Π§ΡΠΎ ΠΌΠΎΠΆΠ½ΠΎ ΡΠ΄Π΅Π»Π°ΡΡ ΠΈΠ· ΡΠ°ΡΠΈΠΊΠΎΠ² ΠΎΡ ΠΏΠΎΠ΄ΡΠΈΠΏΠ½ΠΈΠΊΠ°: Π§ΡΠΎ ΠΌΠΎΠΆΠ½ΠΎ ΡΠ΄Π΅Π»Π°ΡΡ ΠΈΠ· ΠΏΠΎΠ΄ΡΠΈΠΏΠ½ΠΈΠΊΠ°? Β» ΠΠ·ΠΎΠ±ΡΠ΅ΡΠ΅Π½ΠΈΡ ΠΈ ΡΠ°ΠΌΠΎΠ΄Π΅Π»ΠΊΠΈ
Π§ΡΠΎ ΠΌΠΎΠΆΠ½ΠΎ ΡΠ΄Π΅Π»Π°ΡΡ ΠΈΠ· ΠΏΠΎΠ΄ΡΠΈΠΏΠ½ΠΈΠΊΠ°? Β» ΠΠ·ΠΎΠ±ΡΠ΅ΡΠ΅Π½ΠΈΡ ΠΈ ΡΠ°ΠΌΠΎΠ΄Π΅Π»ΠΊΠΈ
Π‘ΠΎΠ΄Π΅ΡΠΆΠ°Π½ΠΈΠ΅
- ΠΡΡΡΠΎΠΉ ΡΡΠ°Π½ΠΎΠΊ ΠΈΠ· ΠΠΎΠ΄ΡΠΈΠΏΠ½ΠΈΠΊΠ° ΡΠ²ΠΎΠΈΠΌΠΈ ΡΡΠΊΠ°ΠΌΠΈ!
- ΠΠ°ΠΊ ΡΠ΄Π΅Π»Π°ΡΡ ΡΠ²Π΅ΡΠ»ΠΎ ΠΈΠ· ΠΏΠΎΠ΄ΡΠΈΠΏΠ½ΠΈΠΊΠ° Π΄Π»Ρ ΡΠ²Π΅ΡΠ»Π΅Π½ΠΈΡ ΠΊΠ°Π»Π΅Π½ΠΎΠΉ ΡΡΠ°Π»ΠΈ
- ΠΠ°ΡΠ΅ΡΠΈΠ°Π»Ρ:
- ΠΠ·Π³ΠΎΡΠΎΠ²Π»Π΅Π½ΠΈΠ΅ ΡΠ²Π΅ΡΠ»Π°
- ΠΠ°ΠΊ ΡΠ°ΠΌΠΎΠΌΡ ΡΠ΄Π΅Π»Π°ΡΡ Π½ΠΎΠΆ ΠΈΠ· ΠΏΠΎΠ΄ΡΠΈΠΏΠ½ΠΈΠΊΠ°, ΠΊΠΎΡΠΎΡΡΠΉ Π±ΡΠ΄Π΅Ρ Π½Π΅ Ρ ΡΠΆΠ΅ ΠΌΠ°Π³Π°Π·ΠΈΠ½Π½ΠΎΠ³ΠΎ
- Π£Π½ΠΈΠ²Π΅ΡΡΠ°Π»ΡΠ½ΡΠΉ ΠΊΡΡΠ³Π»ΠΎΠ³ΠΈΠ± ΠΈΠ· ΠΏΠΎΠ΄ΡΠΈΠΏΠ½ΠΈΠΊΠΎΠ² ΡΠ²ΠΎΠΈΠΌΠΈ ΡΡΠΊΠ°ΠΌΠΈ
ΠΡΡΡΠΎΠΉ ΡΡΠ°Π½ΠΎΠΊ ΠΈΠ· ΠΠΎΠ΄ΡΠΈΠΏΠ½ΠΈΠΊΠ° ΡΠ²ΠΎΠΈΠΌΠΈ ΡΡΠΊΠ°ΠΌΠΈ!
Π― ΠΏΠΎΠΊΠ°ΠΆΡ ΡΡΠΎ ΠΌΠΎΠΆΠ½ΠΎ ΡΠ΄Π΅Π»Π°ΡΡ ΠΈΠ· ΠΏΠΎΠ΄ΡΠΈΠΏΠ½ΠΈΠΊΠ° ΠΈ ΡΡΠ°ΡΡΡ ΠΌΠ΅ΡΠ°Π»Π»ΠΈΡΠ΅ΡΠΊΠΈΡ ΠΎΠ±ΡΠ΅Π·ΠΊΠΎΠ² , ΠΎΡΠ΅ΡΠ΅Π΄Π½Π°Ρ ΡΠ°ΠΌΠΎΠ΄Π΅Π»ΠΊΠ° ΠΏΡΠ΅Π²Π·ΠΎΡΠ»Π° Π²ΡΠ΅ ΠΌΠΎΠΈ ΠΎΠΆΠΈΠ΄Π°Π½ΠΈΡ.
Π’ΠΎΠ²Π°ΡΡ Π΄Π»Ρ ΠΈΠ·ΠΎΠ±ΡΠ΅ΡΠ°ΡΠ΅Π»Π΅ΠΉ Π‘ΡΡΠ»ΠΊΠ° Π½Π° ΠΌΠ°Π³Π°Π·ΠΈΠ½.
Β ΠΠΎΠ½Π΄ΡΠΊΡΠΎΡ Π΄ΠΎΠ»ΠΆΠ΅Π½ Π±ΡΡΡ ΠΈΠ΄Π΅Π°Π»ΡΠ½ΠΎΠΉ ΡΠΎΡΠΌΡ, ΠΊΠ°ΠΊ ΡΠ»ΠΈΡΠΎΡΠΊΠ° Π·Π°Π²ΠΈΡΡΡΠΊΠ°., ΡΠΎΠ²Π½ΡΠΉ ΠΊΡΡΠ³ Ρ Π²ΡΡ
ΠΎΠ΄ΠΎΠΌ, ΠΊΠ°ΠΊ ΡΠΏΠΈΡΠ°Π»ΠΈ ΠΎΡ ΠΊΠΎΠΌΠ°ΡΠΎΠ², ΡΠΎΠ»ΡΠΊΠΎ ΠΌΠ΅Π½ΡΡΠ΅ ΠΊΠΎΠ»Π΅Ρ. Π Ρ Π²Π°Ρ ΠΊΠΎΠ½Π΄ΡΠΊΡΠΎΡ Ρ ΡΠ³Π»Π°ΠΌΠΈ ΠΈ ΠΎΠ²Π°Π»ΡΠ½ΡΠΉ ΠΏΠΎΡΡΠΎΠΌΡ Π·Π°Π²ΠΈΡΠΊΠΈ ΠΏΠΎΠ»ΡΡΠΈΠ»ΠΈΡΡ ΡΠΉΡΠ΅Π²ΠΈΠ΄Π½ΠΎΠΉ ΡΠΎΡΠΌΡ. ΠΠΎΠΏΡΠΎΠ±ΡΠΉΡΠ΅ ΡΠ΄Π΅Π»Π°ΡΡ Π΄ΡΡΠ³ΠΎΠΉ ΠΊΠΎΠ½Π΄ΡΠΊΡΠΎΡ, ΠΈΠ· ΠΏΠΎΠ΄ΠΎΡΠ²Ρ ΠΏΠΎΠ΄ ΠΆΠ΄ ΡΠ΅Π»ΡΡΡ, ΠΊΡΠ΄Π° Π³Π²ΠΎΠ·Π΄ΠΈ Π² ΡΠΏΠ°Π»Ρ Π·Π°Π±ΠΈΠ²Π°ΡΡ. Π’ΠΎΠ»ΡΠΊΠΎ ΠΊΠΎΠ½Π΄ΡΠΊΡΠΎΡ ΡΠ΄Π΅Π»Π°ΠΉΡΠ΅ Π² ΡΠΎΡΠΌΠ΅ ΠΊΠ°ΠΏΠ»ΠΈ Ρ ΠΈΠ·ΠΎΠ³Π½ΡΡΡΠΌ Ρ
Π²ΠΎΡΡΠΈΠΊΠΎΠΌ, ΠΈ Π²ΡΡΠ΅Π·Π°ΡΡ ΠΏΡΠΎΡΠ΅, ΠΈ ΠΏΠ»Π°Π²Π½ΡΠ΅ ΡΠΎΡΠΌΡ ΡΠΌΠΎΡΡΡΡΡΡ Π»ΡΡΡΠ΅, Π΄Π°ΠΆΠ΅ Π΅ΡΠ»ΠΈ ΡΠ°ΠΌ Π±ΡΠ΄Π΅Ρ ΠΎΠ΄ΠΈΠ½ Π·Π°Π²ΠΈΡΠΎΠΊ
ΠΡΡΠΎΡΠ½ΠΈΠΊ
ΠΠ°ΠΊ ΡΠ΄Π΅Π»Π°ΡΡ ΡΠ²Π΅ΡΠ»ΠΎ ΠΈΠ· ΠΏΠΎΠ΄ΡΠΈΠΏΠ½ΠΈΠΊΠ° Π΄Π»Ρ ΡΠ²Π΅ΡΠ»Π΅Π½ΠΈΡ ΠΊΠ°Π»Π΅Π½ΠΎΠΉ ΡΡΠ°Π»ΠΈ
ΠΠ»Π΅ΠΊΡΡΠΎΠ½ΠΈΠΊΠ° Π΄Π»Ρ ΡΠ°ΠΌΠΎΠ΄Π΅Π»ΠΎΠΊ Π²ΠΊΠΈΡΠ°ΠΉΡΠΊΠΎΠΌ ΠΌΠ°Π³Π°Π·ΠΈΠ½Π΅.
ΠΠ°Π»Π΅Π½ΡΡ ΠΈ ΡΠ²Π΅ΡΠ΄ΡΡ ΡΡΠ°Π»Ρ Π±Π΅ΡΠ΅Ρ Π΄Π°Π»Π΅ΠΊΠΎ Π½Π΅ ΠΊΠ°ΠΆΠ΄ΠΎΠ΅ ΡΠ²Π΅ΡΠ»ΠΎ. Π ΡΠ²ΡΠ·ΠΈ Ρ ΡΡΠΈΠΌ ΠΏΡΠΈ Π½Π΅ΠΎΠ±Ρ ΠΎΠ΄ΠΈΠΌΠΎΡΡΠΈ ΠΏΡΠΎΡΠ²Π΅ΡΠ»ΠΈΡΡ ΠΎΠ±ΠΎΠΉΠΌΡ ΠΏΠΎΠ΄ΡΠΈΠΏΠ½ΠΈΠΊΠ°, ΠΊΠ»ΠΈΠ½ΠΎΠΊ Π½ΠΎΠΆΠ° ΠΈΠ»ΠΈ Π΄ΡΡΠ³ΠΈΠ΅ Π·Π°ΠΊΠ°Π»Π΅Π½Π½ΡΠ΅ ΠΈΠ·Π΄Π΅Π»ΠΈΡ Π²ΠΎΠ·Π½ΠΈΠΊΠ°ΡΡ ΡΡΡΠ΄Π½ΠΎΡΡΠΈ. ΠΠ»Ρ ΠΈΡ ΡΠ΅ΡΠ΅Π½ΠΈΡ ΠΌΠΎΠΆΠ½ΠΎ ΡΠ΄Π΅Π»Π°ΡΡ ΡΠ°ΠΌΠΎΠ΄Π΅Π»ΡΠ½ΠΎΠ΅ ΡΠ²Π΅ΡΠ»ΠΎ, ΡΠΏΡΠ°Π²Π»ΡΡΡΠ΅Π΅ΡΡ ΡΠΎ ΡΠ»ΠΎΠΆΠ½ΡΠΌΠΈ Π·Π°Π΄Π°ΡΠ°ΠΌΠΈ.
ΠΠ°ΡΠ΅ΡΠΈΠ°Π»Ρ:
Β
- ΡΠ°ΡΠΈΠΊ ΠΈΠ·-ΠΏΠΎΠ΄ ΠΏΠΎΠ΄ΡΠΈΠΏΠ½ΠΈΠΊΠ°;
- ΡΠ°ΠΌΠΎΡΠ΅Π·.
Β
ΠΠ·Π³ΠΎΡΠΎΠ²Π»Π΅Π½ΠΈΠ΅ ΡΠ²Π΅ΡΠ»Π°
ΠΡΠΆΠ½ΠΎ ΠΏΠΎΠ΄ΠΎΠ±ΡΠ°ΡΡ ΡΠ°ΡΠΈΠΊ ΡΠΎΠΎΡΠ²Π΅ΡΡΡΠ²ΡΡΡΠΈΠΉ Π΄ΠΈΠ°ΠΌΠ΅ΡΡΡ ΡΡΠ΅Π±ΡΠ΅ΠΌΠΎΠ³ΠΎ ΠΎΡΠ²Π΅ΡΡΡΠΈΡ. ΠΠ³ΠΎ ΠΌΠΎΠΆΠ½ΠΎ Π²Π·ΡΡΡ ΠΈΠ· Π½ΠΎΠ²ΠΎΠ³ΠΎ ΠΈΠ»ΠΈ ΡΡΠ°ΡΠΎΠ³ΠΎ ΠΎΡΡΠ°Π±ΠΎΡΠ°Π½Π½ΠΎΠ³ΠΎ ΠΏΠΎΠ΄ΡΠΈΠΏΠ½ΠΈΠΊΠ°. ΠΠ»Ρ Π±ΡΡΡΡΠΎΠ³ΠΎ ΠΈΠ·Π²Π»Π΅ΡΠ΅Π½ΠΈΡ ΠΏΠΎΠ΄ΡΠΈΠΏΠ½ΠΈΠΊ Π»ΡΡΡΠ΅ ΠΎΠ±ΠΌΠΎΡΠ°ΡΡ Π² ΡΠΊΠ°Π½Ρ ΠΈ ΡΠ°Π·Π±ΠΈΡΡ ΠΌΠΎΠ»ΠΎΡΠΊΠΎΠΌ. Π’ΡΡΠΏΠΊΠ° Π½Π΅ ΠΏΠΎΠ·Π²ΠΎΠ»ΠΈΡ ΡΠ°ΡΠΈΠΊΠ°ΠΌ ΡΠ°Π·Π»Π΅ΡΠ΅ΡΡΡΡ ΠΏΠΎ ΠΌΠ°ΡΡΠ΅ΡΡΠΊΠΎΠΉ.
Π ΠΊΠ°ΡΠ΅ΡΡΠ²Π΅ ΠΎΡΠ½ΠΎΠ²Π°Π½ΠΈΡ ΡΠ²Π΅ΡΠ»Π° Π±ΡΠ΄Π΅Ρ ΠΏΡΠΈΠΌΠ΅Π½ΡΡΡΡΡ ΠΎΠ±ΡΡΠ½ΡΠΉ ΡΠ΅ΡΠ½ΡΠΉ ΡΠ°ΠΌΠΎΡΠ΅Π· ΠΏΠΎ Π΄Π΅ΡΠ΅Π²Ρ. ΠΠ»Π°Π²Π½ΠΎΠ΅, ΡΡΠΎΠ±Ρ Π΅Π³ΠΎ Π΄Π»ΠΈΠ½Ρ Ρ Π²Π°ΡΠΈΠ»ΠΎ Π΄Π»Ρ Π½ΡΠΆΠ½ΠΎΠΉ Π³Π»ΡΠ±ΠΈΠ½Ρ ΡΠ²Π΅ΡΠ»Π΅Π½ΠΈΡ. Π¨Π»ΡΠΏΠΊΠ° ΡΠ°ΠΌΠΎΡΠ΅Π·Π° ΠΎΠ±ΡΠ°ΡΠΈΠ²Π°Π΅ΡΡΡ, ΡΡΠΎΠ±Ρ Π΅Π΅ Π΄ΠΈΠ°ΠΌΠ΅ΡΡ ΡΡΠ°Π» Π½Π΅ΠΌΠ½ΠΎΠ³ΠΎ ΠΌΠ΅Π½ΡΡΠ΅, ΡΠ΅ΠΌ ΡΠ°ΡΠΈΠΊ.
Π ΡΠΈΡΠΊΠ°Ρ Π·Π°ΠΆΠΈΠΌΠ°Π΅ΡΡΡ Π½Π΅Π±ΠΎΠ»ΡΡΠ°Ρ Π³Π°Π΅ΡΠΊΠ°, Π½Π° ΠΊΠΎΡΠΎΡΡΡ Π²ΡΡΡΠ°Π²Π»ΡΠ΅ΡΡΡ ΡΠ°ΡΠΈΠΊ. ΠΠ°ΠΉΠΊΠ° ΠΈΡΠΏΠΎΠ»ΡΠ·ΡΠ΅ΡΡΡ ΠΊΠ°ΠΊ Π²ΡΠ΅ΠΌΠ΅Π½Π½Π°Ρ ΠΏΠΎΠ΄ΡΡΠ°Π²ΠΊΠ°, ΠΏΠΎΡΡΠΎΠΌΡ ΠΊΠ°ΡΠ΅ΡΡΠ²ΠΎ Π΅Π΅ ΡΠ΅Π·ΡΠ±Ρ ΠΈ ΡΠΎΡΡΠΎΡΠ½ΠΈΠ΅ Π³ΡΠ°Π½Π΅ΠΉ Π½Π΅ ΠΈΠΌΠ΅Π΅Ρ Π·Π½Π°ΡΠ΅Π½ΠΈΡ.
Π ΡΠ°ΡΠΈΠΊΡ ΠΏΡΠΈΡΡΠ°Π²Π»ΡΠ΅ΡΡΡ Π³ΠΎΠ»ΠΎΠ²ΠΊΠ° ΡΠ°ΠΌΠΎΡΠ΅Π·Π° ΠΈ ΠΎΠ½ΠΈ ΡΠ²Π°ΡΠΈΠ²Π°ΡΡΡΡ Π²ΠΌΠ΅ΡΡΠ΅.
ΠΡΡΡΡΠΏΠ°ΡΡΡΡ Π·Π° Π΄ΠΈΠ°ΠΌΠ΅ΡΡ ΡΠ°ΡΠΈΠΊΠ° ΡΠ²Π°ΡΠΊΡ Π½ΡΠΆΠ½ΠΎ ΡΡΠΎΡΠΈΡΡ Π½Π° Π½Π°ΠΆΠ΄Π°ΠΊΠ΅. ΠΡΠΈ ΡΡΠΎΠΌ ΡΠ°ΠΌΠΎΡΠ΅Π· Π²Π°ΠΆΠ½ΠΎ ΠΏΠΎΠ²ΠΎΡΠ°ΡΠΈΠ²Π°ΡΡ, ΡΡΠΎΠ±Ρ ΠΏΠΎΠ»ΡΡΠΈΡΡ ΡΠΈΠ»ΠΈΠ½Π΄Ρ Π±Π΅Π· ΡΠ³Π»ΠΎΠ².
ΠΠ°ΡΠ΅ΠΌ ΡΠ°ΡΠΈΠΊ ΠΏΠ΅ΡΠ΅ΡΠ°ΡΠΈΠ²Π°Π΅ΡΡΡ ΠΏΠΎΠ΄ ΡΠΏΠΈΡΠ°Π»ΡΠ½ΠΎΠ΅ ΡΠ²Π΅ΡΠ»ΠΎ. ΠΡΠ»ΠΈ Π½ΡΠΆΠ½ΠΎ ΡΠ²Π΅ΡΠ»ΠΈΡΡ ΠΏΠ»ΠΈΡΠΊΡ, ΡΠΎ Π΅ΠΌΡ ΠΏΡΠΈΠ΄Π°Π΅ΡΡΡ ΡΠΎΡΠΌΠ° ΠΏΠ΅ΡΠ°.
ΠΠΎΠ»ΡΡΠΈΠ² Π½ΡΠΆΠ½ΡΡ ΡΠΎΡΠΌΡ, ΡΠ²Π΅ΡΠ»ΠΎ Π·Π°ΠΊΠ°Π»ΡΠ΅ΡΡΡ. Π¨Π°ΡΠΈΠΊ ΠΏΠΎΡΠ»Π΅ ΡΠ²Π°ΡΠΊΠΈ ΠΈ ΠΏΡΠΎΡΠΎΡΠΊΠΈ ΡΠ΅ΡΡΠ΅Ρ ΡΠ²Π΅ΡΠ΄ΠΎΡΡΡ, ΠΏΠΎΡΡΠΎΠΌΡ Π΅Π΅ Π½ΡΠΆΠ½ΠΎ Π²ΠΎΡΡΡΠ°Π½ΠΎΠ²ΠΈΡΡ. ΠΠ»Ρ ΡΡΠΎΠ³ΠΎ ΠΊΠΎΠ½ΡΠΈΠΊ ΡΠ²Π΅ΡΠ»Π° Π³ΡΠ΅Π΅ΡΡΡ Π³Π°Π·ΠΎΠ²ΠΎΠΉ Π³ΠΎΡΠ΅Π»ΠΊΠΎΠΉ Π΄ΠΎ ΠΎΡΠ°Π½ΠΆΠ΅Π²ΠΎΠ³ΠΎ ΡΠ²Π΅ΡΠ° ΠΈ ΠΏΠΎΠ³ΡΡΠΆΠ°Π΅ΡΡΡ Π² ΠΌΠ°ΡΠ»ΠΎ Π½Π° Π½Π΅ΡΠΊΠΎΠ»ΡΠΊΠΎ ΡΠ΅ΠΊΡΠ½Π΄. ΠΡΠΈ ΡΡΠΎΠΌ ΡΠ°ΠΌ ΡΡΡΡΠΏ ΠΈ ΡΠ²Π°ΡΠΊΡ ΠΎΡ
Π»Π°ΠΆΠ΄Π°ΡΡ Π½Π΅ Π½ΡΠΆΠ½ΠΎ, ΡΡΠΎΠ±Ρ ΠΎΠ½ΠΈ Π½Π΅ ΡΡΠ°Π»ΠΈ Ρ
ΡΡΠΏΠΊΠΈΠΌΠΈ.
ΠΠΎΡΠ»Π΅ Π·Π°ΠΊΠ°Π»ΠΊΠΈ Π½Π°ΠΊΠΎΠ½Π΅ΡΠ½ΠΈΠΊ ΡΠ²Π΅ΡΠ»Π° ΠΎΠΊΠΎΠ½ΡΠ°ΡΠ΅Π»ΡΠ½ΠΎ Π·Π°ΡΠ°ΡΠΈΠ²Π°Π΅ΡΡΡ. ΠΠ΅Π»Π°ΡΡ ΡΡΠΎ Π½Π° ΠΎΡΠΏΡΡΠ΅Π½Π½ΠΎΠΌ ΠΌΠ΅ΡΠ°Π»Π»Π΅ Π΄ΠΎ Π·Π°ΠΊΠ°Π»ΠΊΠΈ Π½Π΅ ΡΠ»Π΅Π΄ΡΠ΅Ρ, ΠΏΠΎΡΠΊΠΎΠ»ΡΠΊΡ ΡΠΎΠ³Π΄Π° ΠΊΠ°ΡΠ΅ΡΡΠ²ΠΎ ΡΠ΅ΠΆΡΡΠ΅ΠΉ ΠΊΡΠΎΠΌΠΊΠΈ Π±ΡΠ΄Π΅Ρ Ρ ΡΠΆΠ΅.
ΠΠΎΠ»ΡΡΠ΅Π½Π½ΠΎΠ΅ ΡΠ²Π΅ΡΠ»ΠΎ Ρ ΠΎΡΠΎΡΠΎ ΡΠ²Π΅ΡΠ»ΠΈΡ ΠΏΡΠ°ΠΊΡΠΈΡΠ΅ΡΠΊΠΈ Π»ΡΠ±ΠΎΠΉ ΡΠ²Π΅ΡΠ΄ΡΠΉ ΠΌΠ΅ΡΠ°Π»Π», Π±ΡΠ΄Ρ ΡΠΎ ΠΎΠ±ΠΎΠΉΠΌΠ° ΠΏΠΎΠ΄ΡΠΈΠΏΠ½ΠΈΠΊΠ° ΠΈΠ»ΠΈ Π½Π°ΠΏΠΈΠ»ΡΠ½ΠΈΠΊ. ΠΠ»Π°Π²Π½ΠΎΠ΅ Π΅Π³ΠΎ Π½Π΅ ΠΏΠ΅ΡΠ΅ΠΎΡ Π»Π°ΠΆΠ΄Π°ΡΡ. ΠΡΠ»ΠΈ Π½Π΅Ρ ΠΏΠΎΠ΄ ΡΡΠΊΠΎΠΉ ΠΌΠ°ΡΠ»Π°, ΡΠΎ Π½ΡΠΆΠ½ΠΎ ΠΏΠΎΠ΄Π»ΠΈΠ²Π°ΡΡ Π² ΠΎΡΠ²Π΅ΡΡΡΠΈΠ΅ Ρ ΠΎΡΡ Π±Ρ Π²ΠΎΠ΄Ρ.
ΠΡΠΈ ΡΠ²Π΅ΡΠ»Π΅Π½ΠΈΠΈ ΠΎΡΠ΅Π½Ρ ΡΠΎΠ»ΡΡΡΡ ΡΡΠ°Π»ΡΠ½ΡΡ ΠΏΠ»Π°ΡΡΠΈΠ½, ΡΡΠΎΠ±Ρ Π½Π΅ ΠΌΡΡΠ°ΡΡΡ Ρ ΠΏΠΎΡΡΠΎΡΠ½Π½ΡΠΌ ΠΎΡ Π»Π°ΠΆΠ΄Π΅Π½ΠΈΠ΅ΠΌ, ΠΌΠΎΠΆΠ½ΠΎ ΠΏΠΎΠ»ΠΎΠΆΠΈΡΡ ΡΠ΅Π·ΠΈΠ½ΠΎΠ²ΠΎΠ΅ ΠΊΠΎΠ»ΡΡΠΎ Π²ΠΎΠΊΡΡΠ³ Π½Π°ΠΊΠ΅ΡΠ½Π΅Π½Π½ΠΎΠΉ ΡΠΎΡΠΊΠΈ ΠΈ ΠΏΠΎΠ΄Π»ΠΈΡΡ Π² Π½Π΅Π³ΠΎ Π²ΠΎΠ΄Ρ. ΠΠΈΠ΄ΠΊΠΎΡΡΡ Π±ΡΠ΄Π΅Ρ ΡΠ΄Π΅ΡΠΆΠΈΠ²Π°ΡΡΡΡ Π·Π° ΡΡΠ΅Ρ ΠΏΠΎΠ²Π΅ΡΡ Π½ΠΎΡΡΠ½ΠΎΠ³ΠΎ Π½Π°ΡΡΠΆΠ΅Π½ΠΈΡ ΠΈ ΠΏΠΎΡΡΠΎΡΠ½Π½ΠΎ ΠΎΡ Π»Π°ΠΆΠ΄Π°ΡΡ ΡΠ²Π΅ΡΠ»ΠΎ.
Β
Π‘ΠΌΠΎΡΡΠΈΡΠ΅ Π²ΠΈΠ΄Π΅ΠΎ
sdelaysam-svoimirukami.ru
ΠΠ°ΠΊ ΡΠ°ΠΌΠΎΠΌΡ ΡΠ΄Π΅Π»Π°ΡΡ Π½ΠΎΠΆ ΠΈΠ· ΠΏΠΎΠ΄ΡΠΈΠΏΠ½ΠΈΠΊΠ°, ΠΊΠΎΡΠΎΡΡΠΉ Π±ΡΠ΄Π΅Ρ Π½Π΅ Ρ ΡΠΆΠ΅ ΠΌΠ°Π³Π°Π·ΠΈΠ½Π½ΠΎΠ³ΠΎ
Π‘Π΅Π³ΠΎΠ΄Π½Ρ, Ρ ΡΠ°ΡΡΠΊΠ°ΠΆΡ Π²Π°ΠΌ Π½Π° ΡΡΠΎ ΡΠΏΠΎΡΠΎΠ±Π΅Π½ Π½ΠΎΠΆ ΠΈΠ· ΠΏΠΎΠ΄ΡΠΈΠΏΠ½ΠΈΠΊΠ° ΠΈ ΠΊΠ°ΠΊ Π΅Π³ΠΎ ΡΠ΄Π΅Π»Π°ΡΡ-ΡΡΠΎ Π±Π΅Π·ΡΠΌΠ½Π°Ρ ΠΌΡΡΠ»Ρ, ΠΊΠΎΡΠΎΡΠ°Ρ Π½Π΅ Π΄Π°Π²Π°Π»Π° ΠΌΠ½Π΅ ΡΡΠ½ΡΡΡ ΡΡΡ Π½ΠΎΡΡ, ΡΠ°ΠΊ ΠΊΠ°ΠΊ Π²ΡΠ΅ Π΄Π΅Π»Π°ΡΡ Π½ΠΎΠΆΠΈ ΠΈΠ· Π½Π°ΠΏΠΈΠ»ΡΠ½ΠΈΠΊΠΎΠ², ΠΏΠΎΡΠΎΠΌΡ ΡΡΠΎ ΠΎΠ½ΠΈ ΠΎΡΠ΅Π½Ρ ΠΏΡΠΎΡΠ½ΡΠ΅.
Π ΡΠ΅Π³ΠΎΠ΄Π½Ρ Ρ ΡΠ°ΡΡΠΊΠ°ΠΆΡ Π²Π°ΠΌ, ΠΊΠΎΠ΅-ΡΡΠΎ Π½ΠΎΠ²ΠΎΠ΅ ΠΈ Π½Π΅ Π·Π°Π΅Π·ΠΆΠ΅Π½Π½ΠΎΠ΅, Π° ΠΈΠΌΠ΅Π½Π½ΠΎ Π½ΠΎΠΆ ΠΈΠ· ΠΠΎΠ΄ΡΠΈΠΏΠ½ΠΈΠΊΠ°.
Π ΡΠ°ΠΊ ΠΏΡΠΈΡΡΡΠΏΠΈΠΌ, Π΄Π»Ρ Π½Π°ΡΠ°Π»Π° Π½Π°ΠΌ Π½ΡΠΆΠ΅Π½ ΡΠ°ΠΌ ΠΏΠΎΠ΄ΡΠΈΠΏΠ½ΠΈΠΊ.
Π ΠΈΠΌΠ΅Π½Π½ΠΎ ΡΠ° Π΄Π΅ΡΠ°Π»Ρ, ΠΊΠΎΡΠΎΡΡΡ Π²Ρ Π²ΠΈΠ΄ΠΈΡΠ΅ ΡΠ»Π΅Π²Π° ΠΎΡ ΡΠ΅Π±Ρ.
ΠΠΎΡΠ»Π΅ ΡΠ΅Π³ΠΎ ΠΌΡ ΠΈΠ΄Π΅ΠΌ ΠΊ ΡΠΈΡΠΊΠ°ΠΌ Π·Π°ΠΆΠΈΠΌΠ°Π΅ΠΌ ΠΈ ΠΏΠΈΠ»ΠΈΠΌ.
ΠΠΎΡΠΎΠΌ Π½Π΅ΠΌΠ½ΠΎΠ³ΠΎ Π΅Π΅ ΡΠ°Π·Π³ΠΈΠ±Π°Π΅ΠΌ ΠΈ Π»ΠΎΠΆΠΈΠΌ Π² ΠΏΠ΅ΡΡ.
ΠΠΎΡΠ»Π΅ ΡΠ΅Π³ΠΎ ΠΌΡ Π²ΡΠΏΡΡΠΌΠ»ΡΠ΅ΠΌ Π΄Π΅ΡΠ°Π»Ρ Ρ ΠΏΠΎΠΌΠΎΡΡΡ ΠΌΠΎΠ»ΠΎΡΠΊΠ°, ΠΏΠΎΡΠ»Π΅ ΡΠΎΠ³ΠΎ ΠΊΠ°ΠΊ Π΄Π΅ΡΠ°Π»Ρ Π²ΡΠΏΡΡΠΌΠ»Π΅Π½Π°, ΠΌΡ ΠΈΠ΄Π΅ΠΌ ΠΊ ΡΡΠ°Π½ΠΊΡ Π΄Π΅Π»Π°Π΅ΠΌ ΡΠ°Π·ΠΌΠ΅ΡΠΊΡ Ρ ΠΏΠΎΠΌΠΎΡΡΡ Π·Π°ΡΠ°Π½Π΅Π΅ ΠΏΠΎΠ΄Π³ΠΎΡΠΎΠ²Π»Π΅Π½Π½ΠΎΠ³ΠΎ ΡΡΠ°ΡΠ°ΡΠ΅ΡΠ° ΠΈ Π½Π°ΡΠΈΠ½Π°Π΅ΠΌ Π²ΡΡΠ΅Π·Π°ΡΡ.
ΠΠΎΡΠ»Π΅ ΡΠΎΠ³ΠΎ ΠΊΠ°ΠΊ ΠΌΡ Π²ΡΠ΅ Π²ΡΡΠ΅Π·Π°Π»ΠΈ Ρ ΠΏΠΎΠΌΠΎΡΡΡ Π±ΠΎΠ»Π³Π°ΡΠΊΠΈ Π΅Π΅ Π½ΡΠΆΠ½ΠΎ ΠΎΡΠΏΠΎΠ»ΠΈΡΠΎΠ²Π°ΡΡ ΠΈ Π²ΡΠΏΠΎΠ»Π½ΠΈΡΡ ΡΠ΅ΡΠΌΠΈΡΠ΅ΡΠΊΡΡ ΠΎΠ±ΡΠ°Π±ΠΎΡΠΊΡ Π² ΠΏΠ΅ΡΠΈ +-700-900 Π³ΡΠ°Π΄ΡΡΠΎΠ².
ΠΠΎΡΠ»Π΅ ΡΠ΅Π³ΠΎ ΠΌΡ Π΄ΠΎΠ»ΠΆΠ½Ρ ΠΏΠΎΠΉΠΌΠ°ΡΡ ΡΠ΅ΠΌΠΏΠ΅ΡΠ°ΡΡΡΡ Π² 200 Π³ΡΠ°Π΄ΡΡΠΎΠ² ΠΈ ΠΎΠΏΡΡΡΠΈΡΡ Π½ΠΎΠΆ Π² Π²ΠΎΠ΄Ρ, ΠΏΠΎΡΠ»Π΅ ΡΠ΅Π³ΠΎ Π·Π°ΠΊΠΈΠ½ΡΡΡ Π² ΠΌΠ°ΡΠ»ΠΎ.
ΠΠΎΡΠΎΠΌ ΠΌΡ Π΄ΠΎΠ»ΠΆΠ½Ρ Π·Π°ΠΆΠ°ΡΡ Π·Π°Π³ΠΎΡΠΎΠ²ΠΊΡ Π² ΡΠΈΡΠΊΠ°Ρ ΠΈ ΠΎΠ±ΡΠ°Π±ΠΎΡΠ°ΡΡ Π½ΠΎΠΆ Π½Π°ΠΏΠΈΠ»ΡΠ½ΠΈΠΊΠΎΠΌ.
Π ΠΏΠΎΡΠ»Π΅ ΡΡΠΈΡ
Π²ΡΠ΅Ρ
ΠΌΠ°Π½ΠΈΠΏΡΠ»ΡΡΠΈΠΉ ΠΏΡΠΎΠ²ΠΎΠ΄ΠΈΠΌ ΠΎΡΠΏΡΡΠΊ, Π΅ΡΠ»ΠΈ Π΅Π³ΠΎ Π½Π΅ ΡΠ΄Π΅Π»Π°ΡΡ, ΡΠΎ Π½ΠΎΠΆ Π±ΡΠ΄Π΅Ρ ΠΎΡΠ΅Π½Ρ Ρ
ΡΡΠΏΠΊΠΈΠΌ ΠΈ ΡΠ°Π·ΠΎΠ±ΡΠ΅ΡΡΡ ΠΊΠ°ΠΊ ΡΡΠ΅ΠΊΠ»ΠΎ, Π΅ΡΠ»ΠΈ ΡΡΠΎΠ½ΠΈΡΡ.
ΠΡΠΏΡΡΠΊ Π½ΡΠΆΠ½ΠΎ ΠΏΡΠΎΠ²ΠΎΠ΄ΠΈΡΡ Π² 150 Π³ΡΠ°Π΄ΡΡΠ°Ρ Π² ΠΏΠ΅ΡΠΈ. ΠΠΎΠΆΠΈΠΌΡΡ ΡΠΏΠ°ΡΡ ΠΈ Π½Π° ΡΡΡΠΎ Π΄ΠΎΡΡΠ°Π΅ΠΌ. ΠΠΎ ΡΡΡΠΈ ΡΠ°ΠΌ ΠΊΠ»ΠΈΠ½ΠΎΠΊ ΡΠΆΠ΅ Π³ΠΎΡΠΎΠ².
ΠΠ΅Π»Π°Π΅ΠΌ, ΠΊΠ°ΠΊΡΡ Ρ ΠΎΡΠΈΡΠ΅ ΡΡΠΊΠΎΡΡΡ. ΠΠΎΠΆΠ½ΠΎ Π½Π΅ ΠΏΠ°ΡΠΈΡΡΡΡ ΡΡ ΠΎΠ΄ΠΈΡΡ Π² ΠΌΠ°Π³Π°Π·ΠΈΠ½ ΠΊΡΠΏΠΈΡΡ ΡΠ΅ΡΠΌΠΎΠΏΠ»Π°ΡΡΠΈΠΊ (ΠΎΠ½ Π±ΡΡΡΡΠΎ ΠΏΠ»Π°Π²ΠΈΡΡΡ ΠΈ ΠΏΡΠΈΠ½ΠΈΠΌΠ°Π΅Ρ Π»ΡΠ±ΠΎΠ΅ ΠΏΠΎΠ»ΠΎΠΆΠ΅Π½ΠΈΠ΅). ΠΠΎ ΠΌΡ ΡΠ΄Π΅Π»Π°Π΅ΠΌ ΠΈΠ· Π΄Π΅ΡΠ΅Π²Π°.
ΠΠ°ΡΠ°ΠΆΠΈΠ²Π°Π΅ΠΌ ΠΊΠ»ΠΈΠ½ΠΎΠΊ Π½Π° Π΄Π΅ΡΠ΅Π²ΠΎ, ΠΏΠΎΡΠ»Π΅ ΡΠ΅Π³ΠΎ ΠΎΠ±ΡΠ°Π±Π°ΡΡΠ²Π°Π΅ΠΌ ΠΈ ΠΏΡΠΈΠ΄Π°Π΅ΠΌ ΡΠΎΡΠΌΡ ΡΡΠΊΠΎΡΡΠΈ.
ΠΡ Π² ΠΏΡΠΈΠ½ΡΠΈΠΏΠ΅ Π²ΡΠ΅, Π½ΠΎΠΆ Π³ΠΎΡΠΎΠ². ΠΠΎΠΌΡ ΠΈΠ½ΡΠ΅ΡΠ΅ΡΠ½ΠΎ ΡΡΠ°Π»Ρ, ΠΊΠΎΡΠΎΡΠ°Ρ ΠΈΡΠΏΠΎΠ»ΡΠ·ΡΠ΅ΡΡΡ Π² ΠΈΠ·Π³ΠΎΡΠΎΠ²Π»Π΅Π½ΠΈΠΈ ΠΏΠΎΠ΄ΡΠΈΠΏΠ½ΠΈΠΊΠΎΠ² Π¨Π₯15-Π½Ρ ΡΡΠΎ Ρ ΠΌΠΎΠ³Ρ ΠΏΡΠΎ Π½Π΅Π΅ ΡΠΊΠ°Π·Π°ΡΡ, ΠΎΠ½Π° Π΄ΠΎΠ»Π³ΠΎ Π΄Π΅ΡΠΆΠΈΡ Π·Π°ΡΠΎΡΠΊΡ ΠΈ Π΄ΠΎΡΡΠ°ΡΠΎΡΠ½ΠΎ ΠΏΡΠΎΡΠ½Π°Ρ.
ΠΡΠ»ΠΈ Π²ΡΠ΅ ΠΏΡΠ°Π²ΠΈΠ»ΡΠ½ΠΎ ΡΠ΄Π΅Π»Π°ΡΡ ΠΌΠΎΠΆΠ½ΠΎ ΠΈ Π²Π΅ΡΠΊΠΈ ΡΡΠ±ΠΈΡΡ ΠΈ ΡΠ°Π·Π΄Π΅Π»ΡΠ²Π°ΡΡ ΡΡΡΠΊΠΈ, ΡΡΠΎ Ρ ΠΎΡΠΈΡΠ΅ Π² ΠΎΠ±ΡΠ΅ΠΌ. ΠΠ»Π°Π²Π½ΠΎΠ΅ Π½ΠΈ Π³Π΄Π΅ Π½Π΅ Π½Π°ΠΊΠΎΡΡΡΠΈΡΡ.
Π’Π°ΠΊΠΎΠΉ Π½ΠΎΠΆ Π½Π΅ Ρ ΡΠΆΠ΅, ΡΠΎΠ³ΠΎ ΡΡΠΎ Π²Ρ ΠΊΡΠΏΠΈΡΠ΅ Π² ΠΌΠ°Π³Π°Π·ΠΈΠ½Π΅, Π° Π½Π°ΠΎΠ±ΠΎΡΠΎΡ Π»ΡΡΡΠ΅, ΡΠ°ΠΊ ΠΊΠ°ΠΊ Π±Π»ΠΈΠ·ΠΎΠΊ ΠΊ ΡΠ΅ΡΠ΄ΡΡ. HRC Π±ΡΠ΄Π΅Ρ Π½ΠΈΠΆΠ΅ 60, ΠΏΡΠΈΠΌΠ΅ΡΠ½ΠΎ 56-57.
ΠΡΡΠΎΡΠ½ΠΈΠΊ
Π£Π½ΠΈΠ²Π΅ΡΡΠ°Π»ΡΠ½ΡΠΉ ΠΊΡΡΠ³Π»ΠΎΠ³ΠΈΠ± ΠΈΠ· ΠΏΠΎΠ΄ΡΠΈΠΏΠ½ΠΈΠΊΠΎΠ² ΡΠ²ΠΎΠΈΠΌΠΈ ΡΡΠΊΠ°ΠΌΠΈ
ΠΠ°Π²Π½ΠΎ Ρ
ΠΎΡΠ΅Π»ΠΈ ΡΠ΅Π°Π»ΠΈΠ·ΠΎΠ²Π°ΡΡ ΠΏΡΠΈΡΠΏΠΎΡΠΎΠ±Π»Π΅Π½ΠΈΠ΅ Π΄Π»Ρ ΠΏΡΠΎΠΊΠ°ΡΠΊΠΈ ΠΌΠ΅ΡΠ°Π»Π»ΠΈΡΠ΅ΡΠΊΠΎΠ³ΠΎ ΠΏΡΠΎΡΠΈΠ»Ρ, Π°ΡΠΌΠ°ΡΡΡΡ, ΠΏΠΎΠ»ΠΎΡΡ ΠΈ ΠΏΡΡΡΠ° Π² ΠΊΡΡΠ³. Π Π²ΠΎΡ Π΄Π΅Π»Π°Ρ Π²Π½Π΅ΠΏΠ»Π°Π½ΠΎΠ²ΡΡ ΡΠ±ΠΎΡΠΊΡ Π³Π°ΡΠ°ΠΆΠ° ΠΎΡΡΡΠ»ΠΈ ΠΏΠΎΠ΄ΡΠΈΠΏΠ½ΠΈΠΊΠΈ, ΡΠ³ΠΎΠ»ΠΎΠΊ 40 ΠΌΠΌ ΠΈ ΠΏΠΎΠ»ΡΠΌΡΡΡΡ.
ΠΠΎΠ½ΡΡΡΡΠΊΡΠΈΡ ΡΠ΅ΡΠΈΠ»ΠΈ Π΄Π΅Π»Π°ΡΡ ΠΏΡΠΎΡΡΡΡ, ΠΏΡΠΈΡΠΏΠΎΡΠΎΠ±Π»Π΅Π½Π½ΡΡ ΠΏΠΎΠ΄ ΠΎΠ±ΡΡΠ½ΡΠ΅ ΡΠΈΡΠΊΠΈ. ΠΠ΅ΡΠ²ΡΠΌ Π΄Π΅Π»ΠΎΠΌ ΡΠ΄Π΅Π»Π°Π»ΠΈ ΡΠ°Π·Π΄Π²ΠΈΠΆΠ½ΡΡ ΡΡΠ°Π½ΠΈΠ½Ρ ΠΈΠ· ΡΠ³ΠΎΠ»ΠΊΠ° Π½Π° ΠΌΠ΅ΡΠ°Π»Π»ΠΈΡΠ΅ΡΠΊΠΈΡ Π²ΡΡΠ»ΠΊΠ°Ρ -Π½Π°ΠΏΡΠ°Π²Π»ΡΡΡΠΈΡ . Π Π½Π΅ΠΉ ΠΏΡΠΈΠ²Π°ΡΠΈΠ»ΠΈ Π·Π°Π΄Π½ΠΈΠΉ ΡΡΡΠΏΠΈΡΠ½ΡΠΉ ΠΏΠΎΠ΄ΡΠΈΠΏΠ½ΠΈΠΊ ΠΎΡ ΠΠ°Π΄Ρ-ΠΠ°Π»ΠΈΠ½Ρ. ΠΡΠΎ Π±ΡΠ΄Π΅Ρ ΠΎΡΠ½ΠΎΠ²ΠΎΠΉ Π΄Π»Ρ ΡΡΡΠΊΠΈ ΠΏΡΠΎΠΊΠ°ΡΠ½ΠΎΠ³ΠΎ ΡΡΠ°Π½ΠΊΠ°.
Π§ΡΠΎΠ±Ρ ΠΌΠ΅Ρ Π°Π½ΠΈΠ·ΠΌ ΡΠΏΡΠ°Π²Π»ΡΠ»ΡΡ Ρ ΡΠΈΡΠΎΠΊΠΈΠΌΠΈ ΠΏΠ»Π°ΡΡΠΈΠΊΠ°ΠΌΠΈ Π΅Π³ΠΎ ΡΠ΄Π»ΠΈΠ½ΠΈΠ»ΠΈ Π² Π΄Π²Π° ΡΠ°Π·Π°, ΡΠ°ΡΡ ΠΎΠΌΡΡΠ°Π² Π½Π΅ΠΌΠ½ΠΎΠ³ΠΎ ΡΡΡΠ±Ρ ΠΎΡ ΡΡΠ°ΡΠΎΠ³ΠΎ Π΄ΠΎΠΌΠΊΡΠ°ΡΠ°. ΠΠ°Π»Π΅Π΅ Π·Π°ΠΏΡΠ΅ΡΡΠΎΠ²Π°Π² ΠΏΠΎΠ»ΡΠΌΡΡΡΡ Π² ΠΏΠΎΠ΄ΡΠΈΠΏΠ½ΠΈΠΊΠΈ, Π½Π°ΠΌΠ΅ΡΠΈΠ»ΠΈ ΠΌΠ΅ΡΡΠ° ΡΠ²Π°ΡΠΊΠΈ. ΠΡΠΈΠ²Π°ΡΠΈΠ»ΠΈ ΠΈ ΡΡΡΠ°Π½ΠΎΠ²ΠΈΠ»ΠΈ ΠΏΠΎΠ΄ΡΠΈΠΏΠ½ΠΈΠΊΠΈ Π½Π° ΡΠ²ΠΎΠΈ ΠΌΠ΅ΡΡΠ°. ΠΠΎΡ ΠΈ Π²Π΅ΡΡ ΡΡΠ°Π½ΠΎΠΊ!
Π ΡΡΠΊΡ Π² ΠΈΡΠΎΠ³Π΅ Π²ΡΠ΅-ΡΠ°ΠΊΠΈ ΡΠ΄Π»ΠΈΠ½ΠΈΠ»ΠΈ. ΠΠ° ΡΡΠ°Π»ΡΠ½ΠΎΠΌ ΠΏΡΡΡΠ΅ ΡΠ±Π΅Π΄ΠΈΠ»ΠΈΡΡ ΡΡΠΎ Π²ΡΡ ΡΡΠ° ΡΡΡΠΊΠΎΠ²ΠΈΠ½Π° Π½Π°Π΄Π΅ΠΆΠ½Π° ΠΈ ΡΠ΅Π°Π»ΡΠ½ΠΎ ΡΠ°Π±ΠΎΡΠ°Π΅Ρ. ΠΠ½ΠΎΠ³ΠΎ ΠΏΠΎΠ»Π΅Π·Π½ΠΎΠ³ΠΎ ΠΌΠΎΠΆΠ½ΠΎ ΡΠ΅ΠΏΠ΅ΡΡ Π½Π°ΠΌΡΠ΄ΡΠΈΡΡβ¦ ΠΠ! ΠΡΡΡ ΡΡΠΎ Π΄ΠΎΠ±Π°Π²ΠΈΡΡβ¦ ΠΠΎΠΊΡΠ°ΡΠΈΡΡ ΠΌΠΎΠΆΠ½ΠΎ Π²ΡΠ΅Π³Π΄Π° Π² Π»ΡΠ±ΠΎΠΉ ΡΠ²Π΅Ρ! ΠΠΎ, Π΅ΡΠ»ΠΈ ΡΠ΅ΡΡΠ΅Π·Π½ΠΎ, Π΄ΡΠΌΠ°Ρ ΡΠ΄Π΅Π»Π°ΡΡ ΠΏΠ°Π· Π±ΠΎΠ»Π³Π°ΡΠΊΠΎΠΉ ΠΏΠΎ ΡΠ°Π΄ΠΈΡΡΡ ΡΡΡΠΏΠΈΡΠ½ΠΎΠ³ΠΎ ΠΏΠΎΠ΄ΡΠΈΠΏΠ½ΠΈΠΊΠ°, Π³Π΄Π΅-ΡΠΎ ΠΏΠΎ ΡΠ΅ΡΠ΅Π΄ΠΈΠ½Π΅. ΠΠ°ΠΏΡΠΎΡΠΈΠ² Π½Π°ΡΠΈΡ
ΡΠ΄Π²ΠΎΠ΅Π½Π½ΡΡ
. ΠΡΠΎ Π΄Π»Ρ Π»ΡΡΡΠ΅ΠΉ ΡΠΈΠΊΡΠ°ΡΠΈΠΈ ΠΏΡΡΡΠ°, Π°ΡΠΌΠ°ΡΡΡΡ ΠΈ ΠΏΡΠΎΡΠΈΠ»ΡΠ½ΠΎΠ³ΠΎ ΠΏΡΡΡΠ°. ΠΠ°ΠΊ ΡΠ°Π· ΠΏΡΡΡ Π±ΡΠ΄Π΅Ρ Π»ΠΎΠΆΠΈΡΡΡΡ Π² Π½Π°ΡΠ΅ΡΠΊΠΈ Ρ Π΄Π²ΡΡ
ΡΡΠΎΡΠΎΠ½ ΠΈ Π»ΡΡΡΠ΅ ΡΠΈΠΊΡΠΈΡΠΎΠ²Π°ΡΡΡΡ ΠΏΡΠΈ ΠΏΡΠΎΠΊΠ°ΡΠΊΠ΅.Π’Π°ΠΊ ΠΆΠ΅ ΡΠ΄Π΅Π»Π°Ρ ΡΠ΅Π±ΡΠ° ΠΆΠ΅ΡΡΠΊΠΎΡΡΠΈ Π½Π° ΡΠ³ΠΎΠ»ΠΊΠ΅, Π΄Π°Π±Ρ Π²ΡΠ΅ Π±ΡΠ»ΠΎ ΠΏΠΎ-ΠΌΠΎΡΠ½Π΅Π΅. ΠΡΠ΅ ΡΠ°Π·ΠΌΠ΅ΡΡ Π½Π° ΡΠΎΡΠΎ. ΠΡΠ΅ ΠΊΠ°ΠΊ Π΄Π΅Π»Π°Π»ΠΈ ΠΏΠΎΠ΄ΡΠΎΠ±Π½ΠΎ Π² Π²ΠΈΠ΄Π΅ΠΎ. ΠΠΎΠΆΠ΅Ρ Ρ ΠΊΠΎΠ³ΠΎ Π²ΠΎΠ·Π½ΠΈΠΊΠ½ΡΡ ΠΌΡΡΠ»ΠΈ ΠΏΠΎ Π΄ΠΎΠΏ ΡΠ»ΡΡΡΠ΅Π½ΠΈΡ Π΄Π°Π½Π½ΠΎΠ³ΠΎ ΠΈΠ·Π΄Π΅Π»ΠΈΡ.
Β Β Β Β Β Β Β Β
ΠΠ°ΠΏΠΈΡΡ ΠΏΠΎΠ»ΡΠ·ΠΎΠ²Π°ΡΠ΅Π»Ρ KAS6russiangarag ΠΈΠ· ΡΠΎΠΎΠ±ΡΠ΅ΡΡΠ²Π° Π‘Π΄Π΅Π»Π°ΠΉ Π‘Π°ΠΌ Π½Π° DRIVE2
ΠΡΡΠΎΡΠ½ΠΈΠΊ
Π¨Π°ΡΠΈΠΊΠΈ ΠΈΠ· ΠΏΠΎΠ΄ΡΠΈΠΏΠ½ΠΈΠΊΠΎΠ² ΠΊΠ°ΠΊ ΠΈΡ Π΄Π΅Π»Π°ΡΡ ΠΈ ΠΈΠ· ΡΠ΅Π³ΠΎ
ΠΡΠΎ Π½Π΅ ΠΈΠ³ΡΠ°Π» Π² Π΄Π΅ΡΡΡΠ²Π΅ ΡΠ°ΡΠΈΠΊΠ°ΠΌΠΈ ΠΎΡ ΠΏΠΎΠ΄ΡΠΈΠΏΠ½ΠΈΠΊΠΎΠ²? β ΠΡΠΈΡΡΠ½ΠΎ Π±ΡΠ»ΠΎ Π΄Π΅ΡΠΆΠ°ΡΡ Π² ΡΡΠΊΠ°Ρ
ΠΈΠ΄Π΅Π°Π»ΡΠ½ΠΎ ΡΠΎΠ²Π½ΡΠ΅ ΠΌΠΈΠ½ΠΈ-ΡΡΠ΅ΡΡ, Π³Π»Π°Π΄ΠΊΠΈΠ΅ ΠΈ ΠΈΠ·Π΄Π°ΡΡΠΈΠ΅ ΠΏΡΠΈ Π΄Π²ΠΈΠΆΠ΅Π½ΠΈΠΈ ΠΌΠ΅ΡΠ°Π»Π»ΠΈΡΠ΅ΡΠΊΠΈΠ΅ Π·Π²ΡΠΊΠΈ. ΠΠ°ΠΆΠ΄ΡΠΉ Π² Π΄Π΅ΡΡΡΠ²Π΅ Π²ΠΎΡΡ
ΠΈΡΠ°Π»ΡΡ ΠΈΠΌΠΈ ΠΈ Π΄Π°ΠΆΠ΅ ΡΠ΅Π³ΡΠ»ΡΡΠ½ΠΎ Π·Π°Π΄ΡΠΌΡΠ²Π°Π»ΡΡ, Π° ΠΊΠ°ΠΊ ΡΠ°ΡΠΈΠΊΠΈ Π΄Π»Ρ ΠΏΠΎΠ΄ΡΠΈΠΏΠ½ΠΈΠΊΠΎΠ² ΡΠΎΠ·Π΄Π°ΡΡΡΡ, ΠΈ Π΄ΠΎΡΡΠΈΠ³Π°ΡΡΡΡ ΡΠΏΠ΅ΡΠΈΠ°Π»ΠΈΡΡΠ°ΠΌΠΈ ΡΠ°ΠΊΠΈΠ΅ ΠΈΠ΄Π΅Π°Π»ΡΠ½ΡΠ΅ ΠΏΠ°ΡΠ°ΠΌΠ΅ΡΡΡ ΠΈΠ·Π΄Π΅Π»ΠΈΡ. ΠΠ·ΡΠΎΡΠ»Π΅Ρ, ΠΌΠ½ΠΎΠ³ΠΈΠ΅ ΠΈΠ½ΡΠ΅ΡΠ΅Ρ ΡΠΎΡ
ΡΠ°Π½ΡΡΡ, ΡΠΌΠΎΡΡΡΡ Π²ΠΈΠ΄Π΅ΠΎ, ΠΊΠ°ΠΊ ΡΠ°ΡΠΈΠΊΠΈ Π΄Π»Ρ ΠΏΠΎΠ΄ΡΠΈΠΏΠ½ΠΈΠΊΠΎΠ² ΠΈΠ·Π³ΠΎΡΠ°Π²Π»ΠΈΠ²Π°ΡΡΡΡ, ΠΊΠ°ΠΊΠΈΠ΅ Π΄Π»Ρ ΡΡΠΎΠ³ΠΎ ΠΈΡΠΏΠΎΠ»ΡΠ·ΡΡΡΡΡ ΠΌΠ°ΡΠ΅ΡΠΈΠ°Π»Ρ. Π ΠΎΠΊΠ°Π·ΡΠ²Π°Π΅ΡΡΡ, ΡΠ΅ΠΊΡΠ΅Ρ ΠΏΡΠΎΡΡ, ΠΏΡΠΎΡΡΠΎ Π΅Π³ΠΎ Π½Π°Π΄ΠΎ ΡΠ°Π·Π³Π°Π΄Π°ΡΡ ΠΈ ΠΏΠΎΠ½ΡΡΡ ΠΎΡΠΎΠ±Π΅Π½Π½ΠΎΡΡΠΈ Π²ΡΠ΅Ρ
ΠΏΡΠΎΠΌΡΡΠ»Π΅Π½Π½ΡΡ
ΡΡΠ°ΠΏΠΎΠ² ΠΏΡΠΎΠΈΠ·Π²ΠΎΠ΄ΡΡΠ²Π°. Π Π² ΡΡΠΎΠΉ ΡΡΠ°ΡΡΠ΅ ΠΏΠΎΠΏΡΠΎΠ±ΡΠ΅ΠΌ Π΄Π΅ΡΠ°Π»ΡΠ½ΠΎ ΡΠ°ΡΡΠΌΠΎΡΡΠ΅ΡΡ ΠΏΡΡΡ ΠΏΡΠ΅ΠΎΠ±ΡΠ°Π·ΠΎΠ²Π°Π½ΠΈΡ ΠΎΠ±ΡΡΠ½ΠΎΠΉ ΠΌΠ΅ΡΠ°Π»Π»ΠΈΡΠ΅ΡΠΊΠΎΠΉ ΠΏΡΠΎΠ²ΠΎΠ»ΠΎΠΊΠΈ Π² ΠΈΠ΄Π΅Π°Π»ΡΠ½ΠΎ ΠΎΡΡΠΎΡΠ΅Π½Π½ΡΠ΅ ΡΠ°ΡΠΈΠΊΠΈ Π΄Π»Ρ ΠΏΠΎΠ΄ΡΠΈΠΏΠ½ΠΈΠΊΠΎΠ².
ΠΡΠ½ΠΎΠ²Π½ΡΠ΅ ΡΠ΅Ρ Π½ΠΈΡΠ΅ΡΠΊΠΈΠ΅ Ρ Π°ΡΠ°ΠΊΡΠ΅ΡΠΈΡΡΠΈΠΊΠΈ ΡΠ°ΡΠΈΠΊΠΎΠ² Π΄Π»Ρ ΠΏΠΎΠ΄ΡΠΈΠΏΠ½ΠΈΠΊΠΎΠ²
- ΠΡΠΎΡΠ½ΠΎΡΡΡ. ΠΡΠ²Π΅Ρ Π½Π° Π²ΠΎΠΏΡΠΎΡ,Β ΠΊΠ°ΠΊ Π΄Π΅Π»Π°ΡΡ ΡΠ°ΡΠΈΠΊΠΈ Π΄Π»Ρ ΠΏΠΎΠ΄ΡΠΈΠΏΠ½ΠΈΠΊΠΎΠ²,Β ΠΏΠ΅ΡΠ²ΠΎΠ½Π°ΡΠ°Π»ΡΠ½ΠΎ ΡΠ²ΡΠ·Π°Π½ Ρ Π²ΡΠ±ΠΎΡΠΎΠΌ ΠΌΠ°ΡΠ΅ΡΠΈΠ°Π»Π°, ΡΡΠΎΠ±Ρ ΠΎΠ±Π΅ΡΠΏΠ΅ΡΠΈΡΡ Π΄ΠΎΠ»ΠΆΠ½ΡΡ ΠΏΡΠΎΡΠ½ΠΎΡΡΡ ΠΈΠ·Π΄Π΅Π»ΠΈΡ.
- ΠΠ»Π°Π΄ΠΊΠΎΡΡΡ. ΠΡΠΏΠΎΠ»Π½ΡΠ΅ΡΡΡ ΡΡΠ°ΡΠ΅Π»ΡΠ½ΠΎΠ΅ ΠΎΡΡΠ°ΡΠΈΠ²Π°Π½ΠΈΠ΅ ΠΈ ΡΠ»ΠΈΡΠΎΠ²Π°Π½ΠΈΠ΅ Π΄Π΅ΡΠ°Π»ΠΈ, ΠΏΡΠΎΡΠ°Π±Π°ΡΡΠ²Π°Π΅ΡΡΡ Π½Π° ΡΠΈΠ½Π°Π»ΡΠ½ΡΡ ΡΡΠ°ΠΏΠ°Ρ ΠΏΠΎΠ²Π΅ΡΡ Π½ΠΎΡΡΡ ΡΠ°ΡΠΈΠΊΠΎΠ², ΠΊΠΎΠ³Π΄Π° Π½Π΅ Π΄ΠΎΠΏΡΡΠΊΠ°ΡΡΡΡ ΡΠΊΠΎΠ»Ρ, Π΄Π΅ΡΠΎΡΠΌΠ°ΡΠΈΠΈ, ΠΌΠΈΠΊΡΠΎΡΡΠ΅ΡΠΈΠ½Ρ.
- Π‘ΡΠ΅ΡΠΈΡΠ½ΠΎΡΡΡ. ΠΡΠ°ΠΊΡΠΈΡΠ΅ΡΠΊΠΈ ΠΈΠ΄Π΅Π°Π»ΡΠ½Π°Ρ ΡΠΎΡΠΌΠ° ΡΠ²ΠΎΠΉΡΡΠ²Π΅Π½Π½Π° ΡΠ°ΡΠΈΠΊΠ°ΠΌ Π΄Π»Ρ ΠΏΠΎΠ΄ΡΠΈΠΏΠ½ΠΈΠΊΠ°, Π²ΡΠ΅ ΡΠΎΡΠΊΠΈ ΠΏΠ΅ΡΠΈΡΠ΅ΡΠΈΠΈ ΡΠ°Π²Π½ΠΎΠ·Π½Π°ΡΠ½ΠΎ ΡΠ΄Π°Π»Π΅Π½Ρ ΠΎΡ ΡΠ΅Π½ΡΡΠ°.
- Π’ΠΎΡΠ½ΠΎΡΡΡ. Π¨Π°ΡΠΈΠΊΠΈ Π΄Π»Ρ ΠΏΠΎΠ΄ΡΠΈΠΏΠ½ΠΈΠΊΠ° Π΄ΠΎΠ»ΠΆΠ½Ρ Π±ΡΡΡ ΠΎΠ΄Π½ΠΎΠ³ΠΎ ΡΠ°Π·ΠΌΠ΅ΡΠ°, ΠΏΠΎΡΡΠΎΠΌΡ ΠΏΠΎΠ³ΡΠ΅ΡΠ½ΠΎΡΡΠΈ Π½Π΅ Π΄ΠΎΠΏΡΡΠΊΠ°ΡΡΡΡ. ΠΡΠ΅ ΠΈΠ·Π΄Π΅Π»ΠΈΡ Π²ΡΠΏΠΎΠ»Π½ΡΡΡΡΡ Ρ ΡΠΎΡΠ½ΠΎΡΡΡΡ Π΄ΠΎ Π΄Π΅ΡΡΡΡΡ
Π΄ΠΎΠ»Π΅ΠΉ ΠΌΠΈΠΊΡΠΎΠ½Π°. Π Π½Π΅ ΡΡΠΎΠΈΡ ΡΡΠΈΡΠ°ΡΡ ΡΠ°ΡΠΈΠΊΠΈ ΠΎΠ΄Π½ΠΎΠΉ ΠΈΠ· Π²ΡΠΎΡΠΎΡΡΠ΅ΠΏΠ΅Π½Π½ΡΡ
ΡΠΎΡΡΠ°Π²Π»ΡΡΡΠΈΡ
ΠΏΠΎΠ΄ΡΠΈΠΏΠ½ΠΈΠΊΠ°, Π½Π°ΠΎΠ±ΠΎΡΠΎΡ, ΡΠ°ΡΠΈΠΊ ΠΏΡΠΎΡΡ ΠΏΠΎ ΡΠ²ΠΎΠΈΠΌ Π²Π½Π΅ΡΠ½ΠΈΠΌ ΠΏΠ°ΡΠ°ΠΌΠ΅ΡΡΠ°ΠΌ, Π½ΠΎ ΠΏΡΠΈ ΡΡΠΎΠΌ ΡΡΠΈΡΠ°Π΅ΡΡΡ ΠΊΠ»ΡΡΠ΅Π²ΠΎΠΉ ΠΈ ΡΠ°ΠΌΠΎΠΉ ΡΠ»ΠΎΠΆΠ½ΠΎΠΉ Π² ΡΠ΅Ρ
Π½ΠΈΡΠ΅ΡΠΊΠΎΠΌ ΡΠΌΡΡΠ»Π΅ Π΄Π΅ΡΠ°Π»ΡΡ.
ΠΡ ΠΏΡΠ°Π²ΠΈΠ»ΡΠ½ΠΎΠ³ΠΎ ΡΠ°ΡΠΏΠΎΠ»ΠΎΠΆΠ΅Π½ΠΈΡ ΡΠ°ΡΠΈΠΊΠΎΠ², ΠΈΡ ΡΡΠ½ΠΊΡΠΈΠΎΠ½ΠΈΡΠΎΠ²Π°Π½ΠΈΡ Π·Π°Π²ΠΈΡΠΈΡ ΠΈΠ·Π½ΠΎΡΡΠΎΠΉΠΊΠΎΡΡΡ ΠΏΠΎΠ΄ΡΠΈΠΏΠ½ΠΈΠΊΠ°, ΠΏΡΠ°Π²ΠΈΠ»ΡΠ½Π°Ρ ΡΠ°Π±ΠΎΡΠ° Π°Π³ΡΠ΅Π³Π°ΡΠ° ΠΈΠ»ΠΈ Π»ΡΠ±ΠΎΠ³ΠΎ ΡΡΠ°Π½ΡΠΏΠΎΡΡΠ½ΠΎΠ³ΠΎ ΡΡΠ΅Π΄ΡΡΠ²Π°.
ΠΡΠ½ΠΎΠ²Π½ΡΠ΅ ΡΡΠ°ΠΏΡ Π² ΠΈΠ·Π³ΠΎΡΠΎΠ²Π»Π΅Π½ΠΈΠΈ ΡΠ°ΡΠΈΠΊΠΎΠ² Π΄Π»Ρ ΠΏΠΎΠ΄ΡΠΈΠΏΠ½ΠΈΠΊΠΎΠ²
ΠΠ’ΠΠ ΠΠΠ ΠΠ«Π. ΠΠΎΠ΄Π³ΠΎΡΠΎΠ²ΠΊΠ° Π·Π°Π³ΠΎΡΠΎΠ²ΠΎΠΊ Π΄Π»Ρ ΡΠ°ΡΠΈΠΊΠΎΠ². Π ΠΏΡΠΎΠΌΡΡΠ»Π΅Π½Π½ΡΠΉ ΡΠ΅Ρ
Π΄ΠΎΡΡΠ°Π²Π»ΡΡΡ Π½ΡΠΆΠ½ΠΎΠ΅ ΠΊΠΎΠ»ΠΈΡΠ΅ΡΡΠ²ΠΎ ΡΡΠ°Π»ΡΠ½ΠΎΠΉ ΠΏΡΠΎΠ²ΠΎΠ»ΠΎΠΊΠΈ, ΠΊΠΎΡΠΎΡΠ°Ρ ΠΈΠΌΠ΅Π΅Ρ ΠΎΠ΄ΠΈΠ½Π°ΠΊΠΎΠ²ΡΠΉ ΠΈΠ»ΠΈ Π½Π΅ΠΌΠ½ΠΎΠ³ΠΎ Π±ΠΎΠ»ΡΡΠΈΠΉ Π΄ΠΈΠ°ΠΌΠ΅ΡΡ Ρ Π±ΡΠ΄ΡΡΠΈΠΌ ΡΠ°ΡΠΈΠΊΠΎΠΌ Π΄Π»Ρ ΠΏΠΎΠ΄ΡΠΈΠΏΠ½ΠΈΠΊΠΎΠ². ΠΠ±ΡΡΠ½ΠΎ ΡΡΠ°Π»ΡΠ½ΡΠ΅ ΠΏΡΠΎΠ²ΠΎΠ»ΠΎΠΊΠΈ ΡΡΠΎΡΠΌΠΈΡΠΎΠ²Π°Π½Ρ Π² Π±ΡΡ
ΡΠ°Ρ
, ΠΏΠΎΡΡΠΎΠΌΡ ΠΏΠ΅ΡΠ²ΠΎΠ½Π°ΡΠ°Π»ΡΠ½ΠΎ ΡΠ°Π±ΠΎΡΠΈΠ΅ ΡΠ΅Ρ
Π° ΡΠ°ΡΠΊΡΡΡΠΈΠ²Π°ΡΡ ΡΠ°ΡΡ
ΠΎΠ΄Π½ΡΠ΅ ΠΌΠ°ΡΠ΅ΡΠΈΠ°Π», ΠΏΠΎΠ΄Π³ΠΎΡΠ°Π²Π»ΠΈΠ²Π°ΡΡ Π΅Π³ΠΎ Π΄Π»Ρ ΠΏΠΎΠ΄Π²ΠΎΠ΄Π° ΠΊ ΡΡΠ°ΡΠΈΠΎΠ½Π°ΡΠ½ΠΎΠΌΡ ΡΡΠ°Π½ΠΊΡ ΠΈ ΡΠΊΠ»Π°Π΄ΠΊΠΈ Π΅Π³ΠΎ Π½Π° ΠΏΠΎΠ²Π΅ΡΡ
Π½ΠΎΡΡΡ Π΄Π»Ρ ΠΎΠ±ΡΠ°Π±ΠΎΡΠΊΠΈ ΠΈ ΡΡΠ°ΠΌΠΏΠΎΠ²ΠΊΠΈ ΠΎΠ±ΡΠ°Π·ΡΠΎΠ². Π ΡΠΏΠ΅ΡΠΈΠ°Π»ΠΈΠ·ΠΈΡΠΎΠ²Π°Π½Π½ΡΡ
ΡΠ΅Ρ
Π°Ρ
ΡΡΡΠ°Π½ΠΎΠ²Π»Π΅Π½Ρ Ρ
ΠΎΠ»ΠΎΠ΄Π½ΠΎ-Π²ΡΡΠ°Π΄ΠΎΡΠ½ΡΠ΅ Π°Π²ΡΠΎΠΌΠ°ΡΡ, Π° ΡΠ°ΠΊΠΆΠ΅ ΠΏΠΎΠΏΠ΅ΡΡΠ΅Π½ΠΎ-Π²ΠΈΠ½ΡΠΎΠ²ΡΠ΅ ΠΏΡΠΎΠΊΠ°ΡΠΊΠΈ, Π½Π° ΠΊΠΎΡΠΎΡΡΡ
ΠΈ ΡΠΎΡΠΌΠΈΡΡΡΡΡΡ ΠΏΠ΅ΡΠ²ΠΈΡΠ½ΡΠ΅ ΡΡΠ°Π»ΡΠ½ΡΠ΅ Π·Π°Π³ΠΎΡΠΎΠ²ΠΊΠΈ Π΄Π»Ρ ΠΌΠΈΠ½ΠΈ-ΡΡΠ΅Ρ. Π Π΅ΡΠ»ΠΈ ΠΏΠΎΡΠΌΠΎΡΡΠ΅ΡΡΒ Π²ΠΈΠ΄Π΅ΠΎ ΠΊΠ°ΠΊ Π΄Π΅Π»Π°ΡΡ ΡΠ°ΡΠΈΠΊΠΈ Π΄Π»Ρ ΠΏΠΎΠ΄ΡΠΈΠΏΠ½ΠΈΠΊΠΎΠ² Π²Β ΠΏΡΠΎΠΌΡΡΠ»Π΅Π½Π½ΡΡ
ΠΌΠ°ΡΡΡΠ°Π±Π°Ρ
, ΡΠΎ ΠΌΠΎΠΆΠ½ΠΎ ΡΠ΄ΠΈΠ²ΠΈΡΡΡΡ ΡΠΊΠΎΡΠΎΡΡΠΈ ΡΡΠ°ΠΌΠΏΠΎΠ²ΠΎΡΠ½ΠΎΠ³ΠΎ ΠΊΠΎΠ½Π²Π΅ΠΉΠ΅ΡΠ°. Π’ΠΎΠ»ΡΠΊΠΎ ΠΏΡΠ΅Π΄ΡΡΠ°Π²ΡΡΠ΅, ΡΡΠΎ Π·Π°Π³ΠΎΡΠΎΠ²ΠΊΠΈ ΡΠΎΡΠΌΠΈΡΡΡΡΡΡ ΡΠΎ ΡΠΊΠΎΡΠΎΡΡΡΡ ΠΎΠ΄Π½Π° ΡΡΡΡΡΠ° ΡΡΠ°Π»ΡΠ½ΡΡ
Π΅Π΄ΠΈΠ½ΠΈΡ Π·Π° ΠΎΠ΄Π½Ρ ΠΌΠΈΠ½ΡΡΡ.
ΠΠ’ΠΠ ΠΠ ΠΠ’ΠΠ. ΠΠΎΡΡΠ΅ΠΊΡΠΈΡΠΎΠ²ΠΊΠ° ΡΠΎΡΠΌΡ ΠΈΠ·Π΄Π΅Π»ΠΈΡ. ΠΠ°ΡΡΠ΅ΡΠ° ΠΏΡΠΎΠ΄ΠΎΠ»ΠΆΠ°ΡΡ ΡΠ°Π±ΠΎΡΡ Ρ Π½Π΅ΠΌΠ½ΠΎΠ³ΠΎ ΠΏΡΠΈΠΏΠ»ΡΡΠ½ΡΡΡΠΌΠΈ ΠΈ Π±ΠΎΡΠΎΠ·Π΄ΡΠ°ΡΡΠΌΠΈ ΠΎΠ±ΡΠ°Π·ΡΠ°ΠΌΠΈ. ΠΠ°Π΄Π°ΡΠ° ΡΠΏΠ΅ΡΠΈΠ°Π»ΠΈΡΡΠΎΠ² β ΠΏΡΠΈΠ΄Π°ΡΡ ΡΡΠ΅ΡΠΈΡΠ΅ΡΠΊΡΡ ΡΠΎΡΠΌΡ ΡΠΎΠ·Π΄Π°Π½Π½ΠΎΠΌΡ ΠΎΠ±ΡΠ°Π·ΡΡ. ΠΠ»Ρ ΡΡΠΎΠ³ΠΎ ΡΡΠ°Π»ΡΠ½ΡΠ΅ Π·Π°Π³ΠΎΡΠΎΠ²ΠΊΠΈ ΡΠΈΠΊΡΠΈΡΡΡΡΡΡ Π²ΡΡΡΠ½ΡΡ ΠΌΠ΅ΠΆΠ΄Ρ Π΄Π²ΡΠΌΡ Π΄ΠΈΡΠΊΠΎΠ²ΡΠΌΠΈ ΠΌΠ°ΡΡΠΈΡΠ°ΠΌΠΈ, Π° ΠΊΠΎΠ³Π΄Π° ΠΈΠ·Π΄Π΅Π»ΠΈΠ΅ ΡΡΡΠ°Π½ΠΎΠ²Π»Π΅Π½ΠΎ, ΡΠΎ Π½Π°ΡΠΈΠ½Π°Π΅ΡΡΡ Π΅Π³ΠΎ ΠΎΠ±ΠΊΠ°ΡΠΊΠ° Π΄ΠΎ ΡΠ΅Ρ ΠΏΠΎΡ, ΠΏΠΎΠΊΠ° ΠΎΠ±ΡΠ°Π·Π΅Ρ Π½Π΅ ΠΏΡΠΈΠΎΠ±ΡΠ΅ΡΠ΅Ρ ΡΠ°ΡΠΎΠΎΠ±ΡΠ°Π·Π½ΡΡ ΡΠΎΡΠΌΡ.
ΠΠ½ΡΠ΅ΡΠ΅ΡΠ½ΠΎ Π·Π½Π°ΡΡ! ΠΠΎΠ³Π΄Π° ΡΡΠ°Π»ΡΠ½Π°Ρ Π·Π°Π³ΠΎΡΠΎΠ²ΠΊΠ° Π·Π°ΠΆΠ°ΡΠ° Π² Π³Π½Π΅Π·Π΄Π΅ ΠΎΠ±ΠΊΠ°ΡΠ½ΠΎΠ³ΠΎ ΡΡΠ°Π½ΠΊΠ°, ΡΠΎ Π½Π° Π½Π΅Π΅ ΠΎΡΡΡΠ΅ΡΡΠ²Π»ΡΠ΅ΡΡΡ ΠΌΠ°ΠΊΡΠΈΠΌΠ°Π»ΡΠ½ΠΎΠ΅ Π΄Π°Π²Π»Π΅Π½ΠΈΠ΅ Π² Π΄Π²Π΅ΡΡΠΈ ΡΠΎΠ½Π½.
Π Π·Π°Π²Π΅ΡΡΠ΅Π½ΠΈΠΈ Π²ΡΠΎΡΠΎΠ³ΠΎ ΡΡΠ°ΠΏΠ° ΠΌΠ°ΡΡΠ΅ΡΠ° ΠΏΠΎΠ»ΡΡΠ°ΡΡ Π½Π° ΡΡΠΊΠΈ ΡΠ°ΡΠΈΠΊΠΈ, ΠΊΠΎΡΠΎΡΡΠ΅ ΠΎΡΠ»ΠΈΡΠ°ΡΡΡΡ ΠΎΡ Π·Π°Π³ΠΎΡΠΎΠ²ΠΎΡΠ½ΠΎΠ³ΠΎ Π΄ΠΈΠ°ΠΌΠ΅ΡΡΠ° ΠΏΡΠΎΠ²ΠΎΠ»ΠΎΠΊΠΈ Π² ΡΡΠ΅Π΄Π½Π΅ΠΌ Π½Π° 100 ΠΌΠΈΠΊΡΠΎΠ½, ΡΠΎ Π΅ΡΡΡ ΡΠΈΠΊΡΠΈΡΡΠ΅ΡΡΡ Π½Π΅Π·Π½Π°ΡΠΈΡΠ΅Π»ΡΠ½ΠΎΠ΅ ΠΈ Π½Π΅Π·Π°ΠΌΠ΅ΡΠ½ΠΎΠ΅ Π³Π»Π°Π·Ρ ΠΎΡΠΊΠ»ΠΎΠ½Π΅Π½ΠΈΠ΅ ΠΎΡ Π·Π°Π΄Π°Π½Π½ΡΡ
ΠΏΡΠΎΠΈΠ·Π²ΠΎΠ΄ΠΈΡΠ΅Π»Π΅ΠΌ ΠΏΠ°ΡΠ°ΠΌΠ΅ΡΡΠΎΠ².
Π’Π ΠΠ’ΠΠ ΠΠ’ΠΠ. ΠΠ±ΡΠ°Π±ΠΎΡΠΊΠ° ΡΠ°ΡΠΈΠΊΠΎΠ². Π¨ΡΠ°ΠΌΠΏΠΎΠ²Π°Π½Π½ΡΠ΅ ΠΈ ΠΎΠ±ΠΊΠ°ΡΠ°Π½Π½ΡΠ΅Β ΡΠ°ΡΠΈΠΊΠΈ ΠΏΠΎΠ΄ΡΠΈΠΏΠ½ΠΈΠΊΠΎΠ²ΡΠ΅Β Π² Π΄Π°Π»ΡΠ½Π΅ΠΉΡΠ΅ΠΌ ΠΏΠΎΠ΄Π»Π΅ΠΆΠ°Ρ ΠΎΠ±ΡΠ°Π±ΠΎΡΠΊΠ΅. ΠΠ½ΠΈ ΠΏΠΎΠ΄Π²Π΅ΡΠ³Π°ΡΡΡΡ Π³ΡΡΠ±ΠΎΠΉ Π°Π±ΡΠ°Π·ΠΈΠ²Π½ΠΎΠΉ ΠΎΠ±ΡΠ°Π±ΠΎΡΠΊΠ΅. ΠΠ»Ρ ΡΡΠΎΠ³ΠΎ Π·Π°Π³ΠΎΡΠΎΠ²ΠΊΠΈ ΠΏΠΎΠΌΠ΅ΡΠ°ΡΡΡΡ Π² ΡΠΏΠ΅ΡΠΈΠ°Π»ΡΠ½ΡΠ΅ Π΅ΠΌΠΊΠΎΡΡΠΈ Π±Π°ΡΠ°Π±Π°Π½Π½ΠΎΠ³ΠΎ ΡΠΈΠΏΠ°, Π½Π°ΠΏΠΎΠ»Π½Π΅Π½Π½ΡΠ΅ ΠΌΠ΅Π»ΠΊΠΈΠΌΠΈ ΡΠ°ΡΡΠ½ΠΈΡΠ°ΠΌΠΈ, Π±Π»Π°Π³ΠΎΠ΄Π°ΡΡ ΠΊΠΎΡΠΎΡΡΠΌ ΠΈ ΡΡΠ°ΡΠΈΠ²Π°ΡΡΡΡ Β«ΠΊΠΎΠ»ΡΡΠ° Π‘Π°ΡΡΡΠ½Π°Β», Π»ΠΈΡΠ½ΠΈΠ΅ Π²ΡΡΡΡΠΏΡ.
ΠΠ½ΡΠ΅ΡΠ΅ΡΠ½ΠΎ Π·Π½Π°ΡΡ! ΠΡΠ»ΠΈ ΡΠ°ΡΡΠΌΠ°ΡΡΠΈΠ²Π°ΡΡ ΠΏΠΎΠ΄ΡΠΎΠ±Π½ΠΎ ΠΏΡΠΎΡΠ΅Π΄ΡΡΡ ΠΎΠ±ΡΠ°Π±ΠΎΡΠΊΠΈ ΡΠ°ΡΠΈΠΊΠΎΠ² Π΄Π»Ρ ΠΏΠΎΠ΄ΡΠΈΠΏΠ½ΠΈΠΊΠΎΠ², ΡΠΎ ΠΌΠΎΠΆΠ½ΠΎ ΠΎΠ±ΡΠ°ΡΠΈΡΡ Π²Π½ΠΈΠΌΠ°Π½ΠΈΠ΅ Π½Π° ΠΎΡΠ½ΠΎΠ²Π½ΠΎΠΉ ΠΏΡΠΈΠ΅ΠΌ ΡΠΎΡΠΌΠΈΡΠΎΠ²Π°Π½ΠΈΡ ΠΊΠΎΠ»Π΅Ρ Ρ ΠΎΠ±ΡΠ°Π·ΡΠ°. ΠΠ°ΠΊ ΡΡΠΎ ΠΏΡΠΎΠΈΡΡ ΠΎΠ΄ΠΈΡ? ΠΠΎ-ΠΏΠ΅ΡΠ²ΡΡ , ΠΎΡΠ±ΠΈΡΠ°Π΅ΡΡΡ Π½ΡΠΆΠ½ΠΎΠ³ΠΎ Π΄ΠΈΠ°ΠΌΠ΅ΡΡΠ° ΡΡΠ°Π»ΡΠ½Π°Ρ ΠΏΡΠΎΠ²ΠΎΠ»ΠΎΠΊΠ° ΠΈ ΠΏΡΠΎΠΏΡΡΠΊΠ°Π΅ΡΡΡ ΠΌΠ°ΡΠ΅ΡΠΈΠ°Π» ΡΠ΅ΡΠ΅Π· Π²ΡΡΠ°Π΄ΠΎΡΠ½ΡΠΉ ΡΡΠ°Π½ΠΎΠΊ, Π²Π½ΡΡΡΠΈ ΠΊΠΎΡΠΎΡΠΎΠ³ΠΎ ΠΈΠΌΠ΅ΡΡΡΡ ΡΠΏΠ΅ΡΠΈΠ°Π»ΡΠ½ΡΠ΅ ΠΆΠ΅Π»ΠΎΠ±Π° Π² Π²ΠΈΠ΄Π΅ ΠΏΠΎΠ»ΡΡΡΠ΅Ρ ΡΠ²Π΅ΡΡ Ρ ΠΈ ΡΠ½ΠΈΠ·Ρ. Π ΠΊΠΎΠ³Π΄Π° ΡΡΠ°Π»ΡΠ½ΡΠ΅ Π΄ΠΈΡΠΊΠΈ ΡΡΠ°Π½ΠΊΠ° ΡΠΌΡΠΊΠ°ΡΡΡΡ, ΡΠΎ Π²ΠΎΠΊΡΡΠ³ ΠΎΡΠ½ΠΎΠ²Π½ΠΎΠΉ ΠΏΡΠΎΠ²ΠΎΠ»ΠΎΠΊΠΈ ΠΏΠΎΡΠ²Π»ΡΡΡΡΡ ΠΎΠ±ΠΎΠ΄ΠΊΠΈ. ΠΠΎ-Π²ΡΠΎΡΡΡ , ΠΏΠΎΠ»ΡΡΠ΅Π½Π½ΡΡ Π·Π°Π³ΠΎΡΠΎΠ²ΠΊΡ ΠΏΠΎΠ΄Π²Π΅ΡΠ³Π°ΡΡ Π½Π°Π³ΡΠ΅Π²Ρ ΠΈ Π·Π°ΠΊΠ°Π»ΠΊΠ΅, ΡΡΠΎΠ±Ρ ΠΈΠ·Π΄Π΅Π»ΠΈΡ ΠΎΠ±Π΅ΡΠΏΠ΅ΡΠΈΡΡ ΠΏΡΠΎΡΠ½ΠΎΡΡΡ ΠΈ ΠΈΠ·Π½ΠΎΡΠΎΡΡΡΠΎΠΉΡΠΈΠ²ΠΎΡΡΡ.
Π§ΠΠ’ΠΠΠ Π’Π«Π ΠΠ’ΠΠ. ΠΡΠΈΠ΄Π°Π½ΠΈΠ΅ ΡΡΠ°Π»ΡΠ½ΡΠΌ Π·Π°Π³ΠΎΡΠΎΠ²ΠΊΠ°ΠΌ ΡΠ°ΡΠΎΠΎΠ±ΡΠ°Π·Π½ΠΎΠΉ ΡΠΎΡΠΌΡ. ΠΡΠ΅ ΠΏΠΎΠ΄Π³ΠΎΡΠΎΠ²Π»Π΅Π½Π½ΡΠ΅ ΡΡΠ°Π»ΡΠ½ΡΠ΅ Π·Π°Π³ΠΎΡΠΎΠ²ΠΊΠΈ Π² Π΄Π°Π»ΡΠ½Π΅ΠΉΡΠ΅ΠΉ ΠΎΠ±ΡΠ°Π±ΠΎΡΠΊΠ΅ ΠΏΠΎΠΌΠ΅ΡΠ°ΡΡ Π² ΡΠ°ΡΠΎΠΎΠ±ΡΠ°Π±Π°ΡΡΠ²Π°ΡΡΠΈΠ΅ ΡΡΠ°Π½ΠΊΠΈ, ΠΊΠΎΡΠΎΡΡΠ΅ ΡΠ°Π±ΠΎΡΠ°ΡΡ ΠΏΠΎ ΠΏΡΠΈΠ½ΡΠΈΠΏΡ ΡΡΡΠ΅ΠΌΠΈΡΠ΅Π»ΡΠ½ΠΎΠ³ΠΎ Π²ΡΠ°ΡΠ΅Π½ΠΈΡ ΠΏΠ»Π°Π½ΡΠ°ΠΉΠ±Ρ, ΡΡΠ³ΡΠ½Π½ΡΡ
Π΄ΠΈΡΠΊΠΎΠ² ΡΠΏΠ΅ΡΠΈΠ°Π»ΡΠ½ΠΎΠ³ΠΎ ΡΠ΅ΡΠ΅Π½ΠΈΡ, ΠΈ Π½Π°Π΄Π΅ΠΆΠ½ΠΎΠΉ ΡΠΈΠΊΡΠ°ΡΠΈΠΈ Π½ΠΈΠΆΠ½Π΅ΠΉ ΠΏΠ»Π°ΡΡΠΎΡΠΌΡ. ΠΠ·Π΄Π΅Π»ΠΈΡ ΡΠ°ΠΌ ΠΏΡΠΎΡ
ΠΎΠ΄ΡΡ ΡΠΏΠ΅ΡΠΈΠ°Π»ΡΠ½ΡΡ ΠΎΠ±ΡΠ°Π±ΠΎΡΠΊΡ, Π½Π°Ρ
ΠΎΠ΄ΡΡΡΡ ΠΏΠΎΠ΄ Π΄Π°Π²Π»Π΅Π½ΠΈΠ΅ΠΌ Π² Π΄Π²Π°Π΄ΡΠ°ΡΡ ΡΠΎΠ½Π½. Π ΠΏΡΠΎΡΠ΅ΡΡΠ΅ ΡΡΠ΅ΡΠΈΡΠ΅ΡΠΊΠΈΠ΅ ΠΈΠ·Π΄Π΅Π»ΠΈΡ ΠΌΠ½ΠΎΠ³ΠΎΠΊΡΠ°ΡΠ½ΠΎ ΠΏΡΠΎΠΊΠ°ΡΡΠ²Π°ΡΡΡΡ, ΠΎΡΡΠ°ΡΠΈΠ²Π°ΡΡΡΡ. Π ΠΈΡΠΎΠ³Π΅ ΡΡΠ°Π»ΡΠ½Π°Ρ Π·Π°Π³ΠΎΡΠΎΠ²ΠΊΠ° ΠΈΠΌΠ΅Π΅Ρ ΡΠ΅Π·Π΅ΡΠ²Π½ΡΠΉ Π²Π½Π΅ΡΠ½ΠΈΠΉ ΡΠ»ΠΎΠΉ, ΠΊΠΎΡΠΎΡΡΠΉ ΡΡΡΡ ΠΏΠΎΠ·ΠΆΠ΅ Π±ΡΠ΄Π΅Ρ ΠΏΠΎΠ΄Π²Π΅ΡΠ³Π½ΡΡ ΠΎΠ±ΡΠ°Π±ΠΎΡΠΊΠ΅ Π² ΠΏΡΠΎΡΠ΅ΡΡΠ΅ ΡΠ»ΠΈΡΠΎΠ²Π°Π½ΠΈΡ ΠΈ Π΄ΠΎΠ²ΠΎΠ΄ΠΊΠΈ Π΄ΠΎ Π½ΡΠΆΠ½ΠΎΠ³ΠΎ ΡΠ°Π·ΠΌΠ΅ΡΠ°.
ΠΠ―Π’Π«Π ΠΠ’ΠΠ. Π’Π΅ΡΠΌΠΈΡΠ΅ΡΠΊΠ°Ρ ΠΎΠ±ΡΠ°Π±ΠΎΡΠΊΠ° ΠΈΠ·Π΄Π΅Π»ΠΈΡ. Π‘ΠΎΠ·Π΄Π°Π½Π½ΡΠ΅ ΡΠ°ΡΠΈΠΊΠΈ ΠΏΠΎΠ΄Π²Π΅ΡΠ³Π°ΡΡΡΡ ΡΠΏΠ΅ΡΠΈΠ°Π»ΡΠ½ΠΎΠΉ ΡΠ΅ΡΠΌΠΈΡΠ΅ΡΠΊΠΎΠΉ ΠΎΠ±ΡΠ°Π±ΠΎΡΠΊΠ΅, ΡΠΎ Π΅ΡΡΡ ΠΏΠ΅ΡΠ²ΠΎΠ½Π°ΡΠ°Π»ΡΠ½ΠΎ Π½Π° Π½ΠΈΡ Π²ΠΎΠ·Π΄Π΅ΠΉΡΡΠ²ΡΡΡ Π²ΡΡΠΎΠΊΠΈΠ΅ ΡΠ΅ΠΌΠΏΠ΅ΡΠ°ΡΡΡΡ, ΠΏΠΎΡΠΎΠΌ Π²ΡΠΏΠΎΠ»Π½ΡΠ΅ΡΡΡ ΠΏΡΠΎΠΌΡΡΠ»Π΅Π½Π½ΠΎΠ΅ Π·Π°ΠΊΠ°Π»ΠΈΠ²Π°Π½ΠΈΠ΅ ΠΌΠ΅ΡΠ°Π»Π»Π°, ΠΏΡΠΎΡΠ΅ΡΡ ΠΎΡΠΆΠΈΠ³Π° Π² ΡΠΏΠ΅ΡΠΈΠ°Π»ΡΠ½ΡΡ ΠΏΠ΅ΡΠ°Ρ . Π’Π΅ΡΠΌΠΈΡΠ΅ΡΠΊΠ°Ρ ΠΏΠΎΡΡΠ°ΠΏΠ½Π°Ρ ΠΎΠ±ΡΠ°Π±ΠΎΡΠΊΠ° Π½Π΅ΠΎΠ±Ρ ΠΎΠ΄ΠΈΠΌΠ° ΠΈΠ·Π΄Π΅Π»ΠΈΡ, ΡΡΠΎΠ±Ρ ΡΠ΄Π΅Π»Π°ΡΡ Π΅Π³ΠΎ ΡΠ²Π΅ΡΠ΄ΡΠΌ ΠΈ ΠΈΠ·Π½ΠΎΡΠΎΡΡΠΎΠΉΠΊΠΈΠΌ Π² ΠΏΠ΅ΡΠΈΠΎΠ΄ ΡΠΊΡΠΏΠ»ΡΠ°ΡΠ°ΡΠΈΠΈ.
Π’Π΅ΠΏΠ΅ΡΡ ΡΠΆΠ΅ ΠΌΠΎΠΆΠ½ΠΎ ΠΏΡΠ΅Π΄ΡΡΠ°Π²ΠΈΡΡ, ΠΊΠ°ΠΊ ΠΈΠ·Π³ΠΎΡΠ°Π²Π»ΠΈΠ²Π°ΡΡ ΡΠ°ΡΠΈΠΊΠΈ Π΄Π»Ρ ΠΏΠΎΠ΄ΡΠΈΠΏΠ½ΠΈΠΊΠΎΠ², ΠΊΠ°ΠΊ ΠΏΠΎΡΡΠ°ΠΏΠ½ΠΎ ΡΡΠ°ΡΠ΅Π»ΡΠ½ΠΎ ΠΈ ΠΏΡΠΎΠ΄ΡΠΌΠ°Π½Π½ΠΎ Π²ΡΠΏΠΎΠ»Π½ΡΠ΅ΡΡΡ ΠΎΠ±ΡΠ°Π±ΠΎΡΠΊΠ° ΠΌΠ΅ΡΠ°Π»Π»Π°. ΠΠΎΡΠ»Π΅ ΠΏΠ΅ΡΠ²ΡΡ
ΠΏΡΡΠΈ ΡΡΠ°ΠΏΠΎΠ² ΠΈΠ·Π΄Π΅Π»ΠΈΠ΅ ΠΏΡΠΈΠΎΠ±ΡΠ΅ΡΠ°Π΅Ρ ΡΡΠ΅ΡΠΈΡΠ½ΠΎΡΡΡ, ΡΠ²Π΅ΡΠ΄ΠΎΡΡΡ, Π° ΠΏΠΎΡΠ»Π΅Π΄ΡΡΡΠ΅ΠΌ ΠΏΠΎΡΠ²ΠΈΡΡΡ Π½ΡΠΆΠ½Π°Ρ ΡΠ°Π·ΠΌΠ΅ΡΠ½ΠΎΡΡΡ ΠΈ Π³Π»Π°Π΄ΠΊΠΎΡΡΡ ΠΏΠΎΠ²Π΅ΡΡ
Π½ΠΎΡΡΠΈ.
Π¨ΠΠ‘Π’ΠΠ ΠΠ’ΠΠ. Π¨Π»ΠΈΡΠΎΠ²ΠΊΠ°. Π ΡΠ΅ΡΡΠΎΠΌΡ ΡΡΠ°ΠΏΡ ΡΠ°ΡΠΈΠΊΠΈ ΡΡΠ°Π»ΡΠ½ΡΠ΅ Π΄Π»Ρ ΠΏΠΎΠ΄ΡΠΈΠΏΠ½ΠΈΠΊΠΎΠ² ΡΠΆΠ΅ ΠΏΠΎΠ΄Π³ΠΎΡΠΎΠ²Π»Π΅Π½Ρ β ΠΈΠΌΠ΅ΡΡ Π½ΡΠΆΠ½ΡΡ ΡΠΎΡΠΌΡ, Π²Π½Π΅ΡΠ½ΠΈΠΉ ΡΠ»ΠΎΠΉ Π΄Π»Ρ ΠΏΡΠΎΠ²Π΅Π΄Π΅Π½ΠΈΡ ΡΠ»ΠΈΡΠΎΠ²Π°Π»ΡΠ½ΡΡ ΡΠ°Π±ΠΎΡ, Π½Π΅ΠΎΠ±Ρ ΠΎΠ΄ΠΈΠΌΡΡ ΡΠ²Π΅ΡΠ΄ΠΎΡΡΡ ΠΏΠΎΠ²Π΅ΡΡ Π½ΠΎΡΡΠ΅ΠΉ. Π ΠΏΡΠΎΠΈΠ·Π²ΠΎΠ΄ΡΡΠ²Π΅Π½Π½ΠΎΠΌ ΡΠ΅Ρ Ρ ΠΎΠ±ΡΡΠ½ΠΎ ΠΈΠΌΠ΅ΡΡΡΡ Π² Π½Π°Π»ΠΈΡΠΈΠΈ ΠΈ ΡΠ°ΡΠΎΡΠ»ΠΈΡΠΎΠ²Π°Π»ΡΠ½ΡΠ΅ ΡΡΠ°Π½ΠΊΠΈ, Π² ΠΊΠΎΡΠΎΡΡΡ Π²ΡΠΏΠΎΠ»Π½ΡΠ΅ΡΡΡ ΠΏΠΎΠ΄Π²ΠΎΠ΄ΠΊΠ° Π·Π°Π³ΠΎΡΠΎΠ²ΠΊΠΈ ΠΊ ΡΠΎΡΠ½ΡΠΌ ΠΏΠ°ΡΠ°ΠΌΠ΅ΡΡΠ°ΠΌ. ΠΠ½ΡΡΡΠΈ Π°Π³ΡΠ΅Π³Π°ΡΠΎΠ² ΠΈΠΌΠ΅ΡΡΡΡ ΡΠ²Π΅ΡΡ ΡΠΎΡΠ½ΡΠ΅ ΠΊΠ°Π½Π°Π²ΠΊΠΈ, ΡΠ»ΠΈΡΠΎΠ²Π°Π»ΡΠ½ΡΠ΅ Π΄ΠΈΡΠΊΠΈ, ΠΊ ΠΊΠΎΡΠΎΡΡΠΌ ΡΡΠ°Π»ΡΠ½Π°Ρ Π·Π°Π³ΠΎΡΠΎΠ²ΠΊΠ° ΠΌΠ½ΠΎΠ³ΠΎΠΊΡΠ°ΡΠ½ΠΎ ΠΊΠ°ΡΠ°Π΅ΡΡΡ ΠΈ ΠΏΡΠΈΠΎΠ±ΡΠ΅ΡΠ°Π΅Ρ Π½ΡΠΆΠ½ΡΠ΅ ΡΠΎΡΠΌΡ. ΠΠ½ΠΎΠ³Π΄Π° ΡΠΏΠ΅ΡΠΈΠ°Π»ΠΈΡΡΠ°ΠΌΠΈ ΠΈΡΠΏΠΎΠ»ΡΠ·ΡΠ΅ΡΡΡ Π΄ΠΎΠ²ΠΎΠ΄ΠΊΠ°, Π΅ΡΠ»ΠΈ ΠΏΠΎΡΡΡΠΏΠΈΠ» Π·Π°ΠΊΠ°Π· Π½Π° ΡΠ²Π΅ΡΡ ΡΠΎΡΠ½ΡΠ΅ ΠΈΠ·Π΄Π΅Π»ΠΈΡ.
ΠΠ½ΡΠ΅ΡΠ΅ΡΠ½ΠΎ Π·Π½Π°ΡΡ! Π¨Π»ΠΈΡΠΎΠ²ΠΊΠ° Π²ΡΠΏΠΎΠ»Π½ΡΠ΅ΡΡΡ ΠΊΡΡΠ³ΠΎΠ²ΡΠΌΠΈ Π΄Π²ΠΈΠΆΠ΅Π½ΠΈΡΠΌΠΈ Π΄ΠΎ ΡΠ΅Ρ ΠΏΠΎΡ, ΠΏΠΎΠΊΠ° ΠΎΡ ΡΠ°ΡΠΈΠΊΠΎΠ² Π½Π΅ ΠΎΡΠ΄Π΅Π»ΡΡΡΡ Π²Π΅ΡΡ Π½ΠΈΠ΅ ΠΎΠ±ΠΎΠ΄ΠΊΠΈ, ΠΎΡΡΠ°Π²ΡΠΈΠ΅ΡΡ ΠΏΠΎΡΠ»Π΅ Π²ΡΡΠ°Π΄ΠΎΡΠ½ΠΎΠ³ΠΎ ΡΡΠ°Π½ΠΊΠ°. Π ΠΏΡΠΎΡΠ΅ΡΡΠ΅ ΡΠ»ΠΈΡΠΎΠ²ΠΊΠΈ Π²ΡΠΏΠΎΠ»Π½ΡΠ΅ΡΡΡ ΠΏΠΎΡΡΠ΅ΠΏΠ΅Π½Π½Π°Ρ ΠΏΡΠΎΡΠ°Π±ΠΎΡΠΊΠ° ΠΎΠ±ΡΠ°Π·ΡΠ°, Π΅Π³ΠΎ ΠΏΡΠΎΡ ΠΎΠΆΠ΄Π΅Π½ΠΈΠ΅ ΡΠ΅ΡΠ΅Π· ΠΊΠΎΠ½ΡΡΠΎΠ»ΡΠ½ΡΠ΅ ΠΎΡΠ²Π΅ΡΡΡΠΈΡ, ΡΠΎΠΎΡΠ²Π΅ΡΡΡΠ²ΡΡΡΠΈΠ΅ ΠΊΠΎΠ½ΡΡΠΎΠ»ΡΠ½ΡΠΌ ΠΏΠ°ΡΠ°ΠΌΠ΅ΡΡΠ°ΠΌ ΠΈΠ·Π΄Π΅Π»ΠΈΡ.
Π ΠΈΡΠΎΠ³Π΅ Π²ΡΠΏΠΎΠ»Π½ΡΠ΅ΡΡΡ ΡΠΎΡΠ½Π°Ρ ΡΠΎΡΡΠΈΡΠΎΠ²ΠΊΠ° ΠΎΠ±ΡΠ°Π·ΡΠΎΠ².
Π‘ΠΠΠ¬ΠΠΠ ΠΠ’ΠΠ. ΠΡΠΎΠΌΡΠ²ΠΊΠ° ΡΠ°ΡΠΈΠΊΠΎΠ² Π΄Π»Ρ ΠΏΠΎΠ΄ΡΠΈΠΏΠ½ΠΈΠΊΠΎΠ². ΠΠΎΠ³Π΄Π° ΡΠΆΠ΅ ΠΎΠΏΡΠ΅Π΄Π΅Π»Π΅Π½ΠΎ,Β ΠΊΠ°ΠΊΠΎΠ³ΠΎ Π΄ΠΈΠ°ΠΌΠ΅ΡΡΠ° ΡΠ°ΡΠΈΠΊΠΈ Π² ΠΏΠΎΠ΄ΡΠΈΠΏΠ½ΠΈΠΊΠ°Ρ Β Π΄ΠΎΠ»ΠΆΠ½Ρ Π±ΡΡΡ Π½Π° Π²ΡΡ ΠΎΠ΄Π΅ Ρ ΠΊΠΎΠ½Π²Π΅ΠΉΠ΅ΡΠ°, Π²ΡΠΏΠΎΠ»Π½ΡΠ΅ΡΡΡ ΡΠΈΠ½Π°Π»ΡΠ½Π°Ρ ΠΏΡΠΎΠΌΡΠ²ΠΊΠ° ΠΏΠΎΠ»ΡΡΠ΅Π½Π½ΠΎΠ³ΠΎ ΠΎΠ±ΡΠ°Π·ΡΠ°.
ΠΠΠ‘Π¬ΠΠΠ ΠΠ’ΠΠ. ΠΠΎΠ½ΡΡΠΎΠ»Ρ ΠΈ ΠΏΡΠΎΠ²Π΅ΡΠΊΠ° ΠΏΠΎΠ»ΡΡΠ΅Π½Π½ΠΎΠ³ΠΎ ΠΎΠ±ΡΠ°Π·ΡΠ°. ΠΡΠ΅Π½ΠΈΠ²Π°Π½ΠΈΠ΅ ΠΊΠ°ΡΠ΅ΡΡΠ²Π° ΠΈ ΠΏΡΠΈΠΎΠ±ΡΠ΅ΡΠ΅Π½Π½ΡΡ ΠΏΠ°ΡΠ°ΠΌΠ΅ΡΡΠΎΠ², ΡΠΎΠΎΡΠ½Π΅ΡΠ΅Π½ΠΈΠ΅ ΡΡΠ΅Π±ΠΎΠ²Π°Π½ΠΈΠΉ ΠΊ ΡΠ°ΡΠΈΠΊΠ°ΠΌ ΠΏΠΎΠ΄ΡΠΈΠΏΠ½ΠΈΠΊΠ°.
ΠΠΠΠ―Π’Π«Π ΠΠ’ΠΠ. Π‘ΠΎΡΡΠΈΡΠΎΠ²ΠΊΠ° ΠΈ ΡΠΈΡΡΠ΅ΠΌΠ°ΡΠΈΠ·Π°ΡΠΈΡ ΠΏΠΎΠ»ΡΡΠ΅Π½Π½ΡΡ ΠΎΠ±ΡΠ°Π·ΡΠΎΠ².
ΠΠΠ‘Π―Π’Π«Π ΠΠ’ΠΠ. Π£ΠΏΠ°ΠΊΠΎΠ²ΠΊΠ° ΠΈ Π΄ΠΎΡΡΠ°Π²ΠΊΠ° Π·Π°ΠΊΠ°Π·Π°.
Π’ΡΠ΅Π±ΠΎΠ²Π°Π½ΠΈΡ ΠΊ ΠΏΠΎΠ»ΡΡΠ΅Π½Π½ΡΠΌ ΠΎΠ±ΡΠ°Π·ΡΠ°ΠΌ ΡΠ°ΡΠΈΠΊΠΎΠ² Π΄Π»Ρ ΠΏΠΎΠ΄ΡΠΈΠΏΠ½ΠΈΠΊΠΎΠ²
- Π¨Π°ΡΠΈΠΊΠΈ Π΄ΠΎΠ»ΠΆΠ½Ρ ΠΈΠΌΠ΅ΡΡ Π³Π»Π°Π΄ΠΊΡΡ ΠΈ Π±Π»Π΅ΡΡΡΡΡΡ ΠΏΠΎΠ²Π΅ΡΡ Π½ΠΎΡΡΡ.
- ΠΠΎΠ²Π΅ΡΡ Π½ΠΎΡΡΡ ΠΎΠ±ΡΠ°Π·ΡΠ° Π΄ΠΎΠ»ΠΆΠ½Π° ΠΎΠ±Π»Π°Π΄Π°ΡΡ ΠΈΠ΄Π΅Π°Π»ΡΠ½ΡΠΌ ΡΠΊΠΎΠ»ΡΠΆΠ΅Π½ΠΈΠ΅ΠΌ.
- ΠΠ»Π°Π΄ΠΊΠΎΠ΅ ΠΈ ΠΏΡΠΎΡΠ½ΠΎΠ΅ Π²Π½Π΅ΡΠ½Π΅Π΅ ΠΏΠΎΠΊΡΡΡΠΈΠ΅.
Π’Π°ΠΊΠΈΠΌ ΠΎΠ±ΡΠ°Π·ΠΎΠΌ, ΠΎΡΠ΅Π½Ρ Π²Π°ΠΆΠ½ΠΎ ΠΏΠΎΠ½ΠΈΠΌΠ°ΡΡ, ΠΊΠ°ΠΊ Π΄Π΅Π»Π°ΡΡΡΡ ΡΠ°ΡΠΈΠΊΠΈ Π΄Π»Ρ ΠΏΠΎΠ΄ΡΠΈΠΏΠ½ΠΈΠΊΠΎΠ², Π²Π΅Π΄Ρ ΡΡΠΈ Π½Π΅ Π²ΡΠ΅Π³Π΄Π° Π·Π°ΠΌΠ΅ΡΠ½ΡΠ΅ Π΄Π΅ΡΠ°Π»ΠΈ Π½Π΅ΡΡΡ Π½Π° ΡΠ΅Π±Π΅ ΠΎΡΠ²Π΅ΡΡΡΠ²Π΅Π½Π½ΠΎΡΡΡ Π·Π° ΡΠ°Π±ΠΎΡΡ ΠΏΠΎΠ΄ΡΠΈΠΏΠ½ΠΈΠΊΠ°, Π·Π° Π΄Π»ΠΈΡΠ΅Π»ΡΠ½ΡΠΉ ΡΡΠΎΠΊ ΡΠΊΡΠΏΠ»ΡΠ°ΡΠ°ΡΠΈΠΈ. Π ΡΡΠΎ Π·Π½Π°ΡΠΈΡ, ΡΡΠΎ Π²Π°ΠΆΠ½ΠΎ ΠΊΠΎΠ½ΡΡΠΎΠ»ΠΈΡΠΎΠ²Π°ΡΡ ΡΠ°Π·ΠΌΠ΅ΡΡ ΡΠ°ΡΠΈΠΊΠΎΠ², ΠΈΡ
ΡΠΈΠΏΠΈΡΠ½ΠΎΡΡΡ, Π³Π»Π°Π΄ΠΊΠΎΡΡΡ ΠΈ ΡΠ΅Π»ΠΎΡΡΠ½ΠΎΡΡΡ ΠΏΠΎΠ²Π΅ΡΡ
Π½ΠΎΡΡΠΈ, ΠΎΡ Π½Π°Π·Π²Π°Π½Π½ΡΡ
ΡΠ΅Ρ
Π½ΠΈΡΠ΅ΡΠΊΠΈΡ
Ρ
Π°ΡΠ°ΠΊΡΠ΅ΡΠΈΡΡΠΈΠΊ Π·Π°Π²ΠΈΡΠΈΡ ΡΠ°Π±ΠΎΡΠΎΡΠΏΠΎΡΠΎΠ±Π½ΠΎΡΡΡ ΠΌΠ΅Ρ
Π°Π½ΠΈΠ·ΠΌΠΎΠ², ΡΡΠ°Π½ΡΠΏΠΎΡΡΠ½ΡΡ
ΡΡΠ΅Π΄ΡΡΠ². Π Π΄ΡΠΌΠ°Π΅ΠΌ, ΡΡΠΎ ΠΌΠ½ΠΎΠ³ΠΈΠΌ Π±ΡΠ»ΠΎ ΠΈΠ½ΡΠ΅ΡΠ΅ΡΠ½ΠΎ ΠΏΡΠΎΠ½Π°Π±Π»ΡΠ΄Π°ΡΡ ΠΏΡΡΡ ΡΠΎΡΠΌΠΈΡΠΎΠ²Π°Π½ΠΈΡ ΡΠ°ΡΠΈΠΊΠΎΠ² Π΄Π»Ρ ΠΏΠΎΠ΄ΡΠΈΠΏΠ½ΠΈΠΊΠ° ΠΎΡ ΡΡΠ°Π»ΡΠ½ΠΎΠΉ ΠΏΡΠΎΠ²ΠΎΠ»ΠΎΠΊΠΈ Π΄ΠΎ ΡΠΏΠ°ΠΊΠΎΠ²ΠΎΡΠ½ΠΎΠΉ ΡΠ°ΡΡ, ΠΊ ΠΊΠΎΡΠΎΡΠΎΠΉ ΡΠΆΠ΅ Π³ΠΎΡΠΎΠ²ΡΠΉ ΠΎΠ±ΡΠ°Π·Π΅Ρ ΠΏΠΎΠΏΠ°Π΄Π°Π΅Ρ Π·Π°ΠΊΠ°Π·ΡΠΈΠΊΡ.
ΠΠ΅Π»ΠΈΡΠ΅ΡΡ ΡΠ²ΠΎΠΈΠΌΠΈ Π²ΠΏΠ΅ΡΠ°ΡΠ»Π΅Π½ΠΈΡΠΌΠΈ ΠΈ ΠΆΠΈΠ·Π½Π΅Π½Π½ΡΠΌ ΠΎΠΏΡΡΠΎΠΌ Π² ΠΊΠΎΠΌΠΌΠ΅Π½ΡΠ°ΡΠΈΡΡ ΠΏΠΎΡΠ»Π΅ ΡΡΠ°ΡΡΠΈ, ΠΎΡΡΠ°Π²Π»ΡΠΉΡΠ΅ ΠΎΡΠ·ΡΠ²Ρ ΠΎ ΡΠ°ΡΠΈΠΊΠΎΠ²ΡΡ ΠΏΠΎΠ΄ΡΠΈΠΏΠ½ΠΈΠΊΠ°Ρ .
ΠΠ°ΠΊΠΈΠ΅ ΠΌΠ°ΡΠ΅ΡΠΈΠ°Π»Ρ ΠΈΡΠΏΠΎΠ»ΡΠ·ΡΡΡΡΡ Π΄Π»Ρ ΠΈΠ·Π³ΠΎΡΠΎΠ²Π»Π΅Π½ΠΈΡ ΡΠ°ΡΠΈΠΊΠΎΠΏΠΎΠ΄ΡΠΈΠΏΠ½ΠΈΠΊΠΎΠ²? β ΠΠ»ΠΎΠ³ igus
ΠΠΎΠ΄ΡΠΈΠΏΠ½ΠΈΠΊΠΈ ΡΠΊΠΎΠ»ΡΠΆΠ΅Π½ΠΈΡ
ΠΠ°ΡΡΠΈΠΊ Π§Π°ΠΉΡ | 26. ΠΌΠ°ΡΡ 2020 Π³.
ΠΠ°ΡΠ΅ΡΠΈΠ°Π» Π΄Π»Ρ ΡΠ°ΡΠΈΠΊΠΎΠΏΠΎΠ΄ΡΠΈΠΏΠ½ΠΈΠΊΠΎΠ² ΠΊΠ°ΡΠ΅Π½ΠΈΡ ΡΠΈΡΠΎΠΊΠΎ Π²Π°ΡΡΠΈΡΡΠ΅ΡΡΡ ΠΈ Π²ΡΠ΅Π³Π΄Π° Π² ΠΏΠ΅ΡΠ²ΡΡ ΠΎΡΠ΅ΡΠ΅Π΄Ρ ΠΎΡΠΈΠ΅Π½ΡΠΈΡΠΎΠ²Π°Π½ Π½Π° ΠΌΠ°ΡΠ΅ΡΠΈΠ°Π»Ρ ΠΊΠΎΠ»Π΅Ρ. ΠΡΠΎ ΠΎΠ±Π΅ΡΠΏΠ΅ΡΠΈΠ²Π°Π΅Ρ ΡΠΎΠ³Π»Π°ΡΠΎΠ²Π°Π½Π½ΠΎΠ΅ Π²Π·Π°ΠΈΠΌΠΎΠ΄Π΅ΠΉΡΡΠ²ΠΈΠ΅ ΡΠ΅ΠΏΠ°ΡΠ°ΡΠΎΡΠ°, Π²Π½ΡΡΡΠ΅Π½Π½Π΅Π³ΠΎ ΠΈ Π½Π°ΡΡΠΆΠ½ΠΎΠ³ΠΎ ΠΊΠΎΠ»Π΅Ρ Π² ΡΠΈΡΡΠ΅ΠΌΠ΅. ΠΡΠΎ ΠΎΡΠΎΠ±Π΅Π½Π½ΠΎ Π²Π°ΠΆΠ½ΠΎ, ΠΊΠΎΠ³Π΄Π° ΠΏΡΠΈΠΌΠ΅Π½ΡΠ΅ΡΡΡ Π½Π°Π³ΡΠ΅Π² ΠΈΠ»ΠΈ ΠΎΡ
Π»Π°ΠΆΠ΄Π΅Π½ΠΈΠ΅ ΠΏΠΎΠ΄ΡΠΈΠΏΠ½ΠΈΠΊΠΎΠ². ΠΠ°ΠΆΠ½ΠΎ, ΡΡΠΎΠ±Ρ Ρ
ΠΎΠ΄ΠΎΠ²ΡΠ΅ ΠΊΠ°ΡΠ΅ΡΡΠ²Π° ΡΠ°ΡΠΈΠΊΠΎΠΏΠΎΠ΄ΡΠΈΠΏΠ½ΠΈΠΊΠΎΠ² Π²ΡΠ΅Π³Π΄Π° Π±ΡΠ»ΠΈ Ρ
ΠΎΡΠΎΡΠΈΠΌΠΈ. ΠΠ°ΠΈΠ±ΠΎΠ»Π΅Π΅ ΡΠ°ΡΠΏΡΠΎΡΡΡΠ°Π½Π΅Π½Π½ΡΠ΅ ΠΌΠ°ΡΠ΅ΡΠΈΠ°Π»Ρ Π΄Π»Ρ ΠΌΡΡΠ΅ΠΉ ΠΏΠ΅ΡΠ΅ΡΠΈΡΠ»Π΅Π½Ρ Π½ΠΈΠΆΠ΅ Π² Π·Π°Π²ΠΈΡΠΈΠΌΠΎΡΡΠΈ ΠΎΡ ΠΌΠ°ΡΠ΅ΡΠΈΠ°Π»Π° ΠΊΠΎΠ»ΡΡΠ°.
Π¨Π°ΡΠΈΠΊΠΈ Π΄Π»Ρ ΠΌΠ΅ΡΠ°Π»Π»ΠΈΡΠ΅ΡΠΊΠΈΡ ΡΠ°ΡΠΈΠΊΠΎΠΏΠΎΠ΄ΡΠΈΠΏΠ½ΠΈΠΊΠΎΠ²:
Π‘ΡΠ°Π»Ρ Π΄Π»Ρ ΡΠΎΠ»ΠΈΠΊΠΎΠ²ΡΡ ΠΏΠΎΠ΄ΡΠΈΠΏΠ½ΠΈΠΊΠΎΠ² 1.3505/100Cr6ΠΠ»Ρ ΡΡΠΈΡ ΡΠ°ΡΠΈΠΊΠΎΠΏΠΎΠ΄ΡΠΈΠΏΠ½ΠΈΠΊΠΎΠ² ΡΠ°ΡΡΠΎ ΠΈΡΠΏΠΎΠ»ΡΠ·ΡΡΡΡΡ ΡΠ°ΡΠΈΠΊΠΈ ΠΈΠ· Π·Π°ΠΊΠ°Π»Π΅Π½Π½ΠΎΠΉ ΡΡΠ°Π»ΠΈ. ΠΠ°ΠΈΠ±ΠΎΠ»Π΅Π΅ ΡΠ°ΡΡΠΎ ΠΈΡΠΏΠΎΠ»ΡΠ·ΡΠ΅ΠΌΡΠΌ ΠΌΠ°ΡΠ΅ΡΠΈΠ°Π»ΠΎΠΌ ΡΠ²Π»ΡΠ΅ΡΡΡ Ρ ΡΠΎΠΌΠΈΡΡΠ°Ρ ΡΡΠ°Π»Ρ Ρ ΠΏΡΠΈΠΌΠ΅ΡΠ½ΠΎ 1% ΡΠ³Π»Π΅ΡΠΎΠ΄Π° ΠΈ 1,5% Ρ ΡΠΎΠΌΠ°. Π‘Π²ΠΎΠΉΡΡΠ²Π° ΡΡΠ°Π»ΡΠ½ΡΡ ΡΠ°ΡΠΈΠΊΠΎΠ² ΠΈΠ· ΠΌΠ°ΡΡΠ΅Π½ΡΠΈΡΠ½ΠΎΠΉ Ρ ΡΠΎΠΌΠΈΡΡΠΎΠΉ ΡΡΠ°Π»ΠΈ Π΄Π΅Π»Π°ΡΡ ΠΈΡ ΠΎΡΠΎΠ±Π΅Π½Π½ΠΎ ΠΏΠΎΠ΄Ρ ΠΎΠ΄ΡΡΠΈΠΌΠΈ Π΄Π»Ρ ΠΏΡΠΎΠΈΠ·Π²ΠΎΠ΄ΡΡΠ²Π° ΡΠ°ΡΠΈΠΊΠΎΠΏΠΎΠ΄ΡΠΈΠΏΠ½ΠΈΠΊΠΎΠ², ΠΏΠΎΡΠΊΠΎΠ»ΡΠΊΡ ΠΈΠ· Π½ΠΈΡ ΠΏΠΎΠ»ΡΡΠ°ΡΡΡΡ ΡΡΠ°Π±ΠΈΠ»ΡΠ½ΡΠ΅ ΠΊΠΎΠΌΠΏΠΎΠ½Π΅Π½ΡΡ, ΠΊΠΎΡΠΎΡΡΠ΅ ΡΠ²Π»ΡΡΡΡΡ ΠΏΡΠΎΡΠ½ΡΠΌΠΈ ΠΈ ΡΠ±Π΅Π΄ΠΈΡΠ΅Π»ΡΠ½ΠΎ Π΄ΠΎΠ»Π³ΠΎΠ²Π΅ΡΠ½ΡΠΌΠΈ ΠΏΡΠΈ Π½Π΅ΠΏΡΠ΅ΡΡΠ²Π½ΠΎΠΉ ΡΠΊΡΠΏΠ»ΡΠ°ΡΠ°ΡΠΈΠΈ. Π¨Π°ΡΠΈΠΊΠΈ ΠΈΠ· ΡΠΎΠ»ΠΈΠΊΠΎΠΏΠΎΠ΄ΡΠΈΠΏΠ½ΠΈΠΊΠΎΠ²ΠΎΠΉ ΡΡΠ°Π»ΠΈ ΠΏΡΠΎΡΠ½ΡΠΉ ΠΈ ΠΏΡΠΎΡΠ½ΡΠΉ . ΠΠΎΠ΄Π²Π΅ΡΠΆΠ΅Π½Π½ΠΎΡΡΡ ΠΊΠΎΡΡΠΎΠ·ΠΈΠΈ, ΠΊΠ°ΠΊ ΠΏΡΠ°Π²ΠΈΠ»ΠΎ, Π½ΠΈΠ·ΠΊΠ°Ρ, ΠΏΠΎΡΡΠΎΠΌΡ ΡΠΈΠ»ΠΈΠ½Π΄ΡΠΈΡΠ΅ΡΠΊΠΈΠ΅ ΡΠΎΠ»ΠΈΠΊΠΈ ΠΈ ΠΈΠ³ΠΎΠ»ΡΡΠ°ΡΡΠ΅ ΡΠΎΠ»ΠΈΠΊΠΈ ΠΈΠ·Π³ΠΎΡΠ°Π²Π»ΠΈΠ²Π°ΡΡΡΡ ΠΈΠ· ΡΡΠΎΠ³ΠΎ ΠΌΠ°ΡΠ΅ΡΠΈΠ°Π»Π°. ΠΠΎ Π±Π΅Π· ΡΠΌΠ°Π·ΠΊΠΈ Π½Π΅ ΠΎΠ±ΠΎΠΉΡΠΈΡΡ.
Π¨Π°ΡΠΈΠΊΠΈ Π΄Π»Ρ ΠΏΠ»Π°ΡΡΠΌΠ°ΡΡΠΎΠ²ΡΡ ΡΠ°ΡΠΈΠΊΠΎΠΏΠΎΠ΄ΡΠΈΠΏΠ½ΠΈΠΊΠΎΠ²
ΠΠ΅ΡΠΆΠ°Π²Π΅ΡΡΠ°Ρ ΡΡΠ°Π»Ρ 1.
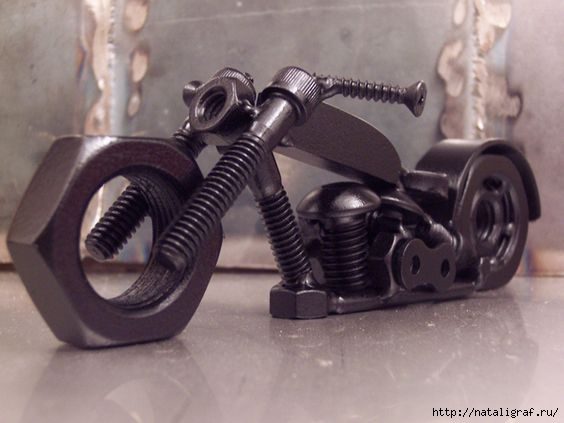
ΠΠ»Ρ ΠΏΠ»Π°ΡΡΠΌΠ°ΡΡΠΎΠ²ΡΡ ΡΠ°ΡΠΈΠΊΠΎΠΏΠΎΠ΄ΡΠΈΠΏΠ½ΠΈΠΊΠΎΠ² ΠΎΠ±ΡΡΠ½ΠΎ ΠΈΡΠΏΠΎΠ»ΡΠ·ΡΡΡΡΡ Π½Π΅Π·Π°ΠΊΠ°Π»Π΅Π½Π½ΡΠ΅ ΡΠ°ΡΠΈΠΊΠΈ ΠΈΠ· Π½Π΅ΡΠΆΠ°Π²Π΅ΡΡΠ΅ΠΉ ΡΡΠ°Π»ΠΈ. ΠΠ½ΠΈ ΠΈΡΠΊΠ»ΡΡΠΈΡΠ΅Π»ΡΠ½ΠΎ ΡΡΡΠΎΠΉΡΠΈΠ²Ρ ΠΊ ΠΊΠΎΡΡΠΎΠ·ΠΈΠΈ, Π° ΡΠ°ΠΊΠΆΠ΅ ΠΎΡΠ΅Π½Ρ ΡΡΡΠΎΠΉΡΠΈΠ²Ρ ΠΊ ΡΠΎΠ»Π΅Π½ΠΎΠΉ Π²ΠΎΠ΄Π΅ ΠΈ ΡΠ΅Π»ΠΎΡΠ°ΠΌ. ΠΠ»Ρ ΠΏΠ»Π°ΡΡΠΌΠ°ΡΡΠΎΠ²ΡΡ ΡΠ°ΡΠΈΠΊΠΎΠΏΠΎΠ΄ΡΠΈΠΏΠ½ΠΈΠΊΠΎΠ² Π½Π΅Ρ Π½Π΅ΠΎΠ±Ρ ΠΎΠ΄ΠΈΠΌΠΎΡΡΠΈ ΠΈΡΠΏΠΎΠ»ΡΠ·ΠΎΠ²Π°ΡΡ Π·Π°ΠΊΠ°Π»Π΅Π½Π½ΡΠ΅ ΡΠ°ΡΠΈΠΊΠΈ. ΠΠ°ΠΊΡΠΈΠΌΠ°Π»ΡΠ½ΠΎ Π΄ΠΎΠΏΡΡΡΠΈΠΌΠ°Ρ Π½Π°Π³ΡΡΠ·ΠΊΠ° ΡΠΆΠ΅ ΠΎΠ³ΡΠ°Π½ΠΈΡΠ΅Π½Π° ΠΏΡΠ΅Π΄Π΅Π»Π°ΠΌΠΈ ΠΌΠ°ΡΠ΅ΡΠΈΠ°Π»Π° ΠΏΠ»Π°ΡΡΠΈΠΊΠΎΠ²ΡΡ ΠΊΠΎΠ»Π΅Ρ. Π¨Π°ΡΠΈΠΊΠΈ ΠΈΠ· Π½Π΅ΡΠΆΠ°Π²Π΅ΡΡΠ΅ΠΉ ΡΡΠ°Π»ΠΈ ΡΡΠΎΡΡ ΠΌΠ΅Π½ΡΡΠ΅, ΡΠ΅ΠΌ ΡΡΠ΅ΠΊΠ»ΡΠ½Π½ΡΠ΅.
Π¨Π°ΡΠΈΠΊΠΈ ΡΠ°ΡΠΈΠΊΠΎΠΏΠΎΠ΄ΡΠΈΠΏΠ½ΠΈΠΊΠΎΠ² ΠΈΠ· Π½Π΅ΡΠΆΠ°Π²Π΅ΡΡΠ΅ΠΉ ΡΡΠ°Π»ΠΈ Π΄Π»Ρ ΠΏΠΎΠ»ΠΈΠΌΠ΅ΡΠ½ΡΡ ΡΠ°ΡΠΈΠΊΠΎΠΏΠΎΠ΄ΡΠΈΠΏΠ½ΠΈΠΊΠΎΠ² xiros ΠΠ·Π²Π΅ΡΡΠΊΠΎΠ²ΠΎ-Π½Π°ΡΡΠΈΠ΅Π²ΠΎΠ΅ ΡΡΠ΅ΠΊΠ»ΠΎ Π‘ΡΠ΅ΠΊΠ»ΡΠ½Π½ΡΠ΅ ΡΠ°ΡΠΈΠΊΠΈ ΠΈΡΠΏΠΎΠ»ΡΠ·ΡΡΡΡΡ , ΠΊΠΎΠ³Π΄Π° ΠΈ Π±Π΅Π·ΠΌΠ΅ΡΠ°Π»Π»ΠΎΠ²ΡΠ΅ ΡΠ°ΡΠΈΠΊΠΎΠΏΠΎΠ΄ΡΠΈΠΏΠ½ΠΈΠΊΠΈ Π½Π΅ΠΎΠ±Ρ
ΠΎΠ΄ΠΈΠΌΡ ΠΈΠ»ΠΈ Π²ΡΠΏΠΎΠ»Π½ΡΡΡΡΡ ΡΡΠ΅Π±ΠΎΠ²Π°Π½ΠΈΡ ΠΏΠΎ Ρ
ΠΈΠΌΠΈΡΠ΅ΡΠΊΠΎΠΉ ΡΡΠΎΠΉΠΊΠΎΡΡΠΈ Π²ΡΡΠΎΠΊΠΈΠΉ. ΠΠ·Π²Π΅ΡΡΠΊΠΎΠ²ΠΎ-Π½Π°ΡΡΠΈΠ΅Π²ΠΎΠ΅ ΡΡΠ΅ΠΊΠ»ΠΎ ΠΈΡΠΏΠΎΠ»ΡΠ·ΡΠ΅ΡΡΡ Π΄Π»Ρ ΠΈΠ·Π³ΠΎΡΠΎΠ²Π»Π΅Π½ΠΈΡ Π±ΡΡΡΠ»ΠΎΠΊ, ΡΡΠ°ΠΊΠ°Π½ΠΎΠ² ΠΈ Π»ΠΈΡΡΠΎΠ²ΠΎΠ³ΠΎ ΡΡΠ΅ΠΊΠ»Π°, Π° ΡΠ°ΠΊΠΆΠ΅ Π² ΠΊΠ°ΡΠ΅ΡΡΠ²Π΅ ΠΌΠ°ΡΠ΅ΡΠΈΠ°Π»Π° Π΄Π»Ρ ΡΠ°ΡΠΈΠΊΠΎΠΏΠΎΠ΄ΡΠΈΠΏΠ½ΠΈΠΊΠΎΠ². ΠΠ½ ΠΈΠΌΠ΅Π΅Ρ Ρ
ΠΎΡΠΎΡΠΈΠ΅ Ρ
ΠΈΠΌΠΈΡΠ΅ΡΠΊΠΈΠ΅ ΡΠ²ΠΎΠΉΡΡΠ²Π° ΠΏΠΎΠ΄Ρ
ΠΎΠ΄ΠΈΡ Π΄Π»Ρ ΡΠ°ΡΠΈΠΊΠΎΠΏΠΎΠ΄ΡΠΈΠΏΠ½ΠΈΠΊΠΎΠ², ΠΊΠΎΡΠΎΡΡΠ΅ ΠΎΠ±ΡΡΠ½ΠΎ 0011 ΠΏΠΎΠ΄Π²Π΅ΡΠ³Π°Π΅ΡΡΡ ΠΊΡΠ°ΡΠΊΠΎΠ²ΡΠ΅ΠΌΠ΅Π½Π½ΠΎΠΌΡ Ρ
ΠΈΠΌΠΈΡΠ΅ΡΠΊΠΎΠΌΡ Π²ΠΎΠ·Π΄Π΅ΠΉΡΡΠ²ΠΈΡ , Π½ΠΎ Π½Π΅ ΡΠΈΠ»ΡΠ½ΠΎΠΌΡ ΡΠ΅ΡΠΌΠΈΡΠ΅ΡΠΊΠΎΠΌΡ Π²ΠΎΠ·Π΄Π΅ΠΉΡΡΠ²ΠΈΡ. ΠΠ³ΠΎ ΡΠ²Π΅ΡΠ»ΠΎ-Π·Π΅Π»Π΅Π½ΡΠΉ ΡΠ²Π΅Ρ ΡΠ°ΠΊΠΆΠ΅ Π΄Π°Π» Π΅ΠΌΡ Π½Π°Π·Π²Π°Π½ΠΈΠ΅ Π»ΠΈΠΌΠΎΠ½Π½ΠΎΠ΅ ΡΡΠ΅ΠΊΠ»ΠΎ .
ΠΡΠΎΡ ΡΠΈΠΏ ΡΡΠ΅ΠΊΠ»Π° Π½Π°ΠΌΠ½ΠΎΠ³ΠΎ Π΄ΠΎΡΠΎΠΆΠ΅ ΠΈΠ·Π²Π΅ΡΡΠΊΠΎΠ²ΠΎ-Π½Π°ΡΡΠΈΠ΅Π²ΠΎΠ³ΠΎ ΡΡΠ΅ΠΊΠ»Π° . ΠΠΎΡΠΎΡΠΈΠ»ΠΈΠΊΠ°ΡΠ½ΠΎΠ΅ ΡΡΠ΅ΠΊΠ»ΠΎ Π΄Π°ΠΆΠ΅ Π±ΠΎΠ»Π΅Π΅ Ρ ΠΈΠΌΠΈΡΠ΅ΡΠΊΠΈ ΡΡΠΎΠΉΠΊΠΎΠ΅, ΡΠ΅ΠΌ ΠΈΠ·Π²Π΅ΡΡΠΊΠΎΠ²ΠΎ-Π½Π°ΡΡΠΈΠ΅Π²ΠΎΠ΅ ΡΡΠ΅ΠΊΠ»ΠΎ, Π° ΡΡΠΎ ΠΎΠ·Π½Π°ΡΠ°Π΅Ρ, ΡΡΠΎ ΠΎΠ½ΠΎ ΠΈΡΠΏΠΎΠ»ΡΠ·ΡΠ΅ΡΡΡ Π² ΠΏΡΠΈΠ»ΠΎΠΆΠ΅Π½ΠΈΡΡ , ΡΠ²ΡΠ·Π°Π½Π½ΡΡ Ρ ΡΠΈΠ»ΡΠ½ΡΠΌΠΈ ΠΊΠΈΡΠ»ΠΎΡΠ°ΠΌΠΈ .
ΠΡΡΠ³ΠΈΠ΅ ΠΏΡΠ΅ΠΈΠΌΡΡΠ΅ΡΡΠ²Π°:
- ΠΡΠ΅Π½Ρ Ρ ΠΎΡΠΎΡΠ°Ρ ΡΠ΅ΡΠΌΠΎΡΡΠΎΠΉΠΊΠΎΡΡΡ ΠΈ ΡΡΡΠΎΠΉΡΠΈΠ²ΠΎΡΡΡ ΠΊ ΠΈΠ·ΠΌΠ΅Π½Π΅Π½ΠΈΡΠΌ ΡΠ΅ΠΌΠΏΠ΅ΡΠ°ΡΡΡΡ
- ΠΠ΅Ρ Π°Π½ΠΈΡΠ΅ΡΠΊΠ°Ρ ΡΡΠ°Π±ΠΈΠ»ΡΠ½ΠΎΡΡΡ
- ΠΠΈΠ·ΠΊΠΈΠΉ ΠΊΠΎΡΡΡΠΈΡΠΈΠ΅Π½Ρ Π»ΠΈΠ½Π΅ΠΉΠ½ΠΎΠ³ΠΎ ΡΠ°ΡΡΠΈΡΠ΅Π½ΠΈΡ
ΠΡΠΎΡ ΡΠΈΠΏ ΠΏΡΠΎΠ·ΡΠ°ΡΠ½ΡΠΉ ΠΈ ΠΏΡΠΎΠ·ΡΠ°ΡΠ½ΡΠΉ.
Π¨Π°ΡΠΈΠΊΠΈ Π΄Π»Ρ ΠΊΠ΅ΡΠ°ΠΌΠΈΡΠ΅ΡΠΊΠΈΡ ΡΠ°ΡΠΈΠΊΠΎΠΏΠΎΠ΄ΡΠΈΠΏΠ½ΠΈΠΊΠΎΠ²:
ΠΠΊΡΠΈΠ΄ Π°Π»ΡΠΌΠΈΠ½ΠΈΡ Al2O3 ΠΠ΅ΡΠ°ΠΌΠΈΡΠ΅ΡΠΊΠΈΠ΅ ΡΠ°ΡΠΈΠΊΠΈ ΠΈΠ· ΠΎΠΊΡΠΈΠ΄Π° Π°Π»ΡΠΌΠΈΠ½ΠΈΡ, ΡΠ°ΠΊΠΆΠ΅ ΠΈΠ·Π²Π΅ΡΡΠ½ΡΠ΅ ΠΊΠ°ΠΊ ΠΎΠΊΡΠΈΠ΄Π½Π°Ρ ΠΊΠ΅ΡΠ°ΠΌΠΈΠΊΠ°, ΠΈΠΌΠ΅ΡΡ ΠΏΠΎΠ»ΠΈΠΊΡΠΈΡΡΠ°Π»Π»ΠΈΡΠ΅ΡΠΊΡΡ ΡΡΡΡΠΊΡΡΡΡ. Π‘Π²ΠΎΠΉΡΡΠ²Π° Π»Π΅Π³ΠΊΠΈΡ
ΡΠ°ΡΠΈΠΊΠΎΠ² Π²ΠΊΠ»ΡΡΠ°ΡΡ Ρ
ΠΎΡΠΎΡΡΡ ΠΊΠΎΡΡΠΎΠ·ΠΈΠΎΠ½Π½ΡΡ ΡΡΠΎΠΉΠΊΠΎΡΡΡ, ΡΡΠΎΠΉΠΊΠΎΡΡΡ ΠΊ ΠΈΡΡΠΈΡΠ°Π½ΠΈΡ ΠΈ ΡΠ΅ΡΠΌΠΎΡΡΠΎΠΉΠΊΠΎΡΡΡ. ΠΠ΅ΡΠΌΠΎΡΡΡ Π½Π° ΡΠ°ΠΊΠΈΠ΅ Π²Π»ΠΈΡΠ½ΠΈΡ, ΠΊΠ°ΠΊ Π²ΠΎΠ΄Π°, ΡΠ°ΡΡΠ²ΠΎΡΡ ΡΠΎΠ»Π΅ΠΉ ΠΈ Π½Π΅ΠΊΠΎΡΠΎΡΡΠ΅ ΠΊΠΈΡΠ»ΠΎΡΡ , ΠΎΠ½ΠΈ ΡΡΠ΅Π·Π²ΡΡΠ°ΠΉΠ½ΠΎ ΡΡΡΠΎΠΉΡΠΈΠ²Ρ ΠΊ ΠΊΠΎΡΡΠΎΠ·ΠΈΠΈ. ΠΠ°ΠΆΠ½ΠΎ ΠΈΠ·Π±Π΅Π³Π°ΡΡ ΠΊΠΎΠ½ΡΠ°ΠΊΡΠ° Ρ ΠΏΠ»Π°Π²ΠΈΠΊΠΎΠ²ΠΎΠΉ ΠΊΠΈΡΠ»ΠΎΡΠΎΠΉ, ΡΠΎΠ»ΡΠ½ΠΎΠΉ ΠΊΠΈΡΠ»ΠΎΡΠΎΠΉ, ΡΠ΅ΠΏΠ»ΠΎΠΉ ΡΠ΅ΡΠ½ΠΎΠΉ ΠΊΠΈΡΠ»ΠΎΡΠΎΠΉ ΠΈ ΡΠΈΠ»ΡΠ½ΡΠΌΠΈ ΡΠ΅Π»ΠΎΡΠ½ΡΠΌΠΈ ΡΠ°ΡΡΠ²ΠΎΡΠ°ΠΌΠΈ. Π’Π°ΠΊΠΆΠ΅ ΠΈΠ·Π²Π΅ΡΡΠ½ΠΎ, ΡΡΠΎ ΠΎΠ½ΠΈ ΡΠ²Π»ΡΡΡΡΡ ΡΠ°ΠΌΠΎΡΠΌΠ°Π·ΡΠ²Π°ΡΡΠΈΠΌΠΈΡΡ ΠΈ ΡΠ»Π΅ΠΊΡΡΠΎΠΈΠ·ΠΎΠ»ΠΈΡΡΡΡΠΈΠΌΠΈ. Π¨Π°ΡΠΈΠΊΠΈ ΠΈΠ· ΠΎΠΊΡΠΈΠ΄Π° Π°Π»ΡΠΌΠΈΠ½ΠΈΡ Al2O3 ΠΈΠΌΠ΅ΡΡ ΡΠ²Π΅Ρ ΠΎΡ Π±Π΅Π»ΠΎΠ³ΠΎ Π΄ΠΎ ΡΠ²Π΅ΡΠ° ΡΠ»ΠΎΠ½ΠΎΠ²ΠΎΠΉ ΠΊΠΎΡΡΠΈ ΠΈ ΠΏΡΠΎΠΈΠ·Π²ΠΎΠ΄ΡΡΡΡ Π² ΡΠΎΠΎΡΠ²Π΅ΡΡΡΠ²ΠΈΠΈ ΡΠΎ ΡΡΠ°Π½Π΄Π°ΡΡΠΎΠΌ ASTM F 2094, ΠΊΠ»Π°ΡΡ II/III.
Π¨Π°ΡΠΈΠΊΠΈ , ΠΈΠ·Π³ΠΎΡΠΎΠ²Π»Π΅Π½Π½ΡΠ΅ ΠΈΠ· ΠΊΠ΅ΡΠ°ΠΌΠΈΡΠ΅ΡΠΊΠΎΠ³ΠΎ ΠΌΠ°ΡΠ΅ΡΠΈΠ°Π»Π° Π½ΠΈΡΡΠΈΠ΄Π° ΠΊΡΠ΅ΠΌΠ½ΠΈΡ , Π»Π΅Π³ΠΊΠΈΠ΅ , Π½ΠΎ ΠΎΠ±Π»Π°Π΄Π°ΡΡ Π±ΠΎΠ»ΡΡΠΎΠΉ ΠΏΡΠΎΡΠ½ΠΎΡΡΡΡ ΠΈ Π²ΡΠ΄Π°ΡΡΠ΅ΠΉΡΡ ΡΡΡΠΎΠΉΡΠΈΠ²ΠΎΡΡΡΡ ΠΊ ΠΊΠΎΡΡΠΎΠ·ΠΈΠΈ . Π’ΠΎΠ»ΡΠΊΠΎ Π½Π΅ΠΊΠΎΡΠΎΡΡΠ΅ ΠΊΠΈΡΠ»ΠΎΡΡ ΠΈ ΡΠ΅Π»ΠΎΡΠ½ΡΠ΅ ΡΠ°ΡΡΠ²ΠΎΡΡ Π²ΡΠ·ΡΠ²Π°ΡΡ ΠΊΠΎΡΡΠΎΠ·ΠΈΡ. ΠΠ°ΡΠ΅ΡΠΈΠ°Π» ΠΈΠΌΠ΅Π΅Ρ ΠΈΠ·ΠΎΠ»ΡΡΠΈΠΎΠ½Π½ΡΠΉ ΡΡΡΠ΅ΠΊΡ . Π¨Π°ΡΠΈΠΊΠΈ ΡΠ°ΠΊΠΆΠ΅ ΡΠ²Π»ΡΡΡΡΡ ΡΠ°ΠΌΠΎΡΠΌΠ°Π·ΡΠ²Π°ΡΡΠΈΠΌΠΈΡΡ ΠΈ ΠΎΠ±Π»Π°Π΄Π°ΡΡ Π±ΠΎΠ»ΡΡΠΎΠΉ ΡΡΡΠΎΠΉΡΠΈΠ²ΠΎΡΡΡΡ ΠΊ ΡΠ΅ΠΌΠΏΠ΅ΡΠ°ΡΡΡΠ½ΡΠΌ ΠΊΠΎΠ»Π΅Π±Π°Π½ΠΈΡΠΌ, ΡΡΠΎ Π·Π°ΠΌΠ΅ΡΠ½ΠΎ Π²Π»ΠΈΡΠ΅Ρ Π½Π° ΠΈΡΠΎΠ³ΠΎΠ²ΡΡ ΠΏΡΠΈΠ±ΡΠ»Ρ. ΠΠ½ΠΈ Π½Π°ΠΌΠ½ΠΎΠ³ΠΎ Π΄ΠΎΡΠΎΠΆΠ΅, ΡΠ΅ΠΌ ΡΠ°ΡΠΈΠΊΠΈ ΠΈΠ· ΠΎΠΊΡΠΈΠ΄Π° Π°Π»ΡΠΌΠΈΠ½ΠΈΡ. Π¨Π°ΡΠΈΠΊΠΎΠ² ΠΈΠ· Si3N4 9 ΡΡ.0011 ΡΠ΅ΡΠ½ΡΠΉ ΠΏΠ΅ΡΠ»Π°ΠΌΡΡΡΠΎΠ²ΡΠΉ ΡΠ²Π΅Ρ.
Π§ΡΠΎ Π΄Π΅Π»Π°Π΅Ρ ΡΠ°ΡΠΈΠΊΠΎΠ²ΡΠΉ ΠΏΠΎΠ΄ΡΠΈΠΏΠ½ΠΈΠΊ ΡΠ°ΠΊΠΈΠΌ ΠΎΡΠΎΠ±Π΅Π½Π½ΡΠΌ?
ΠΡ ΡΠΆΠ΅ ΠΏΡΠΎΠ³ΠΎΠ»ΠΎΡΠΎΠ²Π°Π»ΠΈ!
Π¨Π°ΡΠΈΠΊΠΈ ΠΏΠΎΠ΄ΡΠΈΠΏΠ½ΠΈΠΊΠΎΠ²: ΡΡΠΊΠΎΠ²ΠΎΠ΄ΡΡΠ²ΠΎ | ΠΠΏΡΠ΅Π΄Π΅Π»Π΅Π½ΠΈΠ΅, ΠΌΠ°ΡΠ΅ΡΠΈΠ°Π»Ρ ΠΈ ΠΏΡΠΈΠΌΠ΅Π½Π΅Π½ΠΈΠ΅
Π§ΡΠΎ ΡΠ°ΠΊΠΎΠ΅ ΡΠ°ΡΠΈΠΊΠΎΠΏΠΎΠ΄ΡΠΈΠΏΠ½ΠΈΠΊ?
Π¨Π°ΡΠΈΠΊΠΈ ΠΏΠΎΠ΄ΡΠΈΠΏΠ½ΠΈΠΊΠΎΠ² ΠΏΡΠ΅Π΄ΡΡΠ°Π²Π»ΡΡΡ ΡΠΎΠ±ΠΎΠΉ ΡΡΠ΅ΡΠΈΡΠ΅ΡΠΊΠΈΠ΅ ΠΊΠΎΠΌΠΏΠΎΠ½Π΅Π½ΡΡ, ΡΠ°ΡΡΠΎ ΠΈΡΠΏΠΎΠ»ΡΠ·ΡΠ΅ΠΌΡΠ΅ Π² ΠΊΠ°ΡΠ΅ΡΡΠ²Π΅ ΠΌΠ΅Ρ Π°Π½ΠΈΠ·ΠΌΠΎΠ² ΠΊΠ°ΡΠ΅Π½ΠΈΡ Π² ΡΡΡΡΠΎΠΉΡΡΠ²Π°Ρ Π²ΡΠ°ΡΠ°ΡΠ΅Π»ΡΠ½ΠΎΠ³ΠΎ Π΄Π²ΠΈΠΆΠ΅Π½ΠΈΡ, ΡΠ°ΠΊΠΈΡ ΠΊΠ°ΠΊ ΠΏΠΎΠ΄ΡΠΈΠΏΠ½ΠΈΠΊΠΈ, ΠΎΡΠ½Π°ΡΡΠΊΠ° ΠΈ ΠΊΠΎΠ»Π΅ΡΠ°. ΠΠ½ΡΡΡΠΈ ΡΡΠΈΡ ΡΡΡΡΠΎΠΉΡΡΠ² ΠΎΠ½ΠΈ ΡΠΌΠ΅Π½ΡΡΠ°ΡΡ ΡΡΠ΅Π½ΠΈΠ΅ ΠΏΡΠΈ Π²ΡΠ°ΡΠ΅Π½ΠΈΠΈ ΠΌΠ΅ΠΆΠ΄Ρ ΠΊΠΎΠΌΠΏΠΎΠ½Π΅Π½ΡΠ°ΠΌΠΈ ΠΈ Π²ΠΎΡΠΏΡΠΈΠ½ΠΈΠΌΠ°ΡΡ ΡΠ°Π΄ΠΈΠ°Π»ΡΠ½ΡΠ΅ ΠΈ/ΠΈΠ»ΠΈ ΠΎΡΠ΅Π²ΡΠ΅ Π½Π°Π³ΡΡΠ·ΠΊΠΈ. ΠΡΡΠ³ΠΈΠ΅ ΡΠ°ΡΠΏΡΠΎΡΡΡΠ°Π½Π΅Π½Π½ΡΠ΅ Π²Π°ΡΠΈΠ°Π½ΡΡ ΠΈΡΠΏΠΎΠ»ΡΠ·ΠΎΠ²Π°Π½ΠΈΡ Π²ΠΊΠ»ΡΡΠ°ΡΡ ΠΈΡΠΏΠΎΠ»ΡΠ·ΠΎΠ²Π°Π½ΠΈΠ΅ Π² ΠΊΠ°ΡΠ΅ΡΡΠ²Π΅ ΡΡΠ΅Π΄Ρ Π΄Π»Ρ ΡΠ»ΠΈΡΠΎΠ²ΠΊΠΈ ΠΈΠ»ΠΈ ΠΏΠΎΠ»ΠΈΡΠΎΠ²ΠΊΠΈ ΠΈΠ»ΠΈ ΠΊΠΎΠΌΠΏΠΎΠ½Π΅Π½ΡΠΎΠ² ΠΈΠ³ΡΡΡΠ΅ΠΊ. ΠΠ½ΠΈ Π΄ΠΎΡΡΡΠΏΠ½Ρ ΠΈΠ· Π½Π΅ΡΠΊΠΎΠ»ΡΠΊΠΈΡ ΡΠ°Π·Π»ΠΈΡΠ½ΡΡ ΠΌΠ°ΡΠ΅ΡΠΈΠ°Π»ΠΎΠ² Π² ΡΠΎΠΎΡΠ²Π΅ΡΡΡΠ²ΠΈΠΈ Ρ ΡΡΠ΅Π±ΠΎΠ²Π°Π½ΠΈΡΠΌΠΈ ΠΈ ΠΎΠ³ΡΠ°Π½ΠΈΡΠ΅Π½ΠΈΡΠΌΠΈ ΡΠ°Π·Π»ΠΈΡΠ½ΡΡ ΠΎΠ±Π»Π°ΡΡΠ΅ΠΉ ΠΏΡΠΈΠΌΠ΅Π½Π΅Π½ΠΈΡ.
Β
Β
ΠΠ°ΡΠ΅ΡΠΈΠ°Π»Ρ ΡΠ°ΡΠΈΠΊΠΎΠ² ΠΏΠΎΠ΄ΡΠΈΠΏΠ½ΠΈΠΊΠΎΠ²
Π‘ΠΏΠ΅ΡΠΈΠ°Π»ΠΈΡΡΡ ΠΎΡΡΠ°ΡΠ»ΠΈ ΠΈΡΠΏΠΎΠ»ΡΠ·ΡΡΡ ΡΠ°ΡΠΈΠΊΠΈ ΠΏΠΎΠ΄ΡΠΈΠΏΠ½ΠΈΠΊΠΎΠ², ΠΈΠ·Π³ΠΎΡΠΎΠ²Π»Π΅Π½Π½ΡΠ΅ ΠΈΠ· ΡΠ°Π·Π»ΠΈΡΠ½ΡΡ
ΠΌΠ°ΡΠ΅ΡΠΈΠ°Π»ΠΎΠ², Π²ΡΠ±ΠΎΡ ΠΊΠΎΡΠΎΡΡΡ
Π·Π°Π²ΠΈΡΠΈΡ ΠΎΡ ΠΏΡΠ΅Π΄ΠΏΠΎΠ»Π°Π³Π°Π΅ΠΌΠΎΠ³ΠΎ ΠΏΡΠΈΠΌΠ΅Π½Π΅Π½ΠΈΡ. ΠΠ΅ΠΊΠΎΡΠΎΡΡΠ΅ ΠΈΠ· Π½Π°ΠΈΠ±ΠΎΠ»Π΅Π΅ ΡΠ°ΡΠΏΡΠΎΡΡΡΠ°Π½Π΅Π½Π½ΡΡ
ΠΌΠ°ΡΠ΅ΡΠΈΠ°Π»ΠΎΠ² Π΄Π»Ρ ΡΠ°ΡΠΈΠΊΠΎΠ² ΠΏΠΎΠ΄ΡΠΈΠΏΠ½ΠΈΠΊΠΎΠ² Π²ΠΊΠ»ΡΡΠ°ΡΡ:
Β
- ΠΠ»ΡΠΌΠΈΠ½ΠΈΠΉ. ΠΠ»ΡΠΌΠΈΠ½ΠΈΠ΅Π²ΡΠ΅ ΡΠ°ΡΠΈΠΊΠΈ ΠΎΠ±Π»Π°Π΄Π°ΡΡ Ρ ΠΎΡΠΎΡΠ΅ΠΉ ΠΊΠΎΡΡΠΎΠ·ΠΈΠΎΠ½Π½ΠΎΠΉ ΡΡΠΎΠΉΠΊΠΎΡΡΡΡ ΠΈ ΠΈΠ·Π½ΠΎΡΠΎΡΡΠΎΠΉΠΊΠΎΡΡΡΡ, Π° ΡΠ°ΠΊΠΆΠ΅ ΠΈΠΌΠ΅ΡΡ Π³Π»Π°Π΄ΠΊΡΡ ΠΏΠΎΠ²Π΅ΡΡ Π½ΠΎΡΡΡ, ΡΡΠΎ Π΄Π΅Π»Π°Π΅Ρ ΠΈΡ ΠΏΠΎΠ΄Ρ ΠΎΠ΄ΡΡΠΈΠΌΠΈ Π΄Π»Ρ ΠΏΡΠΈΠ»ΠΎΠΆΠ΅Π½ΠΈΠΉ Ρ Π²ΡΡΠΎΠΊΠΈΠΌ ΠΊΠΎΡΡΡΠΈΡΠΈΠ΅Π½ΡΠΎΠΌ ΡΡΠ΅Π½ΠΈΡ. ΠΠ½ΠΈ ΡΠ°ΡΡΠΎ ΠΈΡΠΏΠΎΠ»ΡΠ·ΡΡΡΡΡ Π² ΠΏΠΎΠ΄ΡΠΈΠΏΠ½ΠΈΠΊΠ°Ρ ΠΈ ΠΊΠ»Π°ΠΏΠ°Π½Π°Ρ , Π°Π²ΡΠΎΠΌΠΎΠ±ΠΈΠ»ΡΠ½ΡΡ , ΡΠ»Π΅ΠΊΡΡΠΈΡΠ΅ΡΠΊΠΈΡ ΠΈ ΡΠ²Π°ΡΠΎΡΠ½ΡΡ ΡΡΡΡΠΎΠΉΡΡΠ²Π°Ρ Π±Π΅Π·ΠΎΠΏΠ°ΡΠ½ΠΎΡΡΠΈ, Π° ΡΠ°ΠΊΠΆΠ΅ Π² Π°ΡΡΠΎΠΊΠΎΡΠΌΠΈΡΠ΅ΡΠΊΠΎΠΌ ΠΈ Π°Π²ΠΈΠ°ΡΠΈΠΎΠ½Π½ΠΎΠΌ ΠΎΠ±ΠΎΡΡΠ΄ΠΎΠ²Π°Π½ΠΈΠΈ ΠΈ ΡΠΈΡΡΠ΅ΠΌΠ°Ρ .
Β
- ΠΠ°ΡΡΠ½Ρ/ΠΌΠ΅Π΄Ρ/Π±ΡΠΎΠ½Π·Π°. ΠΡΠΈ ΠΌΠ°ΡΠ΅ΡΠΈΠ°Π»Ρ ΡΠ²Π»ΡΡΡΡΡ Π½Π΅ΠΌΠ°Π³Π½ΠΈΡΠ½ΡΠΌΠΈ ΠΈ ΡΠ»Π΅ΠΊΡΡΠΎΠΏΡΠΎΠ²ΠΎΠ΄Π½ΡΠΌΠΈ. ΠΠΎΡΠ»Π΅Π΄Π½Π΅Π΅ Π΄Π΅Π»Π°Π΅Ρ ΡΠ°ΡΠΈΠΊΠΈ, ΠΈΠ·Π³ΠΎΡΠΎΠ²Π»Π΅Π½Π½ΡΠ΅ ΠΈΠ· Π½ΠΈΡ , ΠΏΠΎΠ΄Ρ ΠΎΠ΄ΡΡΠΈΠΌΠΈ Π΄Π»Ρ ΠΈΡΠΏΠΎΠ»ΡΠ·ΠΎΠ²Π°Π½ΠΈΡ Π² ΡΠ»Π΅ΠΊΡΡΠΈΡΠ΅ΡΠΊΠΈΡ ΠΈ ΡΠ»Π΅ΠΊΡΡΠΎΠ½Π½ΡΡ ΡΡΡΡΠΎΠΉΡΡΠ²Π°Ρ . ΠΠ½ΠΈ ΡΠ°ΠΊΠΆΠ΅ ΠΈΡΠΏΠΎΠ»ΡΠ·ΡΡΡΡΡ Π² ΡΠ°Π·Π»ΠΈΡΠ½ΡΡ ΠΏΡΠΈΠ»ΠΎΠΆΠ΅Π½ΠΈΡΡ ΡΠ»Π΅ΡΠ°ΡΠ½ΠΎΠ³ΠΎ Π΄Π΅Π»Π° ΠΈ ΠΊΠ»Π°ΠΏΠ°Π½Π°.
Β
- ΠΠ΅ΡΠ°ΠΌΠΈΠΊΠ°. ΠΠ΅ΡΠ°ΠΌΠΈΡΠ΅ΡΠΊΠΈΠΉ ΠΏΠΎΠ΄ΡΠΈΠΏΠ½ΠΈΠΊΠΎΠ²ΡΠΉ ΠΌΠ°ΡΠ΅ΡΠΈΠ°Π» ΠΏΡΠ΅Π΄ΡΡΠ°Π²Π»Π΅Π½ Π²ΠΎ ΠΌΠ½ΠΎΠ³ΠΈΡ
Π²Π°ΡΠΈΠ°Π½ΡΠ°Ρ
: ΠΎΡ ΡΡΠ±ΠΈΠ½ΠΎΠ²ΠΎΠ³ΠΎ ΡΠ°ΡΠΈΠΊΠ° Π΄ΠΎ ΠΌΠ°ΡΠ΅ΡΠΈΠ°Π»Π° ΡΠ°ΡΠΈΠΊΠ° ΠΈΠ· ΠΎΠΊΡΠΈΠ΄Π° Π°Π»ΡΠΌΠΈΠ½ΠΈΡ.
ΠΠ½ ΠΎΠ±Π»Π°Π΄Π°Π΅Ρ Π²ΡΡΠΎΠΊΠΎΠΉ ΡΡΡΠΎΠΉΡΠΈΠ²ΠΎΡΡΡΡ ΠΊ ΠΊΠΎΡΡΠΎΠ·ΠΈΠΈ ΠΈ ΡΠ΅ΡΠΌΠΈΡΠ΅ΡΠΊΠΈΠΌ ΠΏΠΎΠ²ΡΠ΅ΠΆΠ΄Π΅Π½ΠΈΡΠΌ, Π° ΡΠ°ΠΊΠΆΠ΅ ΠΏΡΠΈΡΠΏΠΎΡΠ°Π±Π»ΠΈΠ²Π°Π΅ΡΡΡ ΠΊ ΠΌΠΈΠ½ΠΈΠΌΠ°Π»ΡΠ½ΠΎΠΉ ΡΠΌΠ°Π·ΠΊΠ΅ ΠΈ ΡΠ°Π±ΠΎΡΠ΅ Π² ΠΊΠΈΡΠ»ΠΎΡΠ½ΡΡ /ΡΠ΅Π»ΠΎΡΠ½ΡΡ ΡΡΠ΅Π΄Π°Ρ .
Β
- Π‘ΡΠ΅ΠΊΠ»ΠΎ. Π¨Π°ΡΠΈΠΊΠΈ ΠΏΠΎΠ΄ΡΠΈΠΏΠ½ΠΈΠΊΠΎΠ² ΠΈΠ· ΡΡΠ΅ΠΊΠ»Π° Π΄Π΅ΠΌΠΎΠ½ΡΡΡΠΈΡΡΡΡ ΠΏΡΠ΅Π²ΠΎΡΡ ΠΎΠ΄Π½ΡΡ ΠΊΠΎΡΡΠΎΠ·ΠΈΠΎΠ½Π½ΡΡ ΡΡΠΎΠΉΠΊΠΎΡΡΡ, Ρ ΠΎΡΠΎΡΠΈΠ΅ ΠΌΠ΅Ρ Π°Π½ΠΈΡΠ΅ΡΠΊΠΈΠ΅ ΡΠ²ΠΎΠΉΡΡΠ²Π° ΠΈ ΡΠ»Π΅ΠΊΡΡΠΎΠΈΠ·ΠΎΠ»ΡΡΠΈΠΎΠ½Π½ΡΠ΅ ΡΠ²ΠΎΠΉΡΡΠ²Π°. ΠΠΎΡΠΊΠΎΠ»ΡΠΊΡ ΠΎΠ½ΠΈ Π΄ΠΎΡΡΡΠΏΠ½Ρ Ρ ΡΠ°Π·Π»ΠΈΡΠ½ΠΎΠΉ ΡΡΠ΅ΠΏΠ΅Π½ΡΡ ΠΏΡΠΎΠ·ΡΠ°ΡΠ½ΠΎΡΡΠΈ, ΠΎΠ½ΠΈ ΠΏΠΎΠ΄Ρ ΠΎΠ΄ΡΡ Π΄Π»Ρ ΠΈΡΠΏΠΎΠ»ΡΠ·ΠΎΠ²Π°Π½ΠΈΡ Π² ΠΎΠΏΡΠΈΡΠ΅ΡΠΊΠΈΡ ΠΏΡΠΈΠ»ΠΎΠΆΠ΅Π½ΠΈΡΡ .
Β
- ΠΠ»Π°ΡΡΠΈΠΊ. ΠΠ»Π°ΡΡΠΈΠΊΠΎΠ²ΡΠ΅ ΡΠ°ΡΠΈΠΊΠΈ ΠΏΠΎΠ΄ΡΠΈΠΏΠ½ΠΈΠΊΠΎΠ² ΠΈΠΌΠ΅ΡΡ Π½ΠΈΠ·ΠΊΡΡ ΠΏΠ»ΠΎΡΠ½ΠΎΡΡΡ ΠΌΠ°ΡΠ΅ΡΠΈΠ°Π»Π° ΠΈ Π²ΡΡΠΎΠΊΡΡ ΠΊΠΎΡΡΠΎΠ·ΠΈΠΎΠ½Π½ΡΡ ΡΡΠΎΠΉΠΊΠΎΡΡΡ. Π Π·Π°Π²ΠΈΡΠΈΠΌΠΎΡΡΠΈ ΠΎΡ ΠΏΡΠΈΠΌΠ΅Π½Π΅Π½ΠΈΡ ΠΎΠ½ΠΈ ΠΌΠΎΠ³ΡΡ Π±ΡΡΡ ΠΈΠ·Π³ΠΎΡΠΎΠ²Π»Π΅Π½Ρ ΠΈΠ· ΡΠ°Π·Π»ΠΈΡΠ½ΡΡ ΡΠΎΡΡΠ°Π²ΠΎΠ² Ρ ΡΠ»ΡΡΡΠ΅Π½Π½ΡΠΌΠΈ ΡΠΊΡΠΏΠ»ΡΠ°ΡΠ°ΡΠΈΠΎΠ½Π½ΡΠΌΠΈ ΡΠ²ΠΎΠΉΡΡΠ²Π°ΠΌΠΈ, ΡΠ°ΠΊΠΈΠΌΠΈ ΠΊΠ°ΠΊ ΡΡΠΎΠΉΠΊΠΎΡΡΡ ΠΊ ΠΈΡΡΠΈΡΠ°Π½ΠΈΡ ΠΈΠ»ΠΈ ΡΠ΅ΡΠΌΠΎΡΡΠΎΠΉΠΊΠΎΡΡΡ.
Β
- ΠΠ΅ΡΠΆΠ°Π²Π΅ΡΡΠ°Ρ ΡΡΠ°Π»Ρ. Π ΠΏΡΠΎΠΈΠ·Π²ΠΎΠ΄ΡΡΠ²Π΅ ΡΠ°ΡΠΈΠΊΠΎΠ² ΠΏΠΎΠ΄ΡΠΈΠΏΠ½ΠΈΠΊΠΎΠ² ΠΈΡΠΏΠΎΠ»ΡΠ·ΡΡΡΡΡ ΠΊΠ°ΠΊ Π·Π°ΠΊΠ°Π»Π΅Π½Π½Π°Ρ, ΡΠ°ΠΊ ΠΈ Π½Π΅Π·Π°ΠΊΠ°Π»Π΅Π½Π½Π°Ρ Π½Π΅ΡΠΆΠ°Π²Π΅ΡΡΠ°Ρ ΡΡΠ°Π»Ρ. ΠΠ°ΠΊΠ°Π»Π΅Π½Π½ΡΠ΅ Π²Π°ΡΠΈΠ°Π½ΡΡ ΠΎΠ±Π΅ΡΠΏΠ΅ΡΠΈΠ²Π°ΡΡ Π±ΠΎΠ»ΡΡΡΡ ΠΏΡΠΎΡΠ½ΠΎΡΡΡ ΠΈ ΠΈΠ·Π½ΠΎΡΠΎΡΡΠΎΠΉΠΊΠΎΡΡΡ, ΡΡΠΎ Π΄Π΅Π»Π°Π΅Ρ ΠΈΡ
ΠΏΡΠΈΠ³ΠΎΠ΄Π½ΡΠΌΠΈ Π΄Π»Ρ ΠΈΡΠΏΠΎΠ»ΡΠ·ΠΎΠ²Π°Π½ΠΈΡ Π² ΠΏΡΠΎΠΌΡΡΠ»Π΅Π½Π½ΡΡ
ΠΏΠΎΠ΄ΡΠΈΠΏΠ½ΠΈΠΊΠ°Ρ
.
ΠΠ΅Π·Π°ΠΊΠ°Π»Π΅Π½Π½Π°Ρ Π½Π΅ΡΠΆΠ°Π²Π΅ΡΡΠ°Ρ ΡΡΠ°Π»Ρ Π±ΠΎΠ»Π΅Π΅ ΡΠ΄ΠΎΠ±Π½Π° Π² ΠΎΠ±ΡΠ°Π±ΠΎΡΠΊΠ΅, Π½ΠΎ ΠΈΠΌΠ΅Π΅Ρ ΠΌΠ΅Π½ΡΡΡΡ ΠΊΠΎΡΡΠΎΠ·ΠΈΠΎΠ½Π½ΡΡ ΡΡΠΎΠΉΠΊΠΎΡΡΡ. Π¨Π°ΡΠΈΠΊΠΈ, ΡΠ΄Π΅Π»Π°Π½Π½ΡΠ΅ ΠΈΠ· Π½Π΅Π³ΠΎ, ΠΎΠ±ΡΡΠ½ΠΎ ΠΈΡΠΏΠΎΠ»ΡΠ·ΡΡΡΡΡ Π² ΡΠ»Π΅ΠΊΡΡΠΎΠ½Π½ΡΡ ΡΡΡΡΠΎΠΉΡΡΠ²Π°Ρ .
- Π‘ΡΠ°Π»Ρ ΠΈ Π΄ΡΡΠ³ΠΈΠ΅ ΡΡΠ°Π»ΡΠ½ΡΠ΅ ΡΠΏΠ»Π°Π²Ρ. Π¨Π°ΡΠΈΠΊΠΈ ΠΏΠΎΠ΄ΡΠΈΠΏΠ½ΠΈΠΊΠΎΠ² ΠΌΠΎΠ³ΡΡ Π±ΡΡΡ ΠΈΠ·Π³ΠΎΡΠΎΠ²Π»Π΅Π½Ρ ΠΈΠ· ΡΠ°Π·Π»ΠΈΡΠ½ΡΡ ΡΡΠ°Π»ΡΠ½ΡΡ ΡΠΏΠ»Π°Π²ΠΎΠ², ΡΠ°ΠΊΠΈΡ ΠΊΠ°ΠΊ ΠΏΠΎΠ΄ΡΠΈΠΏΠ½ΠΈΠΊΠΎΠ²Π°Ρ ΡΡΠ°Π»Ρ, ΡΠ³Π»Π΅ΡΠΎΠ΄ΠΈΡΡΠ°Ρ ΡΡΠ°Π»Ρ ΠΈ ΠΈΠ½ΡΡΡΡΠΌΠ΅Π½ΡΠ°Π»ΡΠ½Π°Ρ ΡΡΠ°Π»Ρ. ΠΠΊΡΠΏΠ»ΡΠ°ΡΠ°ΡΠΈΠΎΠ½Π½ΡΠ΅ Ρ Π°ΡΠ°ΠΊΡΠ΅ΡΠΈΡΡΠΈΠΊΠΈ, ΠΊΠΎΡΠΎΡΡΠ΅ ΠΎΠ½ΠΈ Π΄Π΅ΠΌΠΎΠ½ΡΡΡΠΈΡΡΡΡ, Π²Π°ΡΡΠΈΡΡΡΡΡΡ Π² Π·Π°Π²ΠΈΡΠΈΠΌΠΎΡΡΠΈ ΠΎΡ Π²ΡΠ±ΡΠ°Π½Π½ΠΎΠ³ΠΎ ΡΡΡΠΎΠΈΡΠ΅Π»ΡΠ½ΠΎΠ³ΠΎ ΠΌΠ°ΡΠ΅ΡΠΈΠ°Π»Π°.
Β
ΠΡΠΈΠΌΠ΅Π½Π΅Π½ΠΈΠ΅ ΡΠ°ΡΠΈΠΊΠΎΠ² ΠΏΠΎΠ΄ΡΠΈΠΏΠ½ΠΈΠΊΠΎΠ²
Π¨Π°ΡΠΈΠΊΠΈ ΠΏΠΎΠ΄ΡΠΈΠΏΠ½ΠΈΠΊΠΎΠ² ΡΠ΅Π³ΡΠ»ΡΡΠ½ΠΎ ΠΈΡΠΏΠΎΠ»ΡΠ·ΡΡΡΡΡ Π² ΡΠ°ΠΌΡΡ ΡΠ°Π·Π½ΡΡ ΠΎΠ±Π»Π°ΡΡΡΡ Π² ΠΊΠ°ΡΠ΅ΡΡΠ²Π΅ ΠΊΠΎΠΌΠΏΠΎΠ½Π΅Π½ΡΠ°, ΡΠ°Π·Π΄Π΅Π»ΡΡΡΠ΅Π³ΠΎ ΠΈ ΡΠΌΠ΅Π½ΡΡΠ°ΡΡΠ΅Π³ΠΎ ΡΡΠ΅Π½ΠΈΠ΅ ΠΌΠ΅ΠΆΠ΄Ρ Π΄Π²ΠΈΠΆΡΡΠΈΠΌΠΈΡΡ ΡΠ°ΡΡΡΠΌΠΈ. ΠΠ½ΠΈ ΠΈΡΠΏΠΎΠ»ΡΠ·ΡΡΡΡΡ Π² Π΄Π΅ΡΠ°Π»ΡΡ ΠΈ ΠΏΡΠΎΠ΄ΡΠΊΡΠ°Ρ , Π½Π°ΡΠΈΠ½Π°Ρ ΠΎΡ ΠΏΡΠΎΠΌΡΡΠ»Π΅Π½Π½ΡΡ ΡΡΡΡΠΎΠΉΡΡΠ² ΠΈ ΠΎΠ±ΠΎΡΡΠ΄ΠΎΠ²Π°Π½ΠΈΡ ΠΈ Π·Π°ΠΊΠ°Π½ΡΠΈΠ²Π°Ρ ΠΈΠ³ΡΠ°ΠΌΠΈ ΠΈ ΠΈΠ³ΡΡΡΠΊΠ°ΠΌΠΈ. ΠΡΡΠ³ΠΈΠ΅ ΠΏΡΠΈΠΌΠ΅Π½Π΅Π½ΠΈΡ Π²ΠΊΠ»ΡΡΠ°ΡΡ:
- ΠΠΎΠΌΠΏΠΎΠ½Π΅Π½ΡΡ ΠΎΠΏΡΠΈΡΠ΅ΡΠΊΠΎΠ³ΠΎ ΠΎΠ±ΠΎΡΡΠ΄ΠΎΠ²Π°Π½ΠΈΡ ΠΈ ΡΠΈΡΡΠ΅ΠΌ
- ΠΠ»Π΅ΠΌΠ΅Π½ΡΡ ΠΈΡΠΊΡΡΡΡΠ²Π° ΠΈ Π΄Π΅ΠΊΠΎΡΠ°ΡΠΈΠ²Π½ΡΠ΅ ΠΈΠ·Π΄Π΅Π»ΠΈΡ
- ΠΡΡΠΏΠ½ΠΎΠΌΠ°ΡΡΡΠ°Π±Π½Π°Ρ ΠΎΠ±Π»ΠΈΡΠΎΠ²ΠΊΠ° Π·Π΄Π°Π½ΠΈΠΉ
- Π‘ΡΠ΅Π΄Ρ Π΄Π»Ρ ΠΎΡΠ΄Π΅Π»ΠΊΠΈ ΠΏΠΎΠ²Π΅ΡΡ Π½ΠΎΡΡΠ΅ΠΉ, Π½Π°ΠΏΡΠΈΠΌΠ΅Ρ, ΠΏΠ΅ΡΠΊΠΎΡΡΡΡΠΉΠ½Π°Ρ ΠΎΠ±ΡΠ°Π±ΠΎΡΠΊΠ°, ΠΏΠΎΠ»ΠΈΡΠΎΠ²ΠΊΠ°, ΡΠ»ΠΈΡΠΎΠ²ΠΊΠ°, Π½Π°ΠΊΠ»Π΅ΠΏ, ΠΏΠΎΠ»ΠΈΡΠΎΠ²ΠΊΠ° ΠΈ ΡΠ΄Π°Π»Π΅Π½ΠΈΠ΅ Π²ΠΌΡΡΠΈΠ½
Β
Π¨Π°ΡΠΈΠΊΠΈ ΠΏΠΎΠ΄ΡΠΈΠΏΠ½ΠΈΠΊΠΎΠ² ΠΎΡ STR Industries
ΠΠ»Ρ Π»ΡΠ±ΠΎΠ³ΠΎ ΠΊΠ»ΠΈΠ΅Π½ΡΠ°, ΠΊΠΎΡΠΎΡΡΠΉ ΠΈΡΠΏΠΎΠ»ΡΠ·ΡΠ΅Ρ ΡΠ°ΡΠΈΠΊΠΈ ΠΏΠΎΠ΄ΡΠΈΠΏΠ½ΠΈΠΊΠΎΠ², Π²ΡΠ±ΠΎΡ ΠΌΠ΅ΡΡΠ° ΠΏΡΠΈΠΎΠ±ΡΠ΅ΡΠ΅Π½ΠΈΡ ΡΠ°ΡΠΈΠΊΠΎΠ² ΠΏΠΎΠ΄ΡΠΈΠΏΠ½ΠΈΠΊΠΎΠ² ΠΈΠΌΠ΅Π΅Ρ ΡΠ΅ΡΠ°ΡΡΠ΅Π΅ Π·Π½Π°ΡΠ΅Π½ΠΈΠ΅. ΠΠ°ΡΡΠ½Π΅ΡΡΡΠ²ΠΎ Ρ ΠΎΠΏΡΡΠ½ΡΠΌ ΠΏΠΎΡΡΠ°Π²ΡΠΈΠΊΠΎΠΌ Π³Π°ΡΠ°Π½ΡΠΈΡΡΠ΅Ρ, ΡΡΠΎ ΠΎΠ½ΠΈ ΠΏΠΎΠ»ΡΡΠ°Ρ ΠΊΠ°ΡΠ΅ΡΡΠ²Π΅Π½Π½ΡΠ΅ ΠΊΠΎΠΌΠΏΠΎΠ½Π΅Π½ΡΡ, ΠΎΡΠ²Π΅ΡΠ°ΡΡΠΈΠ΅ ΠΈΡ ΠΏΠΎΡΡΠ΅Π±Π½ΠΎΡΡΡΠΌ.
Π STR Industries ΠΌΡ ΠΈΠΌΠ΅Π΅ΠΌ Π±ΠΎΠ»Π΅Π΅ ΡΠ΅ΠΌ ΠΏΡΡΠΈΠ΄Π΅ΡΡΡΠΈΠ»Π΅ΡΠ½ΠΈΠΉ ΠΎΠΏΡΡ ΠΏΡΠΎΠΈΠ·Π²ΠΎΠ΄ΡΡΠ²Π° ΡΡΠ°Π»ΡΠ½ΡΡ ΡΠ°ΡΠΈΠΊΠΎΠ², ΡΡΠΎ Π΄Π°Π΅Ρ Π½Π°ΠΌ Π·Π½Π°Π½ΠΈΡ, Π½Π΅ΠΎΠ±Ρ ΠΎΠ΄ΠΈΠΌΡΠ΅ Π΄Π»Ρ ΠΏΡΠΎΠΈΠ·Π²ΠΎΠ΄ΡΡΠ²Π° Π²ΡΡΠΎΠΊΠΎΡΠΎΡΠ½ΡΡ ΡΠ°ΡΠΈΠΊΠΎΠ² Π΄Π»Ρ ΠΏΠΎΠ΄ΡΠΈΠΏΠ½ΠΈΠΊΠΎΠ², ΠΏΠΎΠ΄Ρ ΠΎΠ΄ΡΡΠΈΡ Π΄Π»Ρ ΠΈΡΠΏΠΎΠ»ΡΠ·ΠΎΠ²Π°Π½ΠΈΡ Π² ΡΠΈΡΠΎΠΊΠΎΠΌ Π΄ΠΈΠ°ΠΏΠ°Π·ΠΎΠ½Π΅ ΠΏΡΠΈΠΌΠ΅Π½Π΅Π½ΠΈΠΉ. ΠΠ°ΡΠ° ΠΏΡΠΎΠ΄ΡΠΊΡΠΈΡ Π΄ΠΎΡΡΡΠΏΠ½Π° Π²ΠΎ ΠΌΠ½ΠΎΠ³ΠΈΡ ΡΠ°Π·Π»ΠΈΡΠ½ΡΡ ΡΠΎΡΡΠ°Ρ , ΡΠ°Π·ΠΌΠ΅ΡΠ°Ρ ΠΈ ΠΌΠ°ΡΠ΅ΡΠΈΠ°Π»Π°Ρ Π΄Π»Ρ ΡΠ΄ΠΎΠ²Π»Π΅ΡΠ²ΠΎΡΠ΅Π½ΠΈΡ ΡΠ°Π·Π»ΠΈΡΠ½ΡΡ ΠΏΠΎΡΡΠ΅Π±Π½ΠΎΡΡΠ΅ΠΉ ΠΊΠ»ΠΈΠ΅Π½ΡΠΎΠ²:
Β
- ΠΠ°ΡΠΊΠΈ (ΡΠΎΠ³Π»Π°ΡΠ½ΠΎ AMBA): 3, 5, 10, 16, 24, 48, 100, 200 , 1000 β
- Π Π°Π·ΠΌΠ΅ΡΡ: Π²Π°ΡΡΠΈΡΡΠ΅ΡΡΡ Π² Π·Π°Π²ΠΈΡΠΈΠΌΠΎΡΡΠΈ ΠΎΡ ΠΌΠ°ΡΠΊΠΈ (ΡΠ°Π±Π»ΠΈΡΡ ΡΠ°Π·ΠΌΠ΅ΡΠΎΠ² ΡΠΌ.
Π½Π° ΡΡΡΠ°Π½ΠΈΡΠ΅ ΡΡΠ°Π»ΡΠ½ΡΡ ΡΠ°ΡΠΈΠΊΠΎΠ²)
- ΠΠ°ΡΠ΅ΡΠΈΠ°Π»Ρ: Π°Π»ΡΠΌΠΈΠ½ΠΈΠΉ , ΠΏΠΎΠ΄ΡΠΈΠΏΠ½ΠΈΠΊΠΎΠ²Π°Ρ ΡΡΠ°Π»Ρ, Π»Π°ΡΡΠ½Ρ, Π±ΡΠΎΠ½Π·Π°, ΡΠ³Π»Π΅ΡΠΎΠ΄ΠΈΡΡΠ°Ρ ΡΡΠ°Π»Ρ, ΠΊΠ΅ΡΠ°ΠΌΠΈΠΊΠ°, ΠΌΠ΅Π΄Ρ, ΡΡΠ΅ΠΊΠ»ΠΎ, ΠΏΠ»Π°ΡΡΠΈΠΊ, Π½Π΅ΡΠΆΠ°Π²Π΅ΡΡΠ°Ρ ΡΡΠ°Π»Ρ, ΠΈΠ½ΡΡΡΡΠΌΠ΅Π½ΡΠ°Π»ΡΠ½Π°Ρ ΡΡΠ°Π»Ρ
Β
ΠΠΎΡΡΡΠΏΠ½ΡΠ΅ ΠΌΠ°ΡΠΊΠΈ ΠΈ ΡΠ°Π·ΠΌΠ΅ΡΡ:
ΠΠ°ΡΠΊΠ° | ΠΠΈΠ°ΠΏΠ°Π·ΠΎΠ½ ΡΠ°Π·ΠΌΠ΅ΡΠΎΠ² (Π΄ΡΠΉΠΌΡ) |
---|---|
3 | 025″ — 3/16″ |
5 | 0,025″ — 1 1/2″ |
10 | 1/32″ — 2 1/2″ |
16 | 1/32″ — 2 1/2″ |
24 | 1/32″ — 2 1/2″ |
48 | 1/32″ — 2 1/2″ |
100 | 1/32″ — 4 1/2″ |
200 | 1/32″ — 4 1/2″ |
1000 | 1/32″ — 4 1/2″ |
Β
ΠΠ°ΡΠ° ΡΠ΅ΡΡΠΈΡΠΈΠΊΠ°ΡΠΈΡ TS 16949 Π΄Π΅ΠΌΠΎΠ½ΡΡΡΠΈΡΡΠ΅Ρ Π½Π°ΡΡ ΠΏΡΠΈΠ²Π΅ΡΠΆΠ΅Π½Π½ΠΎΡΡΡ ΡΠΏΡΠ°Π²Π»Π΅Π½ΠΈΡ ΠΊΠ°ΡΠ΅ΡΡΠ²ΠΎΠΌ ΠΈ ΠΏΠΎΡΡΠΎΡΠ½Π½ΠΎΠΌΡ ΡΠΎΠ²Π΅ΡΡΠ΅Π½ΡΡΠ²ΠΎΠ²Π°Π½ΠΈΡ, ΡΠ΄Π΅Π»ΡΡ ΠΎΡΠΎΠ±ΠΎΠ΅ Π²Π½ΠΈΠΌΠ°Π½ΠΈΠ΅ ΠΏΡΠ΅Π΄ΠΎΡΠ²ΡΠ°ΡΠ΅Π½ΠΈΡ Π΄Π΅ΡΠ΅ΠΊΡΠΎΠ² ΠΏΡΠΈ ΠΏΡΠΎΠ΅ΠΊΡΠΈΡΠΎΠ²Π°Π½ΠΈΠΈ, ΡΠ°Π·ΡΠ°Π±ΠΎΡΠΊΠ΅ ΠΈ ΠΏΡΠΎΠΈΠ·Π²ΠΎΠ΄ΡΡΠ²Π΅ Ρ Π΄ΠΎΠΏΠΎΠ»Π½ΠΈΡΠ΅Π»ΡΠ½ΡΠΌ ΠΎΠ±ΡΠ·Π°ΡΠ΅Π»ΡΡΡΠ²ΠΎΠΌ ΠΏΠΎ ΡΠΎΠΊΡΠ°ΡΠ΅Π½ΠΈΡ ΠΎΡΡ
ΠΎΠ΄ΠΎΠ² Π²ΠΎ Π²ΡΠ΅Ρ
Π°ΡΠΏΠ΅ΠΊΡΠ°Ρ
ΠΏΡΠΎΠΈΠ·Π²ΠΎΠ΄ΡΡΠ²Π°.