Как сделать шар из дерева своими руками без станка: Как выточить шар из дерева своими руками? | Своими руками
Как выточить шар из дерева своими руками? | Своими руками
© Автор: А.Громов
Ходит такая легенда, что когда-то в Советском Союзе мастерство токаря по дереву проверяли оригинальным тестом, в ходе которого тому поручали выточить идеальный шар на глаз, пользуясь одним только мейселем. Возможно, это всего лишь миф, но факт остается фактом: справиться с данным заданием способен только очень опытный мастер.
Стоит отметить, что такие изделия, как шары из дерева, до сих пор очень востребованы. Их используют, к примеру, как элементы мебели или предметов интерьера, для изготовления различных сувениров и поделок.
И для тех токарей, кто по тем или иным причинам отдает предпочтение другим способам выточки шаров, нежели точение на глаз, придумано много разных приспособлений: шаблоны, кондукторы, копировальные устройства. В число наиболее популярных из них входят так называемые шароточки, которые можно приобрести в магазине или изготовить самостоятельно.
Ссылка по теме: Чаша-клубочница из дерева своими руками
Работать с данным устройством крайне просто. Его основание крепится в паз на станине станка, а резец с резцедержателем выставляется по высоте центров. Также необходимо определить центр будущего шара на заготовке и выставить основание ровно под этим центром. Минимальный диаметр шара составляет 20 мм, а максимальный зависит от высоты центров на станке.
Заготовку следует зажать в центрах, либо закрепить в патроне, либо на планшайбе без поддержания задней бабки. Желательно предварительно сделать черновую обработку резцами — выточить цилиндр, определить центр и скруглить края.
После этого можно приступить к точению, двигая резцедержатель по окружности и подвигая резец после каждого прохода на небольшое расстояние, равное примерно 1 мм. Скорость вращения шпинделя необходимо выбирать, исходя из массы заготовки.
Подачу резцедержателя сделать небольшой, чтобы избежать затягивания резца в дерево из-за вибрации.
Для бережного зажима шара вместо центров устанавливаются самодельные приспособления. Благодаря этому можно проточить «хвосты», оставшиеся от первоначальной заготовки. В этих же зажимах можно и отшлифовать шар. (Фото 2.)
Конечно, даже начинающий токарь по дереву знает, что изготовить шар любого диаметра из дерева можно и без всяких дополнительных устройств. Для этого следует только сделать шаблон из фанеры в виде половинки окружности. И запастись временем и терпением… Но бывают ситуации, когда необходимо за короткий срок изготовить большую партию шаров идеальногоразмера. И в этом случае шароточка практически незаменима.
Если вы серьезно занимаетесь токарными работами по дереву, то перед вами рано или поздно встанет задача сделать шар, сферу или полусферу. И тогда такое приспособление, как шароточка, сможет существенно облегчить её решение.
Читайте также: Шариковая ручка из дерева своими руками – как выточить на токарном станке
КАК ВЫТОЧИТЬ ШАР НА ТОКАРНОМ СТАНКЕ – ВИДЕО
3 способа выточить шар из дерева на токарном станке. 3 ways of turning balls in wood on a lathe
Watch this video on YouTube
САМОДЕЛЬНАЯ ШАРОТОЧКА И ВЫТАЧИВАНИЕ ШАРА
Самодельная шароточка. Вытачивание шара и ниппеля на токарном станке ТВ7.
Watch this video on YouTube
ШАРОТОЧКА СВОИМИ РУКАМИ – ВИДЕО
ИНСТРУМЕНТ ДЛЯ МАСТЕРОВ И МАСТЕРИЦ, И ТОВАРЫ ДЛЯ ДОМА ОЧЕНЬ ДЕШЕВО. БЕСПЛАТНАЯ ДОСТАВКА. ЕСТЬ ОТЗЫВЫ.Ниже другие записи по теме «Как сделать своими руками — домохозяину!»
Подпишитесь на обновления в наших группах и поделитесь.
Будем друзьями!
Токарные шары ~ Резьба по дереву
Токарные шары из дерева |

Вспомнив свои давнишние опыты с деревянными шарами, захотел повторить их, но уже на более совершенном станке и при помощи специального приспособления.В интернете можно найти информацию о различных приспособлениях для точения шаров.Чаще всего это металлическое поворотное устройство, в которое вставляется токарная стамеска, а дальше уж дело техники.
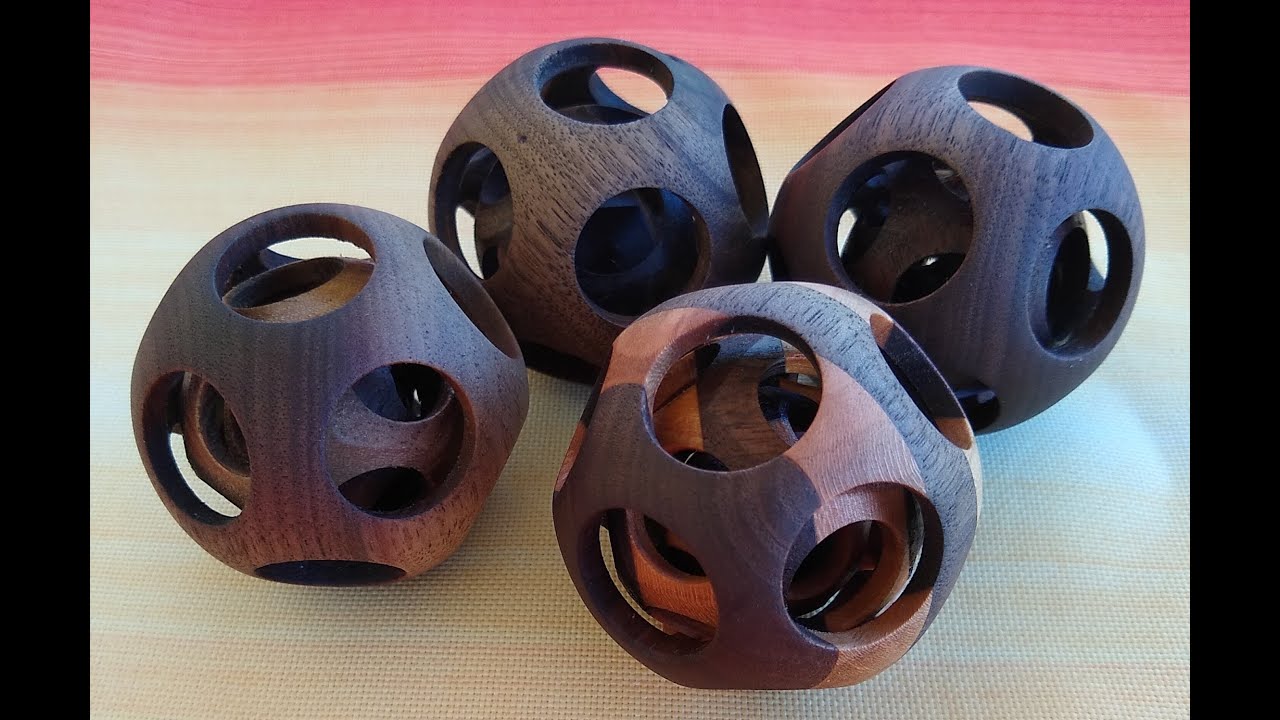
А вот так выглядят мои токарные шары из различных пород древесины.
Токарные шары из дерева своими руками.Красные шары выточены из боярышника, Полосатый шар на заднем плане — из туи, рядом шар из дуба, слева шар из рябины и справа три шара из березового сувеля. |
Самодельное приспособление для точения деревянных шаров.Состоит из двух чашеобразных зажимов в которые и вставляется заготовка.![]() |
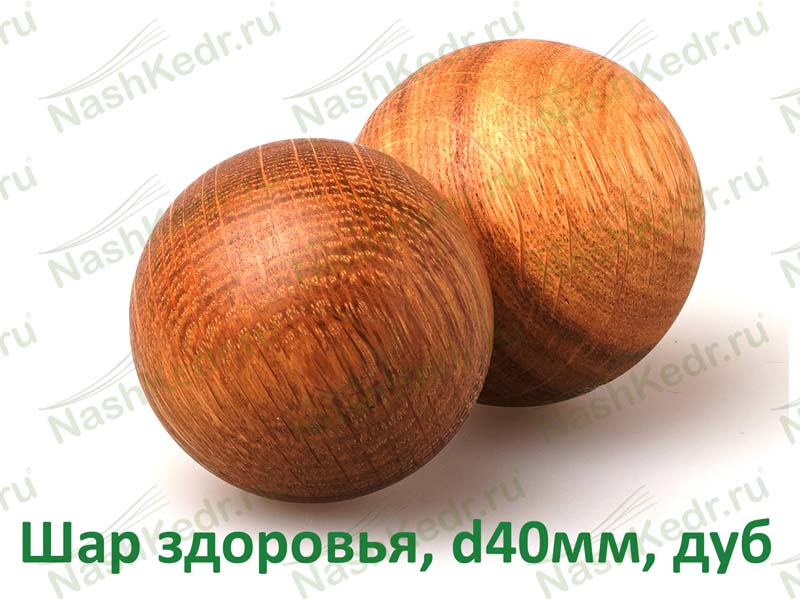
Передние и задние зажимы для точения деревянных шаров |

Сам шар точится так.Берем подходящую заготовку, зажимаем ее в центрах и оцилиндровываем.Точим шар на глаз.Устанавливаем в ПБ передний зажим и на задний центр устанавливаем задний зажим.Устанавливаем в них грубо выточенный шар (см.фото 1).Протачиваем поверхность шара.Вынимаем шар из зажимов и переворачиваем его на 90 градусов.Важно!Нужно стараться шар установить как можно точнее по центру, чтобы не возникла новая ось вращения (биение шара).Протачиваем эту сторону шара.Процедуру повторяем до тех пор, пока не исчезнет двойной контур и не будет биения шара.Обычно на все требуется две перестановки, а по времени точение шара занимает 5-7 минут.

Шары я не лакирую, чтобы сохранить непосредственный контакт с древесиной.Протираю их льняным маслом, полирую салфеткой и стружкой.Кстати, стружка — отличный полировочный материал!
При точении шаров впервые работал с древесиной боярышника.Очень красивая, приятная древесина красно-желтого цвета с чудесным запахом.Стружка при точении получается розовой, как перья фламинго.
История токарного станка — полезная информация Токарно-винторезные станки по металлу
История относит изобретение токарного станка к 650 гг. до н. э. Станок представлял собой два установленных центра, между которыми зажималась заготовка из дерева, кости или рога. Раб или подмастерье вращал заготовку (один или несколько оборотов в одну сторону, затем в другую). Мастер держал резец в руках и, прижимая его в нужном месте к заготовке, снимал стружку, придавая заготовке требуемую форму.
Позднее для приведения заготовки в движение применяли лук со слабо натянутой (провисающей) тетивой. Тетиву оборачивали вокруг цилиндрической части заготовки так, чтобы она образовала петлю вокруг заготовки. При движении лука то в одну, то в другую сторону, аналогично движению пилы при распиливании бревна, заготовка делала несколько оборотов вокруг своей оси сначала в одну, а затем в другую сторону.
В XIV — XV веках были распространены токарные станки с ножным приводом. Ножной привод состоял из очепа — упругой жерди, консольно закрепленной над станком. К концу жерди крепилась бечевка, которая была обернута на один оборот вокруг заготовки и нижним концом крепилась к педали. При нажатии на педаль бечевка натягивалась, заставляя заготовку сделать один — два оборота, а жердь — согнуться. При отпускании педали жердь выпрямлялась, тянула вверх бечевку, и заготовка делала те же обороты в другую сторону.
Примерно к 1430 г. вместо очепа стали применять механизм, включающий педаль, шатун и кривошип, получив, таким образом, привод, аналогичный распространенному в XX веке ножному приводу швейной машинки. С этого времени заготовка на токарном станке получила вместо колебательного движения вращение в одну сторону в течение всего процесса точения.
В 1500 г. токарный станок уже имел стальные центры и люнет, который мог быть укреплен в любом месте между центрами.
На таких станках обрабатывали довольно сложные детали, представляющие собой тела вращения, — вплоть до шара. Но привод существовавших тогда станков был слишком маломощным для обработки металла, а усилия руки, держащей резец, недостаточными, чтобы снимать большую стружку с заготовки. В результате обработка металла оказывалась малоэффективной. Необходимо было заменить руку рабочего специальным механизмом, а мускульную силу, приводящую станок в движение, более мощным двигателем.
Появление водяного колеса привело к повышению производительности труда, оказав при этом мощное революционизирующее действие на развитие техники. А с середины XIV в. водяные приводы стали распространяться в металлообработке.
В середине XVI Жак Бессон (умер в 1569 г.) — изобрел токарный станок для нарезки цилиндрических и конических винтов.
В начале XVIII века Андрей Константинович Нартов (1693-1756), механик Петра первого, изобретает оригинальный токарно-копировальный и винторезный станок с механизированным суппортом и набором сменных зубчатых колес. Чтобы по-настоящему понять мировое значение этих изобретений, вернемся к эволюции токарного станка.
В XVII в. появились токарные станки, в которых обрабатываемое изделие приводилось в движение уже не мускульной силой токаря, а с помощью водяного колеса, но резец, как и раньше, держал в руке токарь. В начале XVIII в. токарные станки все чаще использовали для резания металлов, а не дерева, и поэтому проблема жесткого крепления резца и перемещения его вдоль обрабатываемой поверхности стола весьма актуальной. И вот впервые проблема самоходного суппорта была успешно решена в копировальном станке А. К.Нартова в 1712 г.
К идее механизированного передвижения резца изобретатели шли долго. Впервые эта проблема особенно остро встала при решении таких технических задач, как нарезание резьбы, нанесение сложных узоров на предметы роскоши, изготовление зубчатых колес и т.д. Для получения резьбы на валу, например, сначала производили разметку, для чего на вал навивали бумажную ленту нужной ширины, по краям которой наносили контур будущей резьбы. После разметки резьбу опиливали напильником вручную. Не говоря уже о трудоемкости такого процесса, получить удовлетворительное качество резьбы таким способом весьма трудно.
А Нартов не только решил задачу механизации этой операции, но в 1718-1729 гг. сам усовершенствовал схему. Копировальный палец и суппорт приводились в движение одним ходовым винтом, но с разным шагом нарезки под резцом и под копиром. Таким образом, было обеспечено автоматическое перемещение суппорта вдоль оси обрабатываемой заготовки. Правда, поперечной подачи еще не было, вместо нее было введено качание системы «копир-заготовка». Поэтому работы над созданием суппорта продолжались. Свой суппорт создали, в частности, тульские механики Алексей Сурнин и Павел Захава. Более совершенную конструкцию суппорта, близкую к современной, создал английский станкостроитель Модсли, но А.К. Нартов остается первым, кто нашел путь к решению этой задачи.
Вторая половина XVIII в. в станкостроении ознаменовалась резким увеличением сферы применения металлорежущих станков и поисками удовлетворительной схемы универсального токарного станка, который мог бы использоваться в различных целях.
В 1751 г. Ж. Вокансон во Франции построил станок, который по своим техническим данным уже походил на универсальный. Он был выполнен из металла, имел мощную станину, два металлических центра, две направляющие V-образной формы, медный суппорт, обеспечивающий механизированное перемещение инструмента в продольном и поперечном направлениях. В то же время в этом станке отсутствовала система зажима заготовки в патроне, хотя это устройство существовало в других конструкциях станков. Здесь предусматривалось крепление заготовки только в центрах. Расстояние между центрами можно было менять в пределах 10 см. Поэтому обрабатывать на станке Вокансона можно было лишь детали примерно одинаковой длины.
В 1778 г. англичанин Д. Рамедон разработал два типа станков для нарезания резьб. В одном станке вдоль вращаемой заготовки по параллельным направляющим передвигался алмазный режущий инструмент, скорость перемещения которого задавалась вращением эталонного винта. Сменные шестерни позволяли получать резьбы с разным шагом. Второй станок давал возможность изготавливать резьбу с различным шагом на детали большей длины, чем длина эталона. Резец продвигался вдоль заготовки с помощью струны, накручивавшейся на центральную шпонку.
В 1795 г. французский механик Сено изготовил специализированный токарный станок для нарезки винтов. Конструктор предусмотрел сменные шестерни, большой ходовой винт, простой механизированный суппорт. Станок был лишен каких-либо украшений, которыми любили украшать свои изделия мастера прежде.
Накопленный опыт позволил к концу XVIII века создать универсальный токарный станок, ставший основой машиностроения. Его автором стал Генри Модсли. В 1794 г. он создал конструкцию суппорта, довольно несовершенную. В 1798 г., основав собственную мастерскую по производству станков, он значительно улучшил суппорт, что позволило создать вариант универсального токарного станка.
В 1800 г. Модсли усовершенствовал этот станок, а затем создал и третий вариант, содержавший все элементы, которые имеют токарно-винторезные станки сегодня. При этом существенно то, что Модсли понял необходимость унификации некоторых видов деталей и первым стал внедрять стандартизацию резьб на винтах и гайках. Он начал выпускать наборы метчиков и плашек для нарезки резьб.
Одним из учеников и продолжателей дела Модсли был Р. Робертс. Он улучшил токарный станок тем, что расположил ходовой винт перед станиной, добавил зубчатый перебор, ручки управления вынес на переднюю па нель станка, что сделало более удобным управление станком. Этот станок работал до 1909 г.
Другой бывший сотрудник Модсли — Д. Клемент создал лоботокарный станок для обработки деталей большого диаметра. Он учел, что при постоянной скорости вращения детали и постоянной скорости подачи по мере движения резца от периферии к центру скорость резания будет падать, и создал систему увеличения скорости.
В 1835 г. Д. Витворт изобрел автоматическую подачу в поперечном направлении, которая была связана с механизмом продольной подачи. Этим было завершено принципиальное совершенствование токарного оборудования.
Следующий этап — автоматизация токарных станков. Здесь пальма первенства принадлежала американцам. В США развитие техники обработки металлов началось позднее, чем в Европе. Американские станки первой половины XIХ в. значительно уступали станкам Модсли.
Во второй половине XIХ в. качество американских станков было уже достаточно высоким. Станки выпускались серийно, причем вводилась полная взаимозаменяемость деталей и блоков, выпускаемых одной фирмой. При поломке детали достаточно было выписать с завода аналогичную и заменить сломанную деталь на целую без всякой подгонки.
Во второй половине XIХ в. были введены элементы, обеспечивающие полную механизацию обработки — блок автоматической подачи по обеим координатам, совершенную систему крепления резца и детали. Режимы резания и подач изменялись быстро и без значительных усилий. В токарных станках имелись элементы автоматики — автоматический останов станка при достижении определенного размера, система автоматического регулирования скорости лобового точения и т.д.
Однако основным достижением американского станкостроения было не развитие традиционного токарного станка, а создание его модификации — револьверного станка. В связи с необходимостью изготовления нового стрелкового оружия (револьверов) С. Фитч в 1845 г. разработал и построил револьверный станок с восемью режущими инструментами в револьверной головке. Быстрота смены инструмента резко повысила производительность станка при изготовлении серийной продукции. Это был серьезный шаг к созданию станков-автоматов.
В деревообработке первые станки-автоматы уже появились: в 1842 г. такой автомат построил К. Випиль, а в 1846 г. Т. Слоан.
Первый универсальный токарный автомат изобрел в 1873г. Хр. Спенсер.
Суппорт токарного станка
Одним из важнейших достижений машиностроения в начале XIX века стало распространение металлорежущих станков с суппортами — механическими держателями для резца. Введение суппорта разом повлекло за собой усовершенствование и удешевление всех машин, дало толчок к новым усовершенствованиям и изобретениям.
Суппорт предназначен для перемещения во время обработки режущего инструмента, закрепленного в резцедержателе. Он состоит из нижних салазок (продольного суппорта) 1, которые перемещаются по направляющим станины с помощью рукоятки 15 и обеспечивают перемещение резца вдоль заготовки. На нижних салазках по направляющим 12 перемещаются поперечные салазки (поперечный суппорт) 3, которые обеспечивают перемещение резца перпендикулярно оси вращения заготовки (детали).
На поперечных салазках 3 расположена поворотная плита 4, которая закрепляется гайкой 10. По направляющим 5 поворотной плиты 4 перемещаются (с помощью рукоятки 13) верхние салазки 11, которые вместе с плитой 4 могут поворачиваться в горизонтальной плоскости относительно поперечных салазок и обеспечивать перемещение резца под углом к оси вращения заготовки (детали).
Резцедержатель (резцовая головка) 6 с болтами 8 крепится к верхним салазкам с помощью рукоятки 9, которая перемещается по винту 7. Привод перемещения суппорта производится от ходового винта 2, от ходового вала, расположенного под ходовым винтом, или вручную. Включение автоматических подач производится рукояткой 14.
Устройство поперечного суппорта показано на рисунке ниже. По направляющим продольного суппорта 1 ходовым винтом 12, оснащенным рукояткой 10, перемещаются салазки поперечного суппорта. Ходовой винт 12 закреплен одним концом в продольном суппорте 1, а другим — связан с гайкой (состоящей из двух частей 15 и 13 и клина 14), которая крепится к поперечным салазкам 9. Затягивая винт 16, раздвигают (клином 14) гайки 15 и 13, благодаря чему выбирается зазор между ходовым винтом 12 и гайкой 15.
Величину перемещения поперечного суппорта определяют по лимбу 11. К поперечному суппорту крепится (гайками 7) поворотная плита 8, вместе с которой поворачиваются верхние салазки 6 и резцедержатель 5. На некоторых станках на поперечных салазках 9 устанавливается задний резцедержатель 2 для проточки канавок, отрезки и других работ, которые могут быть выполнены перемещением поперечного суппорта, а также кронштейн 3 с щитком 4, защищающим рабочего от попадания стружки и смазочно-охлаждающей жидкости.
Токарный станок имеет весьма древнюю историю, причем с годами его конструкция менялась очень незначительно. Приводя во вращение кусок дерева, мастер с помощью долота мог придать ему самую причудливую цилиндрическую форму. Для этого он прижимал долото к быстро вращающемуся куску дерева, отделял от него круговую стружку и постепенно давал заготовке нужные очертания. В деталях своего устройства станки могли довольно значительно отличаться друг от друга, но вплоть до конца XVIII века все они имели одну принципиальную особенность: при обработке заготовка вращалась, а резец находился в руках мастера.
Исключения из этого правила были очень редкими, и их ни в коем случае нельзя считать типичными для этой эпохи. Например, держатели для резца получили распространение в копировальных станках. С помощью таких станков работник, не обладавший особыми навыками, мог изготовлять затейливые изделия очень сложной формы. Для этого пользовались бронзовой моделью, имевшей вид изделия, но большего размера (обычно 2:1). Нужное изображение получали на заготовке следующим образом.
Станок оборудовался двумя суппортами, позволявшими вытачивать изделия без участия руки работника: в одном был закреплен копировальный палец, в другом — резец. Неподвижный копировальный палец имел вид стержня, на заостренном конце которого помешался маленький ролик. К ролику копировального пальца специальной пружиной постоянно прижималась модель. Во время работы станка она начинала вращаться и в соответствии с выступами и впадинами на своей поверхности совершала колебательные движения.
Эти движения модели через систему зубчатых колес передавались вращающейся заготовке, которая повторяла их. Заготовка находилась в контакте с резцом, подобно тому, как модель находилась в контакте с копировальным пальцем. В зависимости от рельефа модели заготовка то приближалась к резцу, то удалялась от него. При этом менялась и толщина стружки. После многих проходов резца по поверхности заготовки возникал рельеф, аналогичный имевшемуся на модели, но в меньшем масштабе.
Копировальный станок был очень сложным и дорогим инструментом. Приобрести его могли лишь весьма состоятельные люди. В первой половине XVIII века, когда возникла мода на точеные изделия из дерева и кости, токарными работами занимались многие европейские монархи и титулованная знать. Для них большей частью и предназначались копировальные станки.
Но широкого распространения в токарном деле эти приспособления не получили. Простой токарный станок вполне удовлетворял всем потребностям человека вплоть до второй половины XVIII века. Однако с середины столетия все чаще стала возникать необходимость обрабатывать с большой точностью массивные железные детали. Валы, винты различной величины, зубчатые колеса были первыми деталями машин, о механическом изготовлении которых встал вопрос тотчас же после их появления, так как они требовались в огромном количестве.
Особенно остро нужда в высокоточной обработке металлических заготовок стала ощущаться после внедрения в жизнь великого изобретения Уатта. Изготовление деталей для паровых машин оказалось очень сложной технической задачей для того уровня, которого достигло машиностроение XVIII века.
Обычно резец укреплялся на длинной крючкообразной палке. Рабочий держал его в руках, опираясь как на рычаг на специальную подставку. Этот труд требовал больших профессиональных навыков и большой физической силы. Любая ошибка приводила к порче всей заготовки или к слишком большой погрешности обработки.
В 1765 году из-за невозможности рассверлить с достаточной точностью цилиндр длиной в два фута и диаметром в шесть дюймов Уатт вынужден был прибегнуть к ковкому цилиндру. Расточка цилиндра длиною в девять футов и диаметром в 28 дюймов допускала точность до «толщины маленького пальца».
С начала XIX века начался постепенный переворот в машиностроении. На место старому токарному станку один за другим приходят новые высокоточные автоматические станки, оснащенные суппортами. Начало этой революции положил токарный винторезный станок английского механика Генри Модсли, позволявший автоматически вытачивать винты и болты с любой нарезкой.
Нарезка винтов долго оставалась сложной технической задачей, поскольку требовала высокой точности и мастерства. Механики давно задумывались над тем, как упростить эту операцию. Еще в 1701 году в труде Ш. Плюме описывался способ нарезки винтов с помощью примитивного суппорта.
Для этого к заготовке припаивали отрезок винта в качестве хвостовика. Шаг напаиваемого винта должен был быть равен шагу того винта, который нужно было нарезать на заготовке. Затем заготовку устанавливали в простейших разъемных деревянных бабках; передняя бабка поддерживала тело заготовки, а в заднюю вставлялся припаянный винт. При вращении винта деревянное гнездо задней бабки сминалось по форме винта и служило гайкой, вследствие чего вся заготовка перемещалась в сторону передней бабки. Подача на оборот была такова, что позволяла неподвижному резцу резать винт с требуемым шагом.
Подобного же рода приспособление было на токарно-винторезном станке 1785 года, который был непосредственным предшественником станка Модсли. Здесь нарезка резьбы, служившая образцом для изготавливаемого винта, наносилась непосредственно на шпиндель, удерживавший заготовку и приводивший ее во вращение. (Шпинделем называют вращающийся вал токарного станка с устройством для зажима обрабатываемой детали.) Это давало возможность делать нарезку на винтах машинным способом: рабочий приводил во вращение заготовку, которая за счет резьбы шпинделя, точно так же как и в приспособлении Плюме, начинала поступательно перемещаться относительно неподвижного резца, который рабочий держал на палке.
Таким образом, на изделии получалась резьба, точно соответствующая резьбе шпинделя. Впрочем, точность и прямолинейность обработки зависели здесь исключительно от силы и твердости руки рабочего, направлявшего инструмент. В этом заключалось большое неудобство. Кроме того, резьба на шпинделе была всего 8-10 мм, что позволяло нарезать только очень короткие винты.
Винторезный станок, сконструированный Модсли, представлял собой значительный шаг вперед. История его изобретения так описывается современниками. В 1794-1795 годах Модсли, еще молодой, но уже весьма опытный механик, работал в мастерской известного изобретателя Брамы.
Перед Брамой и Модсли стояла задача увеличить число деталей, изготавливаемых на станках. Однако старый токарный станок был для этого неудобен. Начав работу по его усовершенствованию, Модсли в 1794 году снабдил его крестовым суппортом.
Нижняя часть суппорта (салазки) устанавливались на одной раме с задней бабкой станка и могла скользить вдоль ее направляющей. В любом ее месте суппорт мог быть прочно закреплен при помощи винта. На нижних салазках находились верхние, устроенные подобным же образом. С помощью них резец, закрепленный винтом в прорези на конце стального бруска, мог перемещаться в поперечном направлении.
Движение суппорта в продольном и поперечном направлениях происходило с помощью двух ходовых винтов. Подвинув резец с помощью суппорта вплотную к заготовке, жестко установив его на поперечных салазках, а затем перемещая вдоль обрабатываемой поверхности, можно было с большой точностью срезать лишний металл. При этом суппорт выполнял функцию руки рабочего, удерживающего резец. В описываемой конструкции, собственно, не было еще ничего нового, но она была необходимым шагом к дальнейшим усовершенствованиям.
Уйдя вскоре после своего изобретения от Брамы, Модсли основал собственную мастерскую и в 1798 году создал более совершенный токарный станок. Этот станок стал важной вехой в развитии станкостроения, так как он впервые позволил автоматически производить нарезку винтов любой длины и любого шага.
Слабым местом прежнего токарного станка было то, что на нем можно было нарезать только короткие винты. Иначе и быть не могло ведь там не было суппорта, рука рабочего должна была оставаться неподвижной, а двигалась сама заготовка вместе с шпинделем. В станке Модсли заготовка оставалась неподвижной, а двигался суппорт с закрепленным в нем резцом.
Для того чтобы заставить суппорт перемещаться на нижних салазках вдоль станка, Модсли соединил с помощью двух зубчатых колес шпиндель передней бабки с ходовым винтом суппорта. Вращающийся винт вкручивался в гайку, которая тянула за собой салазки суппорта и заставляла их скользить вдоль станины. Поскольку ходовой винт вращался с той же скоростью, что и шпиндель, то на заготовке нарезалась резьба с тем же шагом, что была на этом винте. Для нарезки винтов с различным шагом при станке имелся запас ходовых винтов.
Автоматическое нарезание винта на станке происходило следующим образом. Заготовку зажимали и обтачивали до нужных размеров, не включая механической подачи суппорта. После этого соединяли ходовой винт со шпинделем, и винтовая нарезка осуществлялась за несколько проходов резца. Обратный отход суппорта каждый делался вручную после отключения самоходной подачи. Таким образом, ходовой винт и суппорт полностью заменяли руку рабочего. Мало того, они позволяли нарезать резьбу гораздо точнее и быстрее, чем на прежних станках.
В 1800 году Модсли внес замечательное усовершенствование в свой станок – взамен набора сменных ходовых винтов он применил набор сменных зубчатых колес, которые соединяли шпиндель и ходовой винт (их было 28 с числом зубьев от 15 до 50).
На своем станке Модсли выполнял нарезку резьб с такой изумительной точностью и аккуратностью, что это казалось современникам почти чудом. Он, в частности, нарезал регулировочные винт и гайку для астрономического прибора, который в течение долгого времени считался непревзойденным шедевром точности. Винт имел пять футов длины и два дюйма в диаметре с 50-ю витками на каждый дюйм. Резьба была такой мелкой, что ее невозможно было рассмотреть невооруженным глазом. В скором времени усовершенствованный Модсли станок получил повсеместное распространение и послужил образцом для многих других металлорежущих станков. В 1817 году был создан строгальный станок с суппортом, позволивший быстро обрабатывать плоские поверхности. В 1818 году Уитни придумал фрезерный станок. В 1839 году появился карусельный станок и т.д.
Нартов Андрей Константинович (1683 — 1756)
Деятель времени Петра Великого. Русский механик и изобретатель. Учился в Школе математических и навигацких наук в Москве. Около 1718 года был послан царем за границу для усовершенствования в токарном искусстве и «приобретения знаний в механике и математике». По указанию Петра I, Нартов вскоре был переведен в Петербург и назначен личным токарем царя в дворцовой токарной мастерской.
Работая здесь в 1712-1725, Нартов изобрел и построил ряд совершенных и оригинальных по кинематической схеме токарных станков (в том числе копировальных), часть которых была снабжена механическими суппортами. С появлением суппорта решалась задача изготовления частей машин строго определенной геометрической формы, задача производства машин машинами.
В 1726-1727 и в 1733 Нартов работал при Московском монетном дворе, где создал оригинальные монетные станки. В том же 1733 году Нартов создал механизм для подъема «Царь колокола». После смерти Петра, Нартову было поручено сделать «триумфальный столп» в честь императора, с изображением всех его «баталий».
Когда в Академию Наук были сданы все токарные принадлежности и предметы Петра, а также и «триумфальный столп», то, по настоянию начальника академии, барона Корфа, считавшего Нартова единственным человеком, способным окончить «столп», он был переведен в академию «к токарным станкам», для заведывания учениками токарного и механического дела и слесарями. Петровская токарня, превращенная Нартовым в академические мастерские, послужила базой для последующих работ М. В. Ломоносова, а затем И. П. Кулибина (особенно в области приборостроения).
В 1742 году Нартов принес Сенату жалобу на советника академии Шумахера, с которым у него происходили пререкания по денежному вопросу, а затем добился назначения следствия над Шумахером, на место которого был определен сам Нартов. В этой должности он пробыл только 1,5 года, потому что оказался «ничего кроме токарного художества незнающим и самовластным»; он велел запечатать архив академической канцелярии, грубо обращался с академиками, и наконец, довел дело до того, что Ломоносов и другие члены стали просить возвращения Шумахера, который вновь вступил в управление академией в 1744 году, а Нартов сосредоточил свою деятельность «на пушечно-артиллерийском деле».
1738-1756, работая в Артиллерийском ведомстве, Нартов создал станки для сверления канала и обточки цапф пушек, оригинальные запалы, оптический прицел; предложил новые способы отливки пушек и заделки раковин в канале орудия. В 1741 Нартов изобрел скорострельную батарею из 44 трехфунтовых мортирок. В этой батарее впервые в истории артиллерии был применен винтовой подъемный механизм, который позволял придавать мортиркам желаемый угол возвышения.
В обнаруженной рукописи Нартова «Ясное зрелище махин» описывается более 20 токарных, токарно-копировальных, токарно-винторезных станков различных конструкций. Выполненные Нартовым чертежи и технические описания свидетельствуют о его больших инженерных познаниях. Он издал также: «Достопамятные повествования и речи Петра Великого» и «Театрум махинарум».
Генри Модсли (Maudslay Henry 1771-1831)
Английский механик и промышленник. Создал токарно-винторезный станок с механизированным суппортом (1797), механизировал производство винтов, гаек и др. Ранние годы провел в Вулвиче под Лондоном.
В 12 лет стал работать набивальщиком патронов в Вулвичском арсенале, а в 18 лет он лучший кузнец арсенала и слесарь-механик, в мастерской Дж. Брама — лучшей мастерской Лондона. Позже открыл собственную мастерскую, потом завод в Ламбете.
Создал «Лабораторию Модсли». Дизайнер. Машиностроитель. Создал механизированный суппорт токарного станка, собственной конструкции. Придумал оригинальный набор сменных зубчатых колес. Изобрел поперечно-строгальный станок с кривошипно-шатунным механизмом. Создал или усовершенствовал большое количество различных металлорежущих станков. Строил для России паровые корабельный машины.
Изготовление деревянных шаров. Точение шаров. Как расточить деревянный шар с помощь специального устройства
Деревянные шары в нашей стране точат и продают, что я видел недавно на одной из декоративно-прикладных выставок. Но это шары, предназначенные для дальнейшей росписи, и, потому, так сказать, в голом виде не имеющие самостоятельной художественной ценности. Их точат из липы – породы, по моим понятиям, для точения совершенно не пригодной, если, конечно, не планируется в дальнейшем раскрасить, обжечь, текстурировать или нанести резьбу на крайне невыразительную поверхность изделия. Не исключаю, что отечественная техника точения шаров весьма отличается от нижеописанной международной, но она нигде не представлена.
При работе с деревом остается много обрезков, которые жалко выбросить, а места они занимают все больше. Целесообразно использовать их для точения шаров, которые, на мой взгляд, обладают значительной художественной ценностью и притягательностью, особенно, если они выполнены из красивой древесины. В Интернете можно найти ряд зарубежных работ по технике точения шаров, если набрать в поисковой строке, например, “Woodturning balls (spheres)”. Там уже имеются в продаже и специальные приспособления для точения шаров, применение которых, как представляется, может быть оправдано лишь при серийном производстве. Точить шары в ручном режиме довольно просто.
Сначала заготовка, например, отрезок тонкого ствола или толстого сучка, диаметром, скажем, 80 мм, закрепляется продольно и грубо обрабатывается (оцилиндровывается) в центрах токарного станка, а затем доводится до формы правильного шара в самодельных чашеобразных зажимах. Эти зажимы (передний и задний) изготавливаются из обрезков твердого дерева, например, клена или бука. Передний зажим в принципе может крепиться на шпинделе передней бабки самыми разнообразными способами: на планшайбе c шурупом (деревянной или металлической), с помощью деревянной резьбы (см. мое недавнее сообщение), в патроне с кулачками на сжим или враспор, а также с помощью конуса Морзе №2 (КМ2). Последний способ является наиболее удобным и распространенным, а процесс изготовления такого зажима из клееной заготовки показан на фото 1- 5. Длина КМ2 обычно составляет около 70 мм с диаметром 17,5 мм в начале и
15 мм в конце. Размеры уточняются в процессе точения путем сравнительных измерений штангенциркулем металлического и деревянного КМ2 с рядом примерок в пиноли задней бабки станка. Ровность горизонтальной поверхности проверяется сначала линейкой, а затем силовым проворачиванием в пиноли и удалением ставших заметных на глаз неровностей, например с помощью скребка, косяка или просто шлифовальной шкурки. Если внутри пиноли имеется грязь, то она оставит
темные следы на поверхности древесины, в противном случае сжатые волокна неровностей проявятся в виде блеска, заметного при освещении под определенным углом. С деталями изготовления деревянного КМ2 можно познакомиться в Интернете, набрав, например, “Turning a wooden Morse taper”. Я изготовил два передних зажима с диаметром губок около 25 и 55 мм, что позволяет точить шары приблизительно от 50 до 150 мм в диаметре, поскольку первая величина должна составлять около 1/3 – 1/2 от последней. Важно, чтобы губки чашеобразных зажимов не имели острых краев, способных оставлять следы на поверхности обрабатываемых шаров.
Задние чашеобразные зажимы, которые крепятся на заднем центре, могут иметь меньший диаметр губок, чем передние, поскольку их основная задача – лишь служить подпоркой. У меня имеются три разных задних вращающихся центра и я сделал задние зажимы для двух из них: корончатого диаметром 32 мм и кольцевого диаметром 37,5 мм. Диаметры губок были 26 мм и 35 мм. Полость для более узкого центра я высверлил в обточенном цилиндре с помощью сверла Форстнера диаметром 32 мм (фото 6 и 7), а для
более толстого выточил на станке с помощью стамесок (фото 8). На фото 9 представлены готовые задние зажимы для соответствующих вращающихся центров.
Центральные отверстия диаметром 8 мм сделаны для выталкивания центров в случае возникновения трудностей с их освобождением.
На фото 10 показан процесс черновой обработки (оцилиндровывание) дубовой заготовки для шара диаметром около 80 мм. Древесина должна быть сухой, чтобы
избежать в дальнейшем коробления и растрескивания готового изделия. Длина заготовки с припусками – около 100 мм. Карандашом наносится центральная поперечная линия, делящая заготовку пополам, и по обе стороны от неё откладываются отрезки по 40 мм, желательно с небольшими припусками в 2-3 мм (фото 11). Далее заготовка скругляется, т.е. срезаются боковые углы (фото 12). Я это делаю наиболее привычной мне глубокожелобчатой стамеской, но можно
использовать и другие стамески, такие как мелкожелобчатая (полукруглая) или косая.
Скругление производится на глаз, при этом центральная линия должна оставаться нетронутой. Потом с помощью отрезной стамески устраняются опорные выступы (фото 13), заготовка, развернутая на 90 градусов, фиксируется в деревянных зажимах (фото 14) и с помощью той же глубокожелобчатой стамески (или любой другой) производится
дальнейшее её скругление (фото 15). При этом устраняется так называемый “двойной контур”, свидетельствующий о неправильной форме шара. Далее заготовка вновь разворачивается на 90 градусов и точится той же стамеской со срезанием все меньшего объема древесины. И так несколько раз до полного устранения “двойного контура” и биения заготовки. Чистовую обработку поверхности выточенного шара можно проводить как “крыльями” глубокожелобчатой стамески, так и прямоугольным скребком, показанным на фото 3, а еще лучше скребком с отрицательным углом. О завершенности процесса скругления заготовки может говорить отсутствие вибрации стамески, положенной сверху на шар. Конечной операцией является шлифовка шара шкурками последовательно уменьшающейся зернистости: P80, 120, 180 и 240 (фото 16). При этом все время следует менять направление оси шара, как это делалось при его точении. При последних
операциях со снятием небольших слоев древесины я часто фиксирую шар в малых зажимах для увеличения доступной рабочей поверхности, особенно при шлифовке. На фото 17 показан отшлифованный дубовый шар, готовый для лакирования поверхности. Если его поверхность предполагается не лакировать, а отделывать маслом и/или воском, следует продолжить шлифование шкурками с зернистостью хотя бы до Р400-600, а лучше до P1500.
Выточив с десяток шаров, понял, что никакая предварительная разметка на цилиндре не нужна и вполне можно делать все на глаз. Скорость вращения заготовки должна быть около 2000 об/мин, а то и выше, в зависимости от диаметра шара. Чем выше скорость, тем чище получается поверхность древесины, но и тем выше опасность вылетания шара из зажимов. Усиливая зажим, рискуешь оставить вмятины на поверхности заготовки, особенно из мягкой древесины, от которых трудно будет избавиться. Точение шара занимает обычно 5-10 минут.
Идучи как-то к дому по задворку заметил и подобрал свежеспиленный сук тополя серебристого толщиной около 100 мм с соблазнительно выделяющимся ядром на срезе. Распилил на ряд коротких заготовок, грубо проточил их до шара, завернул в газеты и полиэтиленовые пакеты и поместил на горячую батарею отопления. Время от времени разворачивал обертки и шары высохли приблизительно через неделю. Вновь поставил на станок и довел форму шаров до совершенства, проявившую заодно и красоту текстуры тополя. Для удобства использовал зажимы с малыми губками, в результате чего на мягкой древесине тополя отпечатались сначала их малозаметные следы, которые отчетливо проявились при последующей лаковой отделке поверхности. Избавиться от них оказалось очень трудно, если только не сошлифовать толстый слой древесины. Сжатые волокна все время распрямляются. Вывод: для работы с шарами из мягкой древесины желательно сделать и зажимы с губками из мягкой древесины. Возможно, целесообразно обклеить губки мягким пластиком, например, ковриком под посуду. В моей практике точения крупных шаров два или три передних зажима разлетелись из-за того, что их чаши оказались тонковатыми, поэтому их надо делать достаточно массивными и клееными (фото 18).
Я лакировал шары, держа их в руке и тут же подсушивая феном, а затем помещал для досушивания сначала в чашеобразные углубления деревянных зажимов, а затем выточил пяток простеньких подставок (фото 19). Поверхность лакировалась 3-4 раза с промежуточными шлифовками и конечной располировкой по единой методике, ранее уже описанной мной в отдельном сообщении (с некоторыми усовершенствованиями). Вытачивание шаров, помимо прочего, помогает на самых простых формах выявлять красоту различных пород деревьев в здоровом и подгнившем состоянии, а также испытывать разнообразные способы отделки поверхности: лаком или воском, с маслом и без него. Например, еще раз я убедился, что лакированные деревянные изделия обладают бо́льшей притягательностью, чем вощеные, по крайней мере для меня и моих близких. Их хочется трогать и при этом можно не бояться эффекта “захватанности” поверхности.
Шары красиво смотрятся в тарелках. Я достал из запасов здоровый чурбак красиво подгнившей ольхи и выточил из неё несколько неглубоких тарелок. Каждый шар красив сам по себе, но их комбинация просто обворажительна. Притягательны даже белые шары из такого вроде бы скудного дерева, как клен ясенелистный (американский). Ну а самой примечательной текстурой обладают, как мне кажется, шары из сливы, желтой и белой акаций, подгнившей рябины, крушины ломкой, а также березового нароста.
Бо́льшая часть собранных мною стволов, хранящихся на балконе, растрескалась, что вполне естественно, так как сушить стволы и сучья надо в сыром подполе, особенно фруктовых деревьев, таких как яблоня, слива и груша. В ряде случаев, поэтому, пришлось делать вклейки в стволы и готовые шары. Это, с одной стороны, весьма трудозатратно, а с другой, нет никакой гарантии, что разные участки древесины в дальнейшем не будут “ играть“ по-разному и вклейки не станут более заметны, чем вначале. Следует изначально учитывать это при выборе материала для вытачивания шаров.
На фото 20 и 21 представлена значительная часть выточенных мною шаров. В качестве художественных подставок под отдельные шары пригодились ранее сделанные чаши, не представлявшие сами по себе особой художественной ценности (фото 22, 23 и 24).
Фото 24. Шар из крушины ломкой диам. 67 мм-в подставке из березового сувеля
Шар из дерева можно использовать для разных потех и серьезных дел. Это и игрушка для детей и основа для массажера для взрослых и детишек. А большой деревянный шар, который можно изготовить из довольно большой чурки, является уже готовым массажером.
Его можно положить на мягкую поверхность, например, на ковер, и катаясь по нему спиной, разминать суставы, давая крови возможность вновь разгуляться в прилегающих сосудах. Деревянный шар после изготовления можно обработать специальными составами, протравами, лаком и др. для придания благородного вида. Такая вещь будет интересно смотреться на вашем столе, если сделать под нее подставку, чтобы шар не скатывался. Большой шар как элемент декора можно положить на пол, также с подставкой, подвесить его и др.
Как же сделать шар из деревянной заготовки?
В этом видео показаны несколько способов такой работы в каждом случае от черновой обработки до .
Как расточить деревянный шар с помощь специального устройства
Комментарии
Иван Баев
Год назад
Спасибо, Гриша, за двойной позитив.Прекрасное муз. сопровождение и за приспособу. Пока смотрел на её работу, в голове целый рой мыслей о том как я буду себе делать. Жалко видео короткое, не успел додумать.
Вячеслав Башмаков
Год назад
Гриша,классно! Золотые руки, хоть и побитые. Получил истинное наслаждение от просмотра ролика. Пусть молодые поучатся делать настоящие ролики, а то задолбали ихние “бум-бум”.Если ни хрена не понимаешь в музыке, то делай без нее.
Леонид Пустовойтов
Год назад
Григорий все здорово, практически качественно и очень интересная приспособа.А можно узнать как такую изготовить, буду благодарен за помощь. Заранее спасибо.
Как сделать футбольный мяч из дерева
История материалов, которые применяются для изготовления авторучек, восходит к древнейшим временам, когда свойства природных веществ, таких, как рог, воски и битумы, использовались людьми в практических целях. Эти материалы были полимерами, в которых молекулы (мономеры) связываются между собой и образуют цепи в процессе схватывания и отверждения. Они, по сути дела, являются пластиками и, как во всех пластиках, основной их компонент — углерод.
Постепенно люди узнали, что свойства подобных материалов можно улучшить при помощи таких методов, как очистка и модифицирование другими веществами, однако лишь в XIX столетии многие новые отрасли промышленности стали испытывать нужду в материалах, обладающих такими свойствами, которых нельзя было найти в природе. Это послужило стимулом к созданию целого ряда новых материалов, в том числе первых пластмасс.
Металл широко применялся на протяжении столетий для самых различных целей, включая изготовление перьев. Бронзовые перья был найдены в руинах Помпеи.
Мастера изготовляли также перья ручной работы, в том числе многие — из драгоценных металлов, в соответствии с особыми запросами богатых заказчиков.
По мере развития технологии машинного производства и металлургии в производстве стали использовать самые разнообразные материалы, включая латунь, серебро и золото. Из этих материалов изготовлялись детали авторучек, в особенности крышки и корпуса. Во многих случаях неблагородный металл, например, латунь, покрывали тонким слоем благородного металла, такого, как золото и серебро. Технологические процессы первоначально включали в себя накатку слоя благородного металла на поверхность неблагородного, однако в настоящее время техника гальванического покрытия вытеснила этот процесс, поскольку она обеспечивает создание более стойкого покрытия. Во многих случаях нержавеющая сталь успешно использовалась для изготовления прочных и дешевых корпусов и крышек, которые очень нравились покупателям. Иногда такие металлы, как палладий и тритий, успешно использовались при изготовлении авторучек. Еще в 1970 г. легкий, но чрезвычайно твердый титан с трудом поддавался обработке при изготовлении авторучек, однако современная технология значительно облегчила его использование, и сегодня производители предлагают несколько разновидностей титановых авторучек.
Первые авторучки (в XIX столетии) изготовлялись из жесткого саженаполненного каучука. Их внешний вид был улучшен благодаря нанесению различных узоров на гравировальных станках. Наиболее привлекательным, однако, стал внешний вид авторучек, когда корпус из жесткого каучука покрывали драгоценными металлами — золотом и серебром. Покрытие выполнялось в форме филиграни или сложных узоров.
За этими великолепными первыми экземплярами авторучек, украшенных орнаментом из металла, сегодня охотятся коллекционеры всего мира.
Деревянные авторучки изготовлялись несколькими производителями с использованием токарной обработки или даже с инкрустацией. Это стало осуществимым прежде всего благодаря широкому выбору древесины, ее красоте и удобству практического использования, в результате чего появилась возможность выбирать те или иные виды древесины для самых различных целей.
Однако древесина, используемая для производства авторучек, даже после обрезки, сушки и обточки на токарном станке разбухает, усыхает, коробится или трескается, в зависимости от климатических условий. Она также пориста, и необходимо герметизировать наружную поверхность для защиты от внешний воздействий и уменьшения поглощения влаги. Примером используемых древесных пород являются эрика древовидная, клен, олива и очень редкое змеиное дерево.
Лак — общее название для всех видов покрытий, образующих твердую, гладкую и блестящую поверхность. В сфере производства авторучек один и тот же термин означает два совершенно разных вида лака — синтетический и китайский.
Наиболее часто используемым покрытием является лак, изготовляемый из инертных химических веществ, которые обычно наносят распылением в несколько слоев на вращающиеся латунные корпуса или крышки. Это покрытие красиво и прочно. Кроме того, оно обеспечивает практически неограниченное разнообразие отделки поверхности, например, под мрамор, и дает возможность изготовлять красивые, долговечные и вместе с тем недорогие принадлежности для письма.
Более дорогостоящие покрытие из китайского, или восточного, лака — растительного происхождения. Для изготовления лака используется смолистый сок, собираемый с небольших деревьев, которые принадлежат к семейству «сумах» и произрастают главным образом в Китае и Японии. Хотя искусство изготовления изделий, покрытых лаком, насчитывает столетия, а методы менялись со временем, сегодня изготовление авторучек с покрытием из китайского лака требует той самой сосредоточенной, внутренней дисциплины, отношения к лаку как к одушевленному существу, которое трудно «укротить» и с которым нелегко работать. Оно требует также досконального знания традиций мастерства, зародившегося за 1000 лет до нашей эры.
Авторучки, покрытые китайским лаком, приводят в восхищение идеальным глянцем поверхности, богатством оттенков, превосходными тактильными свойствами, а также непревзойденной сопротивляемостью разрушительным воздействиям времени и огня. Прекрасные образцы изделий, покрытых китайским лаком, изготовляет престижная фирма S.T. Dupont, которая гордится тем, что, «если бросить одну из наших ручек в огонь, все равно с ней ничего не случится».
ПЛАСТИЧЕСКИЕ МАТЕРИАЛЫТермин «пластик» происходит от древнегреческого слова «пластикос» (податливый). Следовательно, пластмассы — это материалы, которые можно размягчить под действием тепла и которым можно придать желаемую форму. Одни пластики, подобно рогу, естественного происхождения, другие, подобно нитроцеллюлозе, являются полусинтетическими, и получают их путем воздействия химических реагентов на природные вещества. Синтетические пластмассы изготовляют из компонентов нефти или природного газа.
Все пластики имеют в своей основе углерод и содержат ряд молекул в форме цепей. Существуют две главные категории пластиков — термопласты, которые сохраняют способность к переходу в вязкотекучее состояние с изменением формы, и реактопласты, которые принимают постоянную конкретную форму в зависимости от температуры и давления.
ПЕРВЫЕ ПЛАСТИКИСуществует множество первых пластиков. Уже говорилось о том, что китайский лак — один из самых первых в мире пластиков. Особенно широко применялся он в период правления императорской династии Хань (начиная со II столетия до н.э.). Смолистый сок, получаемый из древесины «сумаха лаконосного» (Rhus verniciflua), произрастающего главным образом в Китае и Японии, собирают из надрезов в коре и процеживают. При этом необходимо соблюдать осторожность, ибо смолистый сок ядовит и может вызвать сильные ожоги. Под действием воздуха, в присутствии лакказы (энзима, который играет роль отвердителя), происходит полимеризация, и лак высыхает и затвердевает, образуя блестящее, прочное и водостойкое покрытие.
ЯНТАРЬ — это природный термопласт, окаменевшая смола ископаемых хвойных деревьев из рода сосен Pinus succinifer, которые произрастали 40 — 60 млн. лет назад. Янтарь твердый, легкий и на ощупь теплый; он ярко окрашен и блестит. Если его потереть, он может притягивать к себе другие предметы. Янтарю также приписывают некие магические свойства. Основные методы обработки янтаря сводятся к процессам, которые требуют нагрева, осветления и прессования в плитки. Основная область применения янтаря — изготовление бус одинакового цвета и состава.
РОГ можно нагревать и раскалывать, размягчить в кипятке, затем выровнять и придать ему желаемую форму по методу горячего прессования. В результате рог ведет себя как типичный листовой материал из термопласта. К началу XIX столетия промышленность по изготовлению изделий из отформованного рога процветала; в основном из рога делали гребни. В наше время несколько специализированных фирм изготовляют авторучки с корпусами и крышками из рога. Самые красивые авторучки из рогового вещества производит японская компания Mannenhitsu Hakase; все ручки изготовляются вручную.
Вид ЧЕРЕПАХОВОГО ПАНЦИРЯ , обычно используемого в производстве авторучек, — это роговые большие роговые пластинки, покрывающие костистый верхний щит черепахи биссы; их можно резать и прессовать, как рог, однако всегда таким образом, чтобы сохранился природный узор. Красота узоров черепахового панциря побуждает изготовителей авторучек воспроизводить эти расцветки и узоры на многих лакированных принадлежностях для письма. В наше время для отделки поверхностей применяется в основном синтетический лак.
ШЕЛЛАК — это природная смола животного происхождения, вырабатываемая крошечными насекомыми — лаковыми червецами (Coccus lacca), которые обитают на древесных тропических и субтропических растениях определенных пород. Шеллак — термопласт, он запатентован в США Сэмьюэлем Пеком в 50-х гг. XIX столетия в качестве материала для изготовления прессованных изделий. Шеллак можно смешивать с мелкими древесными опилками и прессовать, придавая ему различные формы, например, делать из него рамки для фотографий. Составы, приготовленные из шеллака, использовались вплоть до 40-х гг. для прессования грампластинок, а в наши дни шеллак применяется для изготовления сургуча. Это — важный материал, используемый при ремонте авторучек.
ДРЕВЕСНАЯ МАСТИКА. Древесные опилки, смешанные с альбумином, образуют реактопласт. Материал был запатентован Лепажем в 50-х гг. XIX столетия. Используется в основном для изготовления декоративных тарелок, рукояток ножей, домино, ювелирных изделий.
ГУТТАПЕРЧА — пластик природного происхождения, срезаемый с коры дерева из рода палаквиум, которое произрастает в Малайе. Из гуттаперчи изготовлялись самые разнообразные изделия, которые находили применение в быту, и технические изделия, от ювелирных изделий и мебели до изоляции подводных телеграфных кабелей, проложенных в 1850 г. Хотя этот материал не слишком прочен, он по-прежнему используется сегодня в оболочках мячей для гольфа.
ПОЛУСИНТЕТИЧЕСКИЕ МАТЕРИАЛЫВ XIX столетии ученые обнаружили, что природные вещества вступают в реакцию с различными химическими препаратами, образуя новые полусинтетические материалы. Основные из них, используемые в производстве принадлежностей для письма, перечислены ниже.
РЕЗИНА. Примерно в 1838 г. Чарльз Гудьир, разорившийся американский производитель чугуна, изобрел процесс вулканизации каучука. Одновременно с Гудьиром добились такого же успеха братья Хэнкок из Англии. Вулканизированный каучук получил название эбонита или вулканизата. Процесс заключается в добавлении различных количеств серы в природный каучук, который становится более твердым и более эластичным. От природы каучук темного цвета, однако в случае необходимости его можно окрасить пигментом, чтобы изменить внешний вид.
К концу XIX столетия и вплоть до начала 20-х гг. XX столетия большинство производителей авторучек изготовляло их из вулканизированного каучука. Двумя характерными примерами могут служить авторучки Jack-Knife фирмы Parker и Ripple фирмы Waterman. Первые были главным образом черными или черными с отделкой поверхности, вторые изготовлялись из не имеющего пятен вулканизированного жесткого каучука и были двухцветными, что выглядело очень красиво; самыми популярными из них были авторучки с пестрой поверхностью в красных и белых крапинках.
КАЗЕИН. Продукт был запатентован в Германии в 1899 г. под названием «галалит» (по-гречески «молочный камень»). Процесс приготовления казеина заключается в том, что в сепарированное, обезжиренное молоко добавляют сычужный фермент. В результате получается сычужный казеин. Затем его сушат, обрабатывают и окрашивают. Используя технологию экструзии, из материала изготовляли стержни и раскатывали их в листы. (Экструзия — метод, при котором шнек перемещает исходный материал вдоль цилиндрического корпуса при высокой температуре и высоком давлении. Пространство, в котором размягченный материал может перемещаться с помощью шнека, постепенно уменьшается, и в результате материал становится вязкотекучим. Затем его продавливают через небольшие отверстия в экструзионной головке при атмосферном давлении и температуре атмосферного воздуха. В результате материал расширяется и принимает ту или иную форму в зависимости от конфигурации отверстия. Его разрезают на куски требуемой формы и требуемого размера и, наконец, сушат).
После выхода из экструдера казеин отверждают, погружая в формальдегид, а затем подвергают механической обработке. Казеин производится с целой гаммой ярких узоров и расцветок; он находил применение в различных отраслях промышленности, включая изготовление пуговиц. Фирма Parker использовала этот материал для изготовления авторучек модели Ivorines. Но, к сожалению, казеин — пористое вещество, и он со временем он начинает давать усадку. Это влияло на внешний вид авторучек Ivorines: если вследствие усадки корпуса пипетка была повреждена и чернила проливались, казеин загрязнялся. В 80-х гг. прошлого века фирма Waterman использовала аналогичный материал для изготовления авторучек серии Lady Elsa. Эти ручки, которые заправлялись сменными баллонами для чернил, не столь легко загрязнялись, и в этом смысле им повезло больше, нежели ручкам Ivorines.
ПЛАСТИКИ НА ОСНОВЕ ПРОИЗВОДНЫХ ЦЕЛЛЮЛОЗЫ. Изготовляются путем химического модифицирования целлюлозы, этого полимера естественного происхождения, из которого состоит примерно 1/3 всей фитомассы нашей планеты. Целлюлозу можно превратить в тонкую пленку (целлофан), искусственное волокно или в термопласт. Существует много производных целлюлозы, играющих наиболее важную роль в изготовлении авторучек; среди них — нитроцеллюлоза, ацетилцеллюлоза, пропионат целлюлозы и ацетобутират целлюлозы. К числу их общих физических свойств принадлежат высокое сопротивление истиранию, высокая газопроницаемость, хорошие электроизоляционные свойства, средняя проницаемость водяных паров и хорошая прозрачность.
НИТРОЦЕЛЛЮЛОЗА. Это вещество получают прямым нитрированием целлюлозы азотной кислотой, при помощи различных методов. Нитроцеллюлоза может быть прозрачной, непрозрачной или цветной. Продукт обладает вполне удовлетворительной безусадочностью, низким водопоглощением и достаточно высокой ударной вязкостью. Он, однако, довольно неустойчив к воздействию тепла и прямых солнечных лучей. Его можно формовать лишь при помощи ограниченного количества методов. Он также легко воспламеняется.
Нитроцеллюлозу подвергают обработке, смешивая с пластификатором, этиловым спиртом и другими растворителями для получения вязкой пластичной массы. Затем этот продукт подвергают сжатию или экструзии и старению для того, чтобы удалить остатки растворителя. Обычно пластификатором служит камфора, которую используют в производстве целлулоида. Из целлулоида изготовляют многие предметы личного пользования, в том числе гребни и детские игрушки. Другие фирменные названия целлулоида — ксилонит, паркесит, кодалотид и пирамин (фирма Du Pont).
Британский химик Александр Паркер из Бирмингема изобрел ксилонит в 1855 г. Добавляя различные масла в нитроцеллюлозу, он получил пасту, которая после высушивания выглядела как слоновая кость или рог. Изобретатель назвал это вещество «паркесином» и изготовил из него несколько изделий, которые экспонировались на Всемирной выставке 1962 г. в Лондоне. Паркер был удостоен почетной награды за отличное качество продукции.
В 1870 г. братья Хайатт запатентовали свой продукт — целлулоид, в котором они использовали камфору, а не оливковое масло, как в паркесине. В 1924 г. фирма Sheaffer изготовила пластмассовые авторучки, используя аналогичный материал — пироксилин, дав ему фирменное название «радит». Двумя годами позже фирма Parker использовала этот материал для изготовления авторучек модели Duofold, присвоив ему фирменное название «перманит».
Сырой пироксилин сохнет очень долго, от шести месяцев до нескольких лет. Если пироксилин высох не полностью, материал может деформироваться или даже расплавиться при машинной обработке в результате образования тепла. Специальные устройства для подачи смазочно-охлаждающей жидкости при сверлении и сушка горячим воздухом помогают решить эти проблемы. Тем не менее пластмассовые компоненты авторучек иногда дают усадку после изготовления.
Нитроцелюлоза чрезвычайно взрывоопасна и огнеопасна. В середине 20-х гг. на фабрике фирмы Wahl Eversharp в Чикаго произошло несколько взрывов. Проблемы, однако, вскоре удалось решить, и к 1928 году были созданы сложные узоры, например, сочетание перламутра и черного цвета. Перламутровая расцветка была получена путем добавления «жемчужной эссенции» в нитроцеллюлозу. Эссенцию приготовляли из химического соединения «гуанин», образующего небольшие плоские, блестящие кристаллы на чешуе некоторых видов рыб. Позднее фосфорнокислый свинец(2) был использован для отделки поверхности под перламутр. С этой целью два бруска двух цветов были измельчены на частицы требуемого размера, и эти частицы были расплавлены путем смешивания их с растворителем и воздействия высокого давления. Получившийся в результате черно-перламутровый брусок можно было подвергнуть термообработке и высушить, прежде чем изготовить из него крышки и корпуса для авторучек.
Новые пластики были не только привлекательными на вид, но и неломкими, поэтому привлекательность пластмассовых авторучек для широкой публики значительно возросла, тем самым стимулируя сбыт. В 30-х гг. многие производители авторучек, в том числе фирма Parker с ее моделями типа Vacumetric, изготовляли пластмассовые авторучки с прозрачным резервуаром или с кольцевым прозрачным окном, что позволяло следить за процессом наполнения ручки чернилами и за их расходованием. Материалы для ручек Vacumetric изготовлялись путем спрессовывания в бруски слоев прозрачной и непрозрачной нитроцеллюлозы и сложных эфиров целлюлозы. Затем бруски окрашивали и заливали наполнителем. Конечные бруски можно было нарезать тонкими слоями, чтобы изготовить детали авторучки. В результате получался узор в виде либо мозаики, либо сетки.
Материал в полоску для авторучек серии Vacumatic изготовлялся точно таким же образом, с применением полупрозрачной и непрозрачной нитроцеллюлозы, которую окрашивали и придавали ей цвета перламутра, если это требовалось. Материал нарезали тонкими слоями и спрессовывали в бруски, из которых можно было затем изготовлять детали авторучек.
АЦЕТИЛЦЕЛЛЮЛОЗА. В результате реакции уксусной кислоты и уксусного ангидрида с технической целлюлозой образуется триацетат целлюлозы. При гидролизе этого вещества образуется ацетилцеллюлоза. Применение пластификатора снижает температуру размягчения целлюлозы, что позволяет производить ее обработку без ухудшения свойств. Меняя дозировку пластификатора, уровень этерификации и длину молекулярной цепи исходной целлюлозы, можно получить семейство пластиков. Они различаются между собой по температуре размягчения, твердости, прочности и ударной вязкости.
ПРОПИОНАТ ЦЕЛЛЮЛОЗЫ И АЦЕТОБУТИРАТ ЦЕЛЛЮЛОЗЫ. Оба эти вещества образуются путем замены уксусной кислоты и уксусного ангидрида соответствующими кислотами и ангидридами. Сложные эфиры сплавляют с пластификатором в условиях высокой температуры и высокого давления для получения однородных расплавов, которые формуются в стержни и гранулы. Пропионат и ацетобутират целлюлозы изготовляются также в форме порошка. Стоят они дороже, чем ацетилцеллюлоза, но зато обладают повышенной прочностью и более стабильны, поскольку характеризуются более низким водопоглощением. Помимо изготовления принадлежностей для письма, пропионат целлюлозы часто применяют для изготовления блистерной упаковки (из полимерной, термоформованной жесткой пленки) и формованной тары, деталей автомашин, таких, например, как рулевые колеса, осветительных приборов и игрушек.
В настоящее время фирмы производят широкий ассортимент цветных пластмасс с использованием нитроцеллюлозы и ацетилцеллюлозы; из этих материалов обычно изготовляются оправы для очков, модные аксессуары и т.д. Новейшая технология дает возможность изготовлять эти материалы в виде более толстых листов, благодаря чему производители авторучек смогли использовать их при изготовлении принадлежностей для письма.
МЕТАЛЛЫЧистые металлы, как правило, из-за своих механических свойств непригодны для использования в производственных процессах. С другой стороны, можно изготовить сплавы металлов, обладающие такими свойствами, которые делают их пригодными. Сплавом называется материал с металлическими свойствами, содержащий более одного компонента. Сплавы могут иметь сложный состав, и два сплава с одинаковым химическим составом могут обладать совершенно разными свойствами, если их подвергнуть различным видам термической обработки.
Сплавы, которые чаще всего применяются в производстве авторучек, изготовляются на основе латуни, стали, никеля, серебра и золота. Металлы обладают значительным преимуществом по сравнению с другими материалами, используемыми в производстве авторучек, поскольку кристаллографическая структура большинства обычно применяемых сплавов обеспечивает крайне необходимые механические свойства, такие, как твердость, упругость и пластичность. Это позволяет применять самые различные методы горячей и холодной обработки для изготовления компонентов авторучек, которым легко придать нужную форму. Помимо универсальности в применении, сплавы металлов обладают приятным внешним видом. Кроме того, применение покрытий дает возможность производителям авторучек изготовлять обширный ассортимент долговечных и красивых инструментов для письма, способных удовлетворить индивидуальные требования.
Металлические детали можно изготовлять при помощи целого ряда технологических процессов — прокатки, ковки, экструзии; относительно легкая деформируемость делает металлы особенно пригодными для высокопроизводительной, массовой и высокоточной обработки. Специальные технологические процессы позволяют получать детали такой формы, которая близка к заданной. Механическая обработка обычно применяется для изготовления компонентов из драгоценных металлов, а литье под давлением применяется в основном для изготовления деталей из неблагородных металлов. Кроме того, детали можно изготовлять либо из одного лишь материала, либо из материала с дополнительными покрытиями, например, с гальваническими покрытиями из золота и серебра, благодаря чему повышается коррозионная стойкость и улучшается внешний вид.
Металлы обладают более широким диапазоном свойств, чем любой другой класс конструкционных материалов, таких, как полимеры и древесина. К примеру, твердые стали обладают пределом прочности на растяжение свыше 250 т/кв. дюйм при комнатной температуре. Температуры плавления могут колебаться от -39 гр.ц. у ртути до 3410 гр.ц у вольфрама. Нержавеющие сплавы устойчивы к воздействию большинства химических веществ, за исключением самых сильных кислот, а золото, платина и родственные им металлы могут подвергнуться коррозии под действием химических веществ лишь в исключительных обстоятельствах. Способность металлических перьев сопротивляться атмосферной коррозии, а также воздействию самых разных сортов чернил чрезвычайно важна для производителей авторучек.
Ниже вкратце перечислены металлы, которые обычно используются для изготовления авторучек. В самом общем виде они делятся на две категории: неблагородные и благородные металлы. Детали из благородных металлов обладают коррозионной стойкостью в нормальных условиях эксплуатации, однако стоят особенно дорого.
НЕБЛАГОРОДНЫЕ МЕТАЛЛЫНЕРЖАВЕЮЩАЯ СТАЛЬ. Наиболее распространенный состав: 74 % железа, 18 % никеля и 8 % хрома. Она используется для изготовления большинства конструктивных элементов. Этот материал — твердый, достаточно пластичный, хорошо поддается таким видам обработки, как холодная прокатка, волочение, штамповка и обжатие. Нержавеющая сталь обладает высокой стойкостью к атмосферной коррозии; можно обрабатывать ее до получения привлекательной на вид поверхности — матовой, шершавой либо отполированной до зеркального блеска. Можно также нанести тонкое гальваническое покрытие из никеля, а поверх него — блестящее покрытие из хрома. Благодаря своей жесткости и коррозионной стойкости нержавеющая сталь используется для изготовления корпусов, крышек и перьев авторучек.
ЛАТУНЬ. Под термином «латунь» подразумевается обширное семейство сплавов, основанных на использовании различных вариантов системы «медь — цинк» и часто содержащих прочие металлические присадки, которые придают сплавам специфические свойства. Наиболее часто встречаются следующие составы: 60 % меди и 40 % цинка; 63 % меди и 37 % цинка; 709 % меди и 30 % цинка. Эти составы сочетают в себе адекватные механических свойства, легкость изготовления и стойкость к коррозии.
Покрытие поверхности вышеуказанных сплавов благородными металлами может осуществляться с применением процесса прокатки. Например, если используется золото, листки каратного золота можно прикреплять к бруску материала-подложки (вышеуказанного состава) при помощи пресса с роликовой подачей в условиях высокой температуры и высокого давления. Толщина и вес в каратах слоя золота регулируются в зависимости от технических требований. Например, если требуется, чтобы вес составлял 1/10 от 12 карат, используется золото 12К, и толщина покрытия регулируется с таким расчетом, чтобы вес слоя золота составлял 1/9 веса материала-подложки.
Готовый брусок прокатывают на прокатном стане, чтобы уменьшить его толщину. Промежуточные операции отжига выполняются на данном этапе для облегчения процесса упрочнения покрытия. Чистовая прокатка производится на зеркально отполированных роликах. Соотношение толщины золотого покрытия и материала-подложки остается неизменным в ходе операций прокатки.
ТИТАН. Этот металл относительно легок, его удельный вес составляет лишь 50 % удельного веса латуни или нержавеющей стали, однако он обладает чрезвычайно высокой стойкостью к коррозии. Вопрос об использовании титана рассматривался несколькими производителями авторучек, но им пришлось столкнуться с проблемами производственного характера, в основном из-за твердости титана. Считается, что титановые детали авторучек можно изготовлять из экструдированных трубных заготовок, и сплавы титана, различные по составу, подвергались испытаниям. Авторучка Titanium TI фирмы Parker выпускалась в течение лишь одного года (1970) по причине трудностей, связанных с обработкой титана. В настоящее время, используя более совершенную технологию, некоторые производители, в том числе фирмы Aurora, Faber-Castell, Lamy, Montblanc и Omas, выпускают авторучки, целиком изготовленные из титана.
АЛЮМИНИЙ. Чистый алюминий — мягкий металл, который не способен выдерживать давление, а потому легко деформируется. Вдобавок, алюминий недостаточно тверд, чтобы выдержать небрежное обращение, которому подвергается большинство принадлежностей для письма. Тем не менее он используется для изготовления деталей, которые не подвергаются регулярному износу. Путем сплавления алюминия с другими металлами можно получить ряд материалов, которые сохраняют общие для них характеристики легкости и долговечности, однако обладают и другими более высокими показателями: повышенной прочностью на растяжение и твердость, а также улучшенной обрабатываемостью.
БЛАГОРОДНЫЕ МЕТАЛЛЫСЕРЕБРО. Обычно в сплавах серебра используется стерлинговое серебро 925 пробы, остальное — легирующие элементы: медь, никель либо цинк, которые служат в качестве упрочняющих элементов. В прошлом использовалось серебро низкой пробы (800), однако с этой практикой покончено. В чистом виде серебро используется лишь в тех случаях, когда его наносят гальваническим способом на металл-подложку. Чистое серебро широко применяется для покрытия металла-подложки благодаря своей превосходной оптической отражательной способности, которая придает изделию привлекательный внешний вид. Сплавы серебра и палладия использовались для изготовления перьев, однако они не являются полноценными заменителями золота. Серебро очень хорошо полируется, но может потемнеть в атмосферах, содержащих соединения серы.
Стерлинговое серебро используется для изготовления деталей из сплошного серебра, в том числе корпусов и крышек. Важной характерной особенностью серебра является то, что на его поверхность можно наносить гравировку в технике «гильоше». Многие производители выпускают авторучки, целиком изготовленные из стерлингового серебра. Такие ручки не только красивее, чем посеребренные, но и будут дорожать со временем.
ЗОЛОТО. Этот самый старый драгоценный металл, известный людям, легко узнать по характерному желтому цвету и чрезвычайно высокой плотности. Мягкость чистого золота делает его непригодным в качестве материала для изготовления изделий. Золото можно сделать более твердым, добавив легирующие элементы — медь, никель, серебро или цинк. Изменения концентрации отдельных металлов в лигатурном сплаве влияют на внешний вид и характеристики золота. Например, цвет золота 18 карат колеблется от светло-желтого до розового и красного, в зависимости от легирующих присадок. Все сплавы золота обладают чрезвычайно высокой стойкостью к коррозии в воде и атмосферной коррозии; вот отчего они почти не тускнеют.
Существуют три основных типа промышленных сплавов, используемых при изготовлении авторучек:
Золото 9К (375 частей чистого золота на 1000 частей сплава). Это — самый твердый сплав золота, он же самый дешевый.
Золото 14К (585 частей чистого золота на 1000). Это — сплав средней стоимости, который ограниченно используется в большинстве стран континентальной Европы, но широко применяется в Великобритании и странах Северной Америки. Большинство золотых перьев изготовляется из золота 14К.
Золото 18К (750 частей на 1000). Хотя оно мягче, нежели оба вышеуказанных сплава, но все-таки достаточно твердое для того, чтобы использоваться при изготовлении авторучек и перьев из сплошного золота. Европейские производители изготовляют из золота 14К авторучки и перья на экспорт, однако в странах — членах Европейского Союза преобладает сплав золота 18К.
Белое золото — сплав, в котором лигатурами являются в основном серебро и палладий, наряду с несколькими другими незначительными добавками. Белое золото обычно изготовляется в варианте 18К, однако весьма экономно используется в промышленности.
ПОКРЫТИЯ ИЗ ЗОЛОТА. Большинство производителей использует уникальные свойства золота, даже если этот благородный металл присутствует лишь в качестве покрытия, нанесенного на металл-подложку. Это покрытие можно наносить с применением двух разных процессов: первый — при помощи процесса прокатки, о котором было сказано выше, второй — при помощи электролитического покрытия: деталь погружают в специальный золотосодержащий раствор, через который проходит электрический ток. Золото или заранее приготовленный сплав с высоким содержанием золота оседают на поверхности детали, которая служит электродом. Для нанесения гальванического покрытия обычно используются сплавы золота 18 или 23,5 карат. Детали корпуса авторучки можно покрывать с использованием обоих способов, но держатели обычно покрывают с применением гальванотехники.
ПРОЧИЕ БЛАГОРОДНЫЕ МЕТАЛЛЫ. Из благородных металлов, используемых для производства авторучек, группа, в которую входят платина, родий, иридий, осмий и палладий, обладает одинаковыми физическими, механическими и химическими свойствами. Все эти металлы — белого цвета, характеризуются высокой температурой плавления и обладают чрезвычайно высокой стойкостью к коррозии.
В чистом виде платина — мягкая, но быстро твердеет при добавлении небольшого количества легирующих присадок, и для производства изделий она используется в виде сплава с содержанием 950 частей на 1000. Поскольку платина — самый дорогой из всех благородных металлов, применяемых для изготовления ювелирных изделий, в том числе перьев, ее используют весьма экономно. Металл используется для изготовления самых престижных перьев; при этом перо становится двухцветным. Один из наилучших примеров — знаменитое перо авторучки Montblanc Masterpiece 149. Несколько производителей, включая фирму Montblanc, изготовляют перья из чистой платины, однако эти перья особенно дороги.
Родий и палладий используются в качестве электролитических покрытий. Они прочнее, чем серебряные покрытия.
Из всех известных на сегодня металлов, обладающих самой высокой плотностью и твердостью, осмий и палладий в основном используются для изготовления шариков, которые затем наваривают на кончик пера из благородного металла, разрезают по линии расщепа и шлифуют. Прочность этих металлов делают перья исключительно долговечными.
ДРЕВЕСИНАИзвестно около 70 000 различных древесных пород, из них около 400 имеются в продаже. Эти породы, как правило, используются в стране их происхождения, хотя некоторые экспортируются в промышленно развитые страны всего мира.
Степень жесткости у разных древесных пород различна, и принято считать, что лиственные породы дают более твердую древесину, чем, например, хвойные. Цвет древесины в основном зависит от содержания экстрактивных веществ, и древесина одних пород на свету бледнеет; а древесина других, напротив, темнеет, но большинство видов древесины приобретает более сочные цвета при полировке.
Естественный рисунок на разрезах древесины называется текстурой; он обусловлен взаимодействием таких природных факторов, как наличие пигментов, полос и крапинок, разница в плотности между клетками ранней и поздней древесины, направление волокон древесины, а также характер расположения годичных колец. Существуют восемь основных типов направления волокон по отношению к оси ствола, из которых наиболее часто встречаются прямослойность, при которой волокна направлены параллельно оси ствола (клен, черное дерево) и путаная свилеватость, при которой волокна расположены беспорядочно (эрика древовидная).
Способность клеток древесины отражать свет придает полированной поверхности блеск, и плотная древесина с тонкой структурой блестит ярче, нежели древесина с грубой структурой.
Для того, чтобы определить прочность и долговечность древесных пород, предназначенных для применения с конкретной целью, необходимо знать, каковы ее некоторые механические свойства, в том числе прочность на изгиб, жесткость или модуль упругости, ударная вязкость (способность поглощать энергию при ударной нагрузке). Сушка древесины играет чрезвычайно важную роль, ибо от нее зависит поведение древесины при использовании, и большинство видов древесины подвергают сушке до тех пор, пока влагосодержание не уменьшится до 12 % от массы. Удельный вес древесины определяется как отношение массы к объему; принято сравнивать удельный вес вещества с удельным весом воды, равным 1,0. Таким образом, удельный вес любой древесины дает четкое представление об ее массе, если известен объем.
При выборе древесины для изготовления авторучек следует учитывать не только цвет и рисунок поверхности, но и деформируемость древесины при использовании авторучки в различных условиях температуры и влажности. Поверхность не должна трескаться. После выдержки древесину распиливают на небольшие бруски, которые обычно имеют квадратное поперечное сечение. Эти бруски затем обрабатывают на токарном станке, придавая им требуемую форму и требуемый размер. Во многих случаях металлические либо иные вкладыши помещают в корпус и крышку авторучки. Поскольку древесина пориста, нанесение покрытия на поверхность необходимо не только для того, чтобы уменьшить поглощение влаги (особенно чернил), но и для сохранения природной красоты дерева.
Ниже приводится краткий перечень древесных пород, наиболее часто используемых ведущими производителями авторучек.
Эбеновое дерево (черное дерево). Древесина твердая, цвет — от темно-коричневого до черного, расположение волокон в основном прямослойное, текстура — тонкая, равномерная по окраске и рисунку. Древесина чрезвычайно тяжелая и плотная (удельный вес 1,09). Ее трудно высушивать и трудно обрабатывать, однако она прекрасно полируется. Превосходным примером авторучки, изготовленной из черного дерева, является модель OMAS 360 Wood.
Клен. Цвет древесины колеблется от кремового до розовато-коричневого. Древесина обычно прямослойная, текстура — тонкая, равномерная по окраске и рисунку. Удельный вес равен 0,69. Древесина клена медленно сохнет, степень деформируемости средняя. Типичный пример авторучки, изготовленной из японского клена, — модель Pilot FK Balanced.
Олива. Цвет этой древесины — от бледно-коричневого до коричневого, расположение волокон спиральное. Древесина обладает тонкой текстурой, равномерной по окраске и рисунку. Она довольно тяжелая (удельный вес 0,89), сохнет медленно, с тенденцией к растрескиванию от усушки и раскалыванию. Древесину можно окрашивать и полировать, однако при пользовании авторучкой может происходить деформация. Прекрасный пример авторучки, изготовленной из оливы — модель Man 100 фирмы Waterman.
Змеиное дерево. Это — южноамериканское дерево из рода Brosimum alicestrum; в Великобритании его называют буквенным деревом, а в США — леопардовым или пестрым. Цвет древесины красно-коричневый с черными вкраплениями или вертикальными полосами. Древесина очень твердая, прочная и тяжелая (удельный вес 1,30). Она с трудом поддается сушке на воздухе и обладает тенденцией к короблению. Несмотря на то, что древесину трудно обрабатывать, ее можно полировать до блеска с получением очень красивой поверхности. Степень деформируемости — средняя. Великолепным примером авторучки, изготовленной из змеиного дерева, является модель OMAS 360 Wood.
Палисандр. Цвет сердцевины ствола колеблется от сплошного ярко-красного до узора из желтых, оранжевых и красных прожилок. Древесина твердая и тяжелая (удельный вес 1,10). Сохнет очень медленно, деформация незначительна. Древесина легко окрашивается, ее можно отполировать с получением очень красивой поверхности. Фирма Omas изготовляет из этой древесины авторучки круглой и граненой формы.
Гваякум. Древесина гваякума — одна из самых твердых и тяжелых, с удельным весом 1,23. Цвет — от буро-зеленоватого до почти черного. Древесина маслянистая; степень деформируемости — средняя. Можно отполировать древесину с получением очень красивой поверхности. Коллекция авторучек фирмы Omas, изготовленная из экзотических пород деревьев в 1995 г., содержит авторучку, изготовленную из этого красивого материала.
Сандал индийский. Цвет древесины колеблется от светло-желтого до золотисто-коричневого и кирпично-красного. Древесина обладает характерным запахом. Удельный вес ее в среднем равен 0,66, в зависимости от страны происхождения. Древесина сохнет довольно медленно, зато очень мало деформируется. Ее можно окрашивать, и она прекрасно полируется. В коллекции авторучек фирмы Omas, выпуск которой начался в 1995 г., имеется экземпляр, изготовленный из сандала.
Эрика древовидная. Эта древесина наиболее часто используется для изготовления авторучек. Она чрезвычайно твердая, устойчива к воздействию тепла и к царапанию. В отличие от вышеперечисленных видов древесины, которые находятся в надземных частях деревьев, древесина эрики древовидной, используемая для изготовления авторучек (и многих других изделий), находится под землей. Цвет колеблется от белого с желтоватым или сероватым оттенком до оттенков коричневого и фиолетового. Древесина сохнет очень медленно, однако хорошо окрашивается и превосходно полируется. Фирмы Waterman, Sailor, Platinum и Omas принадлежат к числу производителей, изготовляющих авторучки из эрики древовидной.
ЛАКХотя большинство лакированных инструментов для письма изготовляется с использованием так называемого синтетического лака, существует гораздо более ценное совершенное и ровное покрытие, получаемое из китайского лака. Этот лак представляет собой древесный сок, обладающий одной особенностью: он затвердевает при соприкосновении с воздухом и образует идеально гладкую поверхность. Сырье получают из сока трех разновидностей деревьев, произрастающих в Восточной Азии: сумаха лаконосного Rhus verniciflua (Япония), сумаха последовательного Rhus succedanea (Китай) и лакового дерева Melossorreha lappifera (Кампучия). Когда лаковое дерево достигает возраста 8 — 12 лет, его сок собирают в кувшинчики, подвешенные под тонкими надрезами в коре. Свойства лака зависят от климатических условий и в особенности, от периода муссонов. Если сок собирают в годы с обильным выпадением осадков, лак будет эластичным, а если сок собран в относительно засушливые периоды, лак будет твердым, даже хрупким. Мягкий лак будет недостаточно прочен для использования в производстве авторучек, а хрупкий материал нелегко поддается полировке, и любой удар оставляет заметные следы на его поверхности.
Вот почему очень важно применять методы, которые позволяют смешиваь различные лаки и обеспечивают оптимальную вязкость. Двумя основными компонентами лака являются смола, которая придает эластичность, и урушиол — активный компонент, придающий лаку твердость. Урушиол — общее родовое название, которое относится также к цициолу и лакколу, в зависимости от породы деревьев, из которых получают сок.
Для того, чтобы при изготовлении авторучек создать поверхность наилучшего качества, лак следует наносить в несколько слоев, при строго контролируемых параметрах окружающего воздуха — температуре и влажности, пока затвердевает каждый слой. (Подобно вину, лак — это живое и непредсказуемое существо, и иногда смесь получается неудачной)
Чтобы преодолеть эти трудности, очень важно в точности знать оптимальные условия для каждого типа лака. Например, лак из Восточной Азии сохнет только при относительно высокой влажности воздуха (75 — 80 %) и при температуре 25 — 30 гр.ц. В наши дни такие фирмы, как S.T.Dupont, разработали методику регулирования температуры и влажности. (Не столь давно работа с лаком могла вызвать аллергическую реакция, но эту проблему удалось решить).
Азиатские мастера по лаку обычно работают с деревом. Между лаком и древесиной существует природное сродство, поскольку оба они принадлежат к одному и тому же семейству органических веществ, но гораздо труднее заставить лак сцепляться с металлом. Подробности процесса подготовки сырья, а также нанесения лака обычно окутаны чем-то вроде тайны, потому что этот процесс включает в себя не только глубокое знание старинных секретов ремесла, но и постоянный поиск мастером-лакировщиком новых рецептов лака и оригинальных вариантов отделок.
ИСТОЧНИКИ СЫРЬЯ И ПРИГОТОВЛЕНИЕ ЛАКАЛак, который использует фирма S.T. Dupont, собирают в Китае, затем, после первичной переработки в Японии, лак отправляют в деревянных бочонках во Францию, где по прибытии он подвергается проверке на качество. Пользуясь кистью, изготовленной из тончайшего волоса и прикрепленной к полоске бамбука, мастер наносит немного лака на стеклянную пластинку. Спустя два часа он уже точно знает, каково качество доставленного лака.
Последовательные стадии приготовления лака носят магические названия: процесс «наяси» — испарение влаги для получения сырого лака, который используется в грунтовках; процесс «курумэ» — получение чистого лака, используемого для заполнения пор и отделки поверхности.
Первую смесь приготовляют вручную при помощи шпателя в глиняном сосуде, примерно так же, как изготовляют самые знаменитые духи: мастер не знает в точности общую формулу, он просто знает точные количества нескольких компонентов покрытия, которые должен смешивать. Это — пигменты, придающие лаку его уникальные цвета: «синева полночного неба», «светлый черепаховый панцирь», «коромандельский красный» и т.д.
Затем лак фильтруют через кусок марли, подвешенный на деревянной раме и двух шнурках. Фильтрацию производят, попеременно закручивая и раскручивая шнурки, так что марля сжимается. Профильтрованный лак очень медленно, по каплям, стекает в глиняный сосуд, который тотчас же запечатывают смазанной жиром влажной бумагой. Ежедневно лак, приготовленный накануне, фильтруют, и каждый сосуд приобретает свою собственную родословную в виде этикетки, на которой указаны порядковый номер перемешивания, вес и дата. После этого лаки готовы для отправки в мастерскую, где воздух кондиционирован и обеспылен.
НАНЕСЕНИЕ ЛАКАПо традиции лак наносился исключительно кистью. После затвердевания каждый слой долго полировали вручную при помощи различных тонких абразивов, например, древесного угля. Некоторые украшения, вроде золотой пыли, следует наносить шпателем либо кистью, в соответствии с техникой нанесения порошка из авантюрина, которая применялась в Японии в конце XIX столетия.
Несмотря на то, что с тех пор методы были значительно усовершенствованы, нанесение лака на авторучку по-прежнему требует большого мастерства. Крышку или корпус, изготовленные из латуни, насаживают на стержень, который вращается над металлической пластинкой. Мастер должен обладать большим опытом, чтобы добавлять необходимое количество лака, которое он затем равномерно распределяет по всей поверхности авторучки, когда латунь соприкасается с пластинкой. Толщина слоя составляет около 70 микрон (0,07 мм). Процесс повторяется несколько раз, и, в зависимости от требуемого рисунка, наносятся до шести слоев лака.
При нанесении каждого слоя покрытия происходит затвердевание лака в результате естественной полимеризации (то есть изменения химического состава лака: молекулы смыкаются и образуют прочную трехмерную структуру). Для того, чтобы процесс проходил нормально, регулируются такие параметры микроклимата помещения, как содержание кислорода в воздухе, температура и влажность. Когда слой лака затвердеет, готовое изделие чрезвычайно осторожно полируют.
Существует обширное разнообразие отделок, в их числе — ровные цвета, узоры с использованием различных цветов и даже изысканные орнаменты с добавлением золотой пыли. Пожалуй, одним из самых привлекательных узоров является так называемая «яичная скорлупа». Фирма S.T. Dupont, вероятно, единственный производитель авторучек на Западе, которому удалось овладеть этой техникой.
Лак обладает естественным янтарным цветом, и обычно в него не требуется добавлять белые пигменты. Мельчайшие частицы яичной скорлупы укладывают вручную на первый слой лака, затем наносят покрытие для окончательной отделки. При последующей полировке яичная скорлупа вновь становится видимой. Этот особый метод изобрел во Франции в 20-х гг. Жан Дюнан (Jean Dunand), первый знаменитый французский мастер по лаку. Его ученик Георгий Новосильев (George Novosilleff) стал первым мастером по лаку, работавшим в фирме S.T. Dupont.
(в статье использованы материалы из книги Андреаса Ламброу «Перьевые ручки мира»)
Мини токарный станок по дереву своими руками | Лучшие самоделки своими руками
Любому мастеру время от времени доводится делать разные деревянные изделия, такие как ручки для инструментов или шкафчиков и прочие небольшие детали, без токарного станка при этом тяжело обойтись. Для таких простых работ и для обработки небольших деревянных деталей я решил сделать своими руками настольный мини токарный станок по дереву. Он действительно очень компактный и не будет занимать много места в мастерской или даже в квартире.
Мини токарный станок по дереву своими руками
Детали необходимые для создания мини токарного станка:
- Электродвигатель 895;
- Уголок-крепление для двигателя 895;
- Ось диаметром 8 мм и длиной 140 мм;
- Шкив для ремня GT2 на 36 зубьев и внутренним диаметром 8 мм;
- Шкив для ремня GT2 на 16 зубьев и внутренним диаметром 5 мм;
- Ремень GT2-122 мм и шириной 6 мм;
- Блок подушки подшипника двух видов;
- Модуль управления скоростью двигателя на 20А;
- Выключатель;
- Джек питания 5.5 DC;
- Оргстекло (акриловый лист) размерами 400х90х8 мм;
- Акриловый лист размерами 240х130х2 мм;
- Сверло с зенковкой 8мм;
- Болты М6 с ручкой;
- Болты М6;
- Импульсный БП на 24В и 17A.
Мини токарный станок по дереву своими руками
Процесс изготовления токарного станка по дереву:
Первым делом сделаем станину из оргстекла 400х90х8 мм, с помощью фрезера делаем в нём прорезь, а затем также делаем паз.
Мини токарный станок по дереву своими руками
Мини токарный станок по дереву своими руками
После этого просверливаем отверстия под уголок крепления двигателя, нарезаем резьбу и прикручиваем уголок. Нужно при этом учесть, что центр отверстия под двигатель должно быть соосно с прорезью который делали раньше фрезером, но если что отверстия в уголке позволяют подстроить в небольших пределах размещение скобы. После выравнивания затягиваем болты.
Мини токарный станок по дереву своими руками
Далее к уголку прикручиваем сам электродвигатель и надеваем на его вал шкив на 16 зубьев и затянув гужон на шкиве.
Мини токарный станок по дереву своими руками
Для того чтобы сделать корпус для двигателя и электроники токарного станка берём оргстекло (акриловый лист) 240х130х2 мм, размечаем и загибаем, для того чтобы это сделать нагреваем феном по размеченной линии, а затем взяв линейку, кладём её на линию, придавив её рукой, чтобы не двигалась. И теперь начинаем гнуть другой конец акрилового листа, стараемся браться поближе к линии, чтобы гнулось ровно по ней.
Мини токарный станок по дереву своими руками
Мини токарный станок по дереву своими руками
Для боковых стенок корпуса токарного станка будем использовать фанеру, кладём загнутый ранее корпус на фанеру и обрисовываем по его внутренней стороне на фанере. Вторую сторону делаем таким же способом и затем вырезаем их.
Мини токарный станок по дереву своими руками
Теперь берём ось, надеваем на него зубчатый шкив и затем надеваем ремень на два шкива, берём фанерную стенку и натягивая ремень отмечаем на стенке место где будет размешаться ось, она должна быть при этом над двигателем. Затем в этом месте в стенке сверлим отверстие.
Мини токарный станок по дереву своими руками
Также сверлим ещё два отверстия под винты блока подушки подшипника и прикручиваем затем его к стенке.
Мини токарный станок по дереву своими руками
С задней боковой стенкой корпуса делаем всё то же самое. Кроме того в ней нужно будет ещё наделать отверстий для охлаждения и одно отверстие под разъём питания.
Мини токарный станок по дереву своими руками
Далее я покрасил эти боковые стенки.
Мини токарный станок по дереву своими руками
Затем я зажал ось в шуруповёрт и заточил на наждаке её конец под конус.
Мини токарный станок по дереву своими руками
Далее начинаем собирать всю часть с двигателем токарного станка. Для этого я боковую крайнюю сторону привинтил к акриловой станине сбоку, просверлив перед этим два отверстия по сторонам.
Мини токарный станок по дереву своими руками
Вторую боковую сторону я закрепил шурупами снизу станины.
Мини токарный станок по дереву своими руками
Далее делаем проводку и подсоединяем к плате управления скоростью двигателя провода от двигателя, переменный резистор для управления скоростью, и подводим питание от разъёма питания через выключатель.
Мини токарный станок по дереву своими руками
В корпусе сверлим отверстия под выключатель и переменный резистор.
Мини токарный станок по дереву своими руками
Корпус прикручиваем спереди и сзади к станине четырьмя шурупами. Сзади я ещё дополнительно притянул шурупами к боковым фанерным стенкам.
Мини токарный станок по дереву своими руками
Берём 8 мм сверло с зенковкой, откручиваем гужон и снимаем часть которая предназначена для зенковки, она будет служить «патроном» для токарного станка по дереву. Прикручиваем его на ось.
Мини токарный станок по дереву своими руками
Из отрезков фанеры и небольшой досточки делаем заднюю бабку токарного станка. Все части я склеил между собой цианокрилатным клеем.
Мини токарный станок по дереву своими руками
Также я сделал подобным образом упор для резцов, вырезал нижнюю часть из фанеры, а сам упор из кусочка доски и склеил их вместе.
Мини токарный станок по дереву своими руками
К задней бабке я прикрутил блок подушки подшипника. Затем я покрасил эти две деревянные части токарного станка.
Мини токарный станок по дереву своими руками
Далее я взял латунную полосу и отрезал от неё два небольших отрезка, в одном по центру просверлил отверстие и нарезал резьбу М6 под зажимной винт с ручкой, а во втором сделал уже два отверстия и тоже нарезал резьбу.
Мини токарный станок по дереву своими руками
Эти две пластинки вставляем в паз внизу станины, первая с одним отверстием будет крепить к себе упор под резцы, а вторая с двумя отверстиями будет крепить к себе заднюю бабку. Первым винтом с обычной круглой шляпкой мы просто стягиваем бабку с пластиной но не полностью, чтобы бабка могла свободно ходить, а задним винтом с ручкой мы уже будем зажимать её во время установки деревянной заготовки в токарный станок по дереву.
Мини токарный станок по дереву своими руками
Берём болт М8, зажимаем его в шуруповёрте и также делаем на конце конус, так как мы делали с осью. После этого вставляем его в подшипник задней бабки и накручиваем на него гайку, помимо неё я позже добавил широкую шайбу с гужоном.
Мини токарный станок по дереву своими руками
Мини токарный станок по дереву своими руками
Теперь наш мини токарный станок по дереву сделанный своими руками полностью готов! Осталось только подключить к нему питание, зажать деревянную заготовку и начать вытачивать необходимые нам деревянные детали.
Мини токарный станок по дереву своими руками
Мини токарный станок по дереву своими руками
Мини токарный станок по дереву своими руками
Мини токарный станок по дереву своими руками
Игра «Шарик в лабиринте» своими руками
Главная » Все новости
26.06.2017
«Шарик в лабиринте» — игра с историей, она известна многим поколениям. Карманные варианты игры выпускаются разных видов и форм, стали популярны её компьютерные аналоги. На станке с ЧПУ тоже можно сделать лабиринт со стальным шариком внутри. Модель смотрится интересно, подойдет для подарка, а если постараться — то и на продажу.
Материалы и оборудование
Для изготовления основы лабиринта можно взять древесину толщиной 30-40 мм. Надо приготовить пропитку или масло для финишной обработки материала. Лист оргстекла (прозрачного пластика) будет закрывать игровое поле, чтобы стальные шарики не выпали.
В процессе работы на станке с ЧПУ мастер использовал:
1) фрезу для Т-образных пазов
2) фрезу концевую двухзаходную
3) фрезу сферическую
4) гравер составной
5) фрезу концевую однозаходную
Как выбрать узор для лабиринта?
Найти подходящее изображение можно в Google — поисковик предлагает массу вариантов. Нужный рисунок можно перенести в программу для создания модели лабиринта.
Как сделать игру?
1 этап – фрезерование
Сначала обозначают игровое поле (фреза 1), затем укрепляют его края (фреза 2).
Узор лабиринта вырезают сферической фрезой, она же выполняет отверстия под ручки и обрезает край всего изделия.
Гравёр наносит надписи – они показывают вход и выход из лабиринта.
Для вырезания оргстекла подойдет фреза 5. Размер заготовки равен площади игрового поля. В пластиковом покрытии лабиринта нужно сразу сделать отверстия под саморезы.
Обратите внимание, мастер укрепил пластик малярной лентой, чтобы не допустить раскола листа.
2 этап – обработка и сборка изделия
Основу игры шлифуют со всех сторон, покрывают древесным маслом.
После сушки в ходах лабиринта оставляют один или несколько стальных шариков, сверху прикручивают заготовку из оргстекла.
Игра готова! А вот еще фото лабиринтов для вдохновения:
Создание на станке с ЧПУ настольных, развивающих, развлекательных игр и игрушек – это целое направление в техническом творчестве. Посмотрите, как сделать своими руками «Морской бой», а мы и дальше будем знакомить вас с интересными идеями.
Источник: ToolsToday
Изделия на токарном станке своими руками
Изготовление изделий на токарном станке
Точение кубка При изготовлении кубка в патрон вколачивают деревянную болванку и навертывают его на шпиндель.
Болванку обтачивают и придают ей черновую форму кубка. Затем приступают к вытачиванию внутренней полости. Для этого ставят подручник поперек направляющих станины и продвигают его к торцу, а полукруглую стамеску поворачивают желобком книзу и, поставив ее слегка наискось, нажимают слева направо от центра вращения. Получается довольно глубокая впадина (углубление), которую окончательно растачивают выточками-крючками соответствующей формы. Вытачиваемые полости и отверстия проверяют нутромером. При точении надо следить, чтобы внутренняя выемка была гладкая, а стенки — равномерной толщины. После выточки внутренней полости выполняют наружную обработку кубка. Наиболее тонкие части изделия, такие, как ножка, обтачивают в конце работы. Точение вазы Общий принцип точения вазы такой же, как и точение кубка. Различие в том, что кубок точат целиком, а вазу частями. Сначала вытачивают колонку-ножку, затем верхнюю полую часть и наконец нижнюю — цоколь вазы. Выточив колонку на трезубце обычным путем, заготовляют кусок древесины и согласно рисунку вытачивают из него верхнюю часть, в центре которой центровым сверлом делают углубление для колонки и срезают ее, затем вытачивают цоколь, используя при точении чашечный патрон. В нижней части также делают углубление для нижнего конца ножки. Закончив точение отдельных частей, их собирают на клею. Когда клей просохнет, изделие отделывают на станке. Точение шкатулки Шкатулку собирают из трех частей: самой шкатулки, крышки и кнопки крышки. Сначала вытачивают крышку и в центре высверливают отверстие для кнопки, затем точат шкатулку и кнопку; причем внутреннюю часть крышки вытачивают окончательно, а наружную только вчерне. Крышку отрезают и приступают к вытачиванию самой шкатулки. На выточенную шкатулку надевают вчерне крышку и обтачивают ее сверху начисто. Готовые части склеивают, изделие просушивают и отделывают. Точение бочонка Для изготовления бочонка с крышкой применяют способ одноцентрового точения, то есть заготовку устанавливают консольно на шпинделе передней бабки. Заготовку обтачивают в цилиндр, затем обрабатывают ее свободный торец и делают в нем выточку согласно чертежу или образцу. Когда выточка сделана, край ее растачивают под фальц притвора. Диаметр выточки делают равным диаметру внутренней полости бочонка; диаметр фальца притвора должен быть равен половине толщины обработанной стенки бочонка. Высоту фальца делают в зависимости от величины бочонка. Обычно глубину фальца притвора делают 5—8 мм. Закончив обработку внутренней части крышки, выполняют приближенную обточку ее наружной поверхности, оставляя для доводки 1—2 мм. Затем крышку отрезают от заготовки и приступают к выточке внутренней полости, подрезав торец заготовки. Когда полость бочонка готова, обтачивают наружную поверхность, оставляя на доводку 1—2мм, и приступают к выточке фальца притвора на бочонке. Для этого от наружной кромки отмеряют высоту его, равную высоте фальца крышки, и острым углом прямой стамески делают подрез. Для обеспечения плотного притвора стенки фальцев бочонка и крышки должны быть цилиндрическими, а высота фальца бочонка должна быть ниже фальца крышки на 0,2—0,3 мм. Чтобы крышка надевалась на остов бочонка без задиров волокон, на наружной кромке его делают мелкую фаску. Затем насаживают крышку на остов бочонка и совместно доводят их наружные диаметры до нужных размеров. Незаметность притвора зачастую достигается тем, что на наружной поверхности бочонка делают проточки, имитирующие обручи. Изготовленный бочонок отрезают от заготовки. Для украшения бочонок часто делают из комбинированной древесины. Последовательность точения бочонка: выбор заготовки, вставка в патрон приточенного конца, округление,
отторцовка конца, разметка, внешняя обточка крышки (первичная), внутренняя выточка крышки, внешняя обточка крышки (вторичная) и ее срезка, отторцовка конца после срезки, обточка бочонка (первичная), внутренняя выточка бочонка, выточка фальцев, проточка фальцев по крышке, чистовая обточка бочонка вместе с крышкой, шлифовка шкуркой, покрытие лаком, отрезка бочонка от заготовки. Точение рюмки Последовательность точения рюмки Последовательность точения рюмки: а — вытачивание цилиндра по максимальному диаметру изделия, б— разметка и обтачивание внешней поверхности, в— растачивание внутренней полости, г— вытачивание ножки и основания, д — лакирование и отрезание изделия, е — готовые изделия Точение русской матрешки Вначале протачивают внешнюю сторону нижней части основания, затем внутреннюю полость, делают переход для надевания верхней части и отрезают заготовку. Верхнюю часть игрушки вначале вытачивают с внешней стороны. Затем растачивают внутреннюю полость, протачивают уступ по диаметру выточенной нижней части матрешки. Нижнюю часть игрушки надевают на верхнюю. После их подгонки на поверхности игрушки делают риску — отметку. Выточенная матрешка хорошо закрывается всегда только в одном положении. В собранном состоянии игрушку окончательно вытачивают, отделывают и грунтуют под последующее раскрашивание. При изготовлении семейства матрешек, вставляемых одна в другую, вначале вытачивают самую маленькую. В этом случае внутренние полости последующих матрешек вытачивают под размер предыдущей. Следует иметь в виду, что место разъема у всех матрешек данного семейства должно быть в одной плоскости. Защитно-декоративное покрытие токарных (точеных) изделий Простейшим способом отделки изделий является покрытие их с помощью тампона или кисти масляным или нитролаками, но предварительно необходимо хорошо отшлифовать шкуркой и загрунтовать порозаполнителем КФ (для древесины светлых пород) и КФ-3 (для древесины красного дерева и др.). Лучший результат нанесения лака достигается пульверизатором или способом окунания в него точеного изделия. При покрытии нитролаком первый слой просушивается 15—20 мин, затем шлифуется пастой или мелкозернистой шкуркой. После этого наносится второй и последующие слои лака. При необходимости выточенные изделия перед лакированием покрывают морилкой, имитирующей ценные породы. На мореной поверхности хорошо смотрятся вырезанные резцами (штихелями) узоры или проточенные на станке канавки, углубления, полоски. Красиво смотрятся изделия, отделанные выжиганием и обжиганием. Кроме обычной иглы электровыжигательного аппарата часто применяются различные формочки (крючки) из проволоки, штемпеля. Различные узоры можно сделать спиралью, насаженной на жало паяльника. Нередко выжиганием получают контурный рисунок для последующего раскрашивания. Контур препятствует растеканию краски.
Рисунок для выжигания можно выполнить на бумаге, затем проколоть по контуру иглой. Бумагу или кальку с отверстиями накладывают на изделие и припудривают тампоном толченым углем. Когда шаблон снимают, на изделии остается контурный рисунок, который можно раскрасить акварелью и покрыть лаком. Для раскраски можно использовать гуашь, но, чтобы не пачкалась и не текла при раскрашивании, в нее добавляют немного жидкого столярного клея или водоэмульсионной краски. Краска немного обесцвечивает тона. Яркими выглядят изделия, раскрашенные анилиновыми красками. Они разводятся в воде и наносятся кистью. Изделие перед этим обязательно грунтуется. В качестве грунта можно использовать клейстер, который наносится тампоном или губкой. Грунтовка проводится два-три раза с интервалами на просушку в 10 ч. Окрашивать точеные изделия можно и масляными красками, но в этом случае применяется грунт, состоящий из одной части желатина (столярного клея) и пяти частей зубного порошка. Ручки, рукоятки, веретена и другие изделия после обработки шлифовальной шкуркой окунаются в лак ПФ-283 (бывший 4С) и сушатся в течение 24 ч. Затем по лакированной поверхности наносятся черной тушью рисунки, надписи перьевой ручкой. Рисунки раскрашиваются цветной тушью. После этого изделия снова окунаются в тот же лак и сушатся в подвешенном положении.
Изделия на токарном станке
Токарные станки предназначены для выпиливания (точения) заготовок из дерева в виде вращающихся тел. Выполняют на таких механизмах обточку и расточку поверхностей цилиндрической, конической и фасонной
формы. Для изготовления различных предметов и заготовок используют нарезание четкой резьбы, обработку и подрезку торцов, сверление, а также зенкерование и развертывание отверстий разной величины. Любой токарный станок по дереву состоит из передней бабки с патроном, шпинделем и ступенчатым приводом, станины, задней бабки с центром для поддержания обрабатываемой детали и удобного подручника, который служит опорой для резцов во время работы. Задняя бабка с подручником могут легко передвигаться вдоль по станине, в нужных местах прочно закрепляясь специальными установочными болтами. Будущее изделие устанавливается и зажимается в патроне. В его качестве используются трезубцы, корончатые и поводковые патроны, планшайбы, патроны-рюмки. Изделия на токарном станкеДля производства применяется сухая древесина без сучков различных пород, но с однородным строением, такая как береза, бук, граб, груша, липа, яблоня, осина, клен. Тогда изделия на токарном станке будут отличаться прекрасным внешним видом и долгим сроком службы. Точеные детали очень часто входят в состав столярных предметов: это многочисленные колонки, пилястры, столешницы, мебельные ножки, подвесные полки, розетки. Различные вырезанные украшения из дерева пользуются высокой популярностью благодаря их красоте и традиционной направленности, несущей теплоту и уют дому. Получаемая гладкая обточенная поверхность позволяет выполнять многие предметы искусства. Например, специалист способен выточить изящный кубок или вазу, а также разнофактурный бочонок и шкатулку. Для изготовителей сувенирной продукции важно овладение выполнением русской матрешки, деревянных рюмок, стопок и графинчиков. После точения поверхности отшлифовываются и обрабатываются масляными или нитролаками, после чего предметы раскрашиваются акварелью, гуашью либо анилиновыми красками. Это придает им блестящий яркий внешний вид и разнообразие цветовых оттенков. Профессиональные токари способны выполнить изделия на токарном станке любой сложности от мелких виртуозных фигурок и шахмат до крупных форматов по эскизам заказчика. Деревянные игрушки, токарные вазы, миски и прочая посуда пользуются широкой известностью как в нашей стране, так и за рубежом. А древесная порода с красивой текстурой, такая как дуб, грецкий орех, красное дерево, можжевельник, сосна, кедр отлично подходит для декоративных изделий. https://www.youtube.com/watch?v=27wkmYg7TTQ
Отделка заготовки
Данный метод используется для обработки элементов цилиндрической формы разнообразной длины, зафиксированной между центрами задней и передней бабок. Соответственно, вы имеете возможность изготовить любые детали: от стоек перил и ножек стола до крохотных шахматных фигурок. В особенности у искусных мастеров получается изготовление и обтачивание бильярдных киев.
Первый этап работы состоит в определении расположения оси заготовки из дерева, чтобы зажать ее между центром задней бабки и поводковым центром.
Второй этап заключается в том, чтобы изготовить заготовку (из обрезки полена или бруска дерева квадратного сечения). Это может производиться в режиме 1000−1500 оборотов в минуту. В этом случае стружка должна сниматься справа налево посредством желобчатой вогнутой широкой стамески для предварительной обработки рейера. Если заготовка длинноватая, то черновая обработка осуществляется в несколько шагов; подручник при этом придвигается к детали по мере ее отделки, не меняя положения по высоте.
Читать также: Как выглядит молочный гриб
При точении деталей бывают инструменты различной формы для обработки фасонной поверхности:
- крючок,
- полукруглый резец,
- плоская стамеска,
- скошенная стамеска (или в народе — косяк),
- желобчатая стамеска и др.
В зависимости от разновидности применяемого инструмента и стадии рабочего процесса необходимо время от времени приближать подручник к заготовке. По окончании процесса, когда деталь будет уже готова, осуществляется финальная отделка:
- полирование,
- тонирование,
- шлифование,
- вощение и проч.
Последние штрихи происходят, когда подручник уже снят.
Художественная обработка дерева
Точение
Изделия из древесины не так уж часто встречаются при археологических раскопках. Но. бывают и счастливые исключения. Благодаря повышенной влажности почва новгородской земли как бы законсервировала и донесла до нас множество различных деревянных вещей. Правда, в большинстве случаев это не целые изделия, а отдельные части, но и небольшие фрагменты дали ученым возможность реконструировать точеную деревянную посуду — всевозможные братины, чаши, кубки, миски, ставцы, блюда, солонки. В старину в братины наливали различные напитки, которые подавали на стол по особо торжественным случаям. Блюда предназначались для пирогов и сладостей, а чаши и миски — для иных угощений. В ставцах — сосудах с крышками — хранили хлеб, а для соли вытачивали устойчивые солонки. Древние токари, хотя и работали на примитивных станках с лучковой передачей, применяли наиболее сложную и трудоемкую технологию изготовления токарных сосудов. Новгородские древоделы точили посуду не с торца, а поперек волокон. Этот способ точения делал посуду прочнее и наиболее полно выявлял декоративные свойства древесины. Вначале мастер делал заготовку. Он раскалывал кряж, высота и толщина которого должны были быть одинаковыми. Топором обтесывал половину кряжй, придавая заготовке приближенно форму усеченного конуса или полушара. Затем заготовку укрепляли на токарном станке и обрабатывали. На готовом изделии древесные волокна образовывали неповторимый рисунок. Даже древесина ольхи, маловыразительная при торцевом точении, обнаруживала интересный текстурный рисунок, а древесина ясеня и клена приобретала переливчатый шелковистый блеск. Современные станки’, которые есть и во многих кружках технического творчества, и в школьных мастерских, дают возможность точить древесину любой породы, выбор которой зависит от ее физических и механических свойств и назначения изделия. Физические свойства — это блеск, цвет, текстура и влажность древесины. Механические — прочность, упругость, пластичность. Из дуба; грецкого ореха, можжевельника, красного дерева, сосны, кедра, имеющих красивую текстуру, точат в основном декоративные изделия, которые не раскрашивают, а лишь покрывают прозрачным лаком. Природная красота такой древесины — лучшее украшение токарной работы. Из липы, осины, ольхи, березы вытачивают изделия, которые затем раскрашивают гуашью, темперой, масляными и анилиновыми красками. На современных деревообрабатывающих предприятиях для вытачивания большого количества одинаковых деталей применяют токарные автоматы и полуавтоматы. Художественные декоративные изделия и посуду вытачивают только на ручных станках. Обрабатывать лучше хорошо высушенную древесину, которая при полировке не дает ворса. Длинномерные детали точат на токарном станке с задней бабкой, а небольшие изделия — на станке с трубчатым патроном, в котором деталь закрепляют только с одной стороны. Это дает возможность со свободного торца выбирать полые объемы. Тарелки или чаши с большим диаметром удобно точить на планшайбе — металлическом диске, с отверстиями под шурупы, которыми деревянную заготовку плотно прикрепляют к диску. На стационарных станках применяется планшайба со специальными зажимами. На всех ручных станках древесину обрабатывают несложными ручными резцами. Для грубой черновой обработки заготовки, для придания ей цилиндрической формы применяют полукруглые резцы. Плоские резцы, называемые косяками, применяются для чистого точения внешней поверхности изделия. Эти резцы нетрудно изготовить из обыкновенных стамесок или из плоских напильников, сточив с них насечку. Для обработки внутренних поверхностей издавна применяли резцы с крючковидными лезвиями. Токари называют их просто крючками. Полукруглые и крюч-ковидные резцы можно выковать из углеродистой стали. Если изготовить такие резцы разных размеров, ими можно будет обрабатывать внутреннюю поверхность различной величины и конфигурации. Многие токари работают резцами, которые представляют собой металлическое кольцо, приваренное к прутку. Более распространено точение древесины с торца, чем поперек волокон. Для такого точения применяют бруски с квадратным сечением. Топором обтесывают брусок, стараясь придать ему как можно более правильную цилиндрическую форму. Обтесанную заготовку забивают в трубчатый патрон, установив ее строго горизонтально. Включив станок, берут широкий полукруглый резец. Рукоятку резца держат в правой руке, а левой прижимают металлическую часть резца к подручнику. Резец держат под углом примерно 15—30° к оси вращения заготовки. Осторожным касанием лезвия снимают стружку. Резец проводят несколько раз вдоль всей длины заготовки до тех пор, пока она не приобретет строго цилиндрическую форму. При изготовлении полого изделия, например карандашницы, в первую очередь вытачивают полость крючковидными резцами или кольцами. При этом подручник станка разворачивают в сторону торцевой
поверхности цилиндра. Выбрав полость, приступают к проработке внешних форм. Предварительно плоским резцом делают разметку, наносят на поверхность цилиндра кончиком резца неглубокие, но отчетливо видимые риски. Если работают по эскизу, то разметку делают штангенциркулем, им же во время точения контролируют толщину изделия. Ориентируясь на риски, плоским резцом снимают стружку серединой лезвия или же его нижней частью — пяткой. Вначале вытачивают обобщенную форму изделия, а затем прорабатывают отдельные детали. Не выключая станка, токарное изделие шлифуют и полируют. Сперва шлифуют наждачной бумагой с крупным абразивным покрытием, затем с мелким. Полировать, или, как говорят мастера, лощить, древесину можно древесной стружкой или сухим хвощом, который продается в аптеке. Хорошо полируется древесина конским волосом. Исстари древесину лощили также мочалом или лубом, оттого и операцию лощения иногда называли лублением. Здесь же, на станке, изделие можно покрыть лаком или восковой мастикой, которые наносят на поверхность тампоном. Закончив отделку, изделие торцуют и подрезают. Освоив технику точения с торца, можно попробовать свои силы в более сложной технике точения — поперек волокон. Современные мастера и сейчас нередко применяют этот способ, так широко распространенный в древности. Как правило, они ставят перед собой чисто декоративные задачи, изготовляя, например, настенные тарелки из древесины хвойных деревьев. Причем лучшим материалом считаются доски-половицы, которые всегда можно достать, так как сейчас сносится много старых домов, особенно в районах массовой застройки больших городов. Сосновые половицы от времени приобретают насыщенный золотисто-коричневый цвет, делающий излишним тонирование древесины. К тому же можно быть уверенным, что декоративная тарелка, изготовленная из такого материала, не треснет и не покоробится. Вместо половиц можно использовать и любые другие сосновные доски, только хорошо высушенные. Интересный декоративный эффект можно получить, если применить для точения клееные блоки. Несколько дощечек склеивают так, чтобы слои каждой последующей дощечки шли поперек слоев предыдущей, так же как склеивают листы шпона при изготовлении фанеры. Если склеить несколько трехгранных призм, как показано на рисунке, то из такой заготовки можно выточить сосуд, имитирующий бондарное изделие. Для изготовления клееных блоков нужно подбирать древесину с ярко выраженной текстурой и интенсивным цветом. Деревянные токарные формы издавна были в ходу у мастеров-игрушечников. А забавная матрешка, выполненная резцом токаря, стала общепризнанным национальным русским сувениром. Казалось бы, при конструировании токарных игрушек возможности мастера очень ограничены, так как в распоряжении его имеются лишь тела вращения. Но из семи объемных геометрических тел, которые лежат в основе всех предметов, четыре — шар, цилиндр, конус и тор — тела вращения. Вглядитесь в окружающие нас предметы. Многие из них состоят из тел вращения. Ствол дерева, кастрюля, карандаш имеют форму цилиндра, футбольный мяч и яблоко — шара. Коническую форму могут иметь ножка стула, плафон, ведро. Баранка имеет форму тора. Но токарные игрушки чаще всего изображают человека и животных. Конечно, все эти фигурки очень условны, но именно эта условность и придает своеобразную выразительность. Как же работать над токарной игрушкой? Прежде всего разработайте эскиз. В эскизе необходимо решить многое: продумать конструкцию всей игрушки, учитывая пластические возможности токарной обработки, найти рисунок росписи. По эскизу составьте чертеж, на котором точно укажите размеры и конфигурацию всех деталей игрушки. Лучший материал для вытачивания игрушек — древесина липы, осины и ольхи. Она мягкая, легкая, с однородным строением и окраской. Мелкие вещицы иногда делают из березы. Плотная и твердая древесина березы позволяет вытачивать детали величиной со спичечную головку. Древесина лиственных пород хорошо окрашивается различными красителями. Поэтому из нее в большинстве случаев делают крашеные игрушки, часто сочетая раскраску с выжиганием. Оригинальные токарные игрушки можно сделать из древесины хвойных пород. Такие игрушки не обязательно раскрашивать — лучше выявить и подчеркнуть естественный рисунок древесины. Для этого детали перед сборкой обрабатывают морилкой. Готовые детали игрушек соединяют столярным клеем, клеем БФ-2 или латексом. В местах соединения предварительно сверлят отверстия для соединительных штырей. Собранной игрушке дают высохнуть, а затем приступают к раскраске. Прежде чем применить те или иные красители, нужно определить назначение изделия. Декоративную токарную работу, которая будет стоять на столе или висеть на стене и только от случая к случаю попадать в руки, можно смело расписывать темперой или даже гуашью. Ни темпера, ни гуашь не требуют предварительной грунтовки. Игрушки, расписанные темперой, имеют приятную бархатистую фактуру. Темпера прочно держится на древесине, поэтому ее не обязательно покрывать защитным слоем лака. А вот игрушки, расписанные гуашью, нужно покрыть двумя-тремя слоями прозрачного лака. Можно применять масляный лак 4С или нитролак НЦ-222. Лак на фигурки наносят кистью или тампоном. Правда, этим способом трудно добиться равномерного распределения лака на поверхности древесины, поэтому лучше применить более эффективный способ .е стекут излишки лака. После подсыхания первого слоя тем же способом нанесите второй. Способом окунки можно не только лакировать, но и окрашивать детали игрушек в жидких растворах красок. Если вы задумали расписать игрушку масляными красками, ее нужно предварительно загрунтовать. Грунтовка не дает краске пожухнуть и сохраняет ее характерный блеск. Для приготовления грунтовки разведите в стакане воды одну чайную ложку желатина в пять ложек зубного порошка. Вместо желатина можно использовать столярный или рыбий клей. Грунт наносится на поверхность древесины два-три раза и хорошо просушивается. Детали игрушек, выточенные из мягкой древесины хвойных пород — сосны, ели или кедра, можно декорировать обжигом. Под действием огня более мягкие и рыхлые летние участки годичных слоев обугливаются значительно быстрее, чем более плотные осенние. При этом текстура более контрастно появляется на поверхности древесины. Обжигать древесину нужно постепенно, слегка касаясь ее поверхности пламенем паяльной лампы или газовой горелки. Чтобы получился темно-коричневый тон, вначале опалите древесину до появления светло-коричневого цвета. После вторичной обработки поверхность древесины станет еще темнее, а контраст между годичными слоями усилится. Так поступают до тех пор, пока не будет получена нужная тональность. Декорированные обжигом детали покройте прозрачным лаком. Работая с огнем, не забывайте строго соблюдать необходимые меры противопожарной безопасности. Выточенные на токарном станке различные детали можно с успехом использовать в оформлении школьного интерьера. В последние годы для оформления интерьеров все чаще стали использовать дерево. Этот естественный материал оживляет холодные железобетонные стены, придает интерьеру особую теплоту и уют. Дерево словно излучает солнечные лучи, которые оно впитывало на протяжении всей своей жизни. Особенно хорошо вписываются в современный интерьер деревянные резные рельефы. Но техника резьбы довольно трудоемка. И конечно, начинающим мастерам выполнить панно больших размеров в этой технике практически невозможно. Значительно проще выполняется панно в технике наборного рельефа, имеющей более простые технические решения по сравнению с резьбой. В то же время наборный рельеф всегда отличается высокой декоративной выразительностью и неповторимым своеобразием. Достоинство этого способа и в том, что в работе над рельефом может принять участие большой коллектив ребят. И не только юные художники, но и те ребята, которые умеют строгать, пилить, точить на токарном станке. Оформлять помещение начните с разработки эскиза. Рисунок эскиза должен отражать характер того помещения, где будет размещено панно. Если, например, вы оформляете кабинет биологии, то используйте для панно условные изображения растений и животных, если же кабинет физики — приборов и механизмов. Четко представляя себе содержание будущего панно, набросайте на листке бумаги эскиз. Поищите композицию — правильное размещение всех изобразительных элементов на листе. Затем по рисунку эскиза вычертите на бумаге чертеж-эскиз в натуральную величину. Это можно сделать на обратной стороне обоев. На чертеже определите, какие формы вам -лучше использовать: токарные или столярные. И только после этого вычертите рабочие чертежи всех деталей, из которых будет складываться панно. Необходимо также подсчитать и указать на каждом рабочем чертеже количество деталей той или иной конфигурации. Работая над эскизом и чертежами входящих в панно деталей, помните, что язык наборного рельефа должен быть немногословным и передавать предметы окружающего нас мира в условной манере. Основу панно составляет деревянный щит. Он сколачивается из ровных гладких досок, хорошо обструганных и зачищенных наждачной бумагой. Прежде чем сколачивать доски в щит, сложите их вместе лицевой стороной вверх и переведите на них контуры рисунка с чертежа-эскиза. Теперь при сколачивании щита вы сможете вбить гвозди там, где их шляпки будут прикрыты деревянными деталями. Вбивая гвозди, утопите их шляпки. Имея рабочие чертежи деталей, выточите одни из них на токарном станке, другие сделайте столярными инструментами. Наиболее эффектно в наборном рельефе смотрится древесина хвойных пород: лиственницы, ели и сосны. Она имеет красивую и четко выявленную текстуру, которая придает ей особую декоративность. Другое неоценимое достоинство древесины хвойных пород заключается в том, что через несколько месяцев она «загорает» — под влиянием света и солнечных лучей приобретает глубокий золотисто-янтарный оттенок. Это, конечно, не значит, что во всех случаях нужно стремиться применять древесину только хвойных пород. Необходимо учитывать назначение каждой отдельной детали. Например, для лица человека лучше взять древесину лиственных пород: осины, липы, тополя, ольхи или березы, имеющих мало выраженный текстурный рисунок. У всех этих пород, кроме ольхи, светлая окраска. Для передачи загорелого тела хорошо использовать светло-коричневую древесину ольхи. Каждую токарную заготовку распилите на две части и по их высоте заготовьте столярные детали. Это нужно для того, чтобы все детали выступали над фоном примерно на одну и ту же высоту. Затем все детали аккуратно зачистите наждачной бумагой, за исключением тех поверхностей, которыми они будут приклеиваться к щиту. Разложив все детали на щите, проверьте правильность построения композиции. Ведь изображение, воплощенное в материале, отличается от того, которое было нарисовано на бумаге, даже если точно соблюдены размеры и конфигурация всех деталей. Это и понятно: на эскизе мы видим плоское изображение в отличие от объемного в натуре. Возможно, что, после того как вы разложите детали, вам что-то не понравится и вы захотите одни детали заменить другими, какие-то передвинуть, то есть внести коррективы, которые трудно было предвидеть в эскизе. Когда композиция вас полностью удовлетворит, можете смело приступать к наклейке деталей на щит. Серьезно отнеситесь к выбору клея. Выбирайте его с учетом того места, где будет висеть панно. Если близко от него будут находится печь или батареи центрального отопления, то вам понадобится термостойкий клей, а для сырого помещения -влагостойкий. Высокой термо- и влагостойкостью обладают универсальный клей (БФ-2, БФ-4) и нитроклей. Удобен для наклеивания деталей латексный клей. Когда клей высохнет, обработайте панно наждачной бумагой —удалите пятна клея и следы карандаша. А затем покройте древесину тонким слоем бесцветной мастики, например «Самоблеском», «Силиконовой», «Зеркальной». Способ применения мастик указан на упаковке. Размещая панно на стене, постарайтесь, чтобы свет падал сбоку. Боковое освещение сделает его наиболее выразительным, выгодно подчеркнет рельеф. https://make-1.ru/1s/4_derevo_39.php https://100fondue.ru/razda/tokarnie-stanki/50_izdeliya_na_tokarnom_stanke… https://www.bibliotekar.ru/krasota/9.htm
Широкий выбор форм и моделей
Занимаясь обработкой древестных заготовок профессионально, важно грамотно подбирать соответствующий инструмент для токарных работ по дереву. Богатый выбор и объемные наборы с разноплановыми наконечниками позволят охватить значительную часть работ.
Исходя из функциональности, стамески по дереву принято делить на такие группы:
- Грубая обдирка. Инструмент обладает парой рабочих граней, сопрягающихся под острым углом. Считается, что данная конструкция является существенно безопасней, чем радиусные аналоги.
Рейер для грубой черновой зачистки
- Чистовое точение. Подобные виды резцов для токарного станка по дереву снимают незначительный слой стружки и предназначены не для придания заготовке формы, а назначение их в придании внешней гладкости наружной поверхности. Металлические наконечники выпускаются с левой или правой заточкой.
Инструмент для чистовой зачистки
- Фасонный резец по дереву на рабочей части обладает полукруглой режущей частью. Их задействуют для работы с нестандартными поверхностями.
Фасонный может иметь практически любую конфигурацию
- Отрезной резец. Он актуальны сейчас для одной операции, в которой требуется от заготовки отделить какую-то часть.
Отрезной шириной 10 мм
- Расточные. С помощью таких изделий убираются излишки материала, появившиеся в процессе обработки. В такой операции помогает спецуступ, расположенный в области резания.
Расточной для удаления излишков древесины
- Токарные резцы по дереву с круглым сечением. Они используются для обработки радиусных заготовок. Рабочая часть бывает как радиусной, так и с небольшими технологическими зубцами.
Рейер для точения чаш
- Токарные работы по дереву в торце проводятся при помощи обычного режущего напильника.
- В качестве вспомогательного оборудования применяют специальные ограничители на резцы, лимитирующие глубину резания.
Помимо стандартного набора профессионалы используют в работе самодельные резцы для токарного станка по дереву. Такой подход обеспечивает увеличение производительности и помогает расширить ассортимент готовой продукции.
Если предполагается длительное время заниматься обработкой древесины, то в таком случае не обойтись без качественного инструмента, который изготавливается из стали инструментального класса. Она способна выдерживать большую производственную интенсивность, которая не всегда по силам самоделкам.
Самодельные токарные резцы по дереву
Наибольшую трудность в производстве каждого типа стамески для токарного станка вызывает подбор заготовок для режущей части. Кроме обеспечения соответствующей твердости приходится задумываться о возможности установки металлической части в державку. Она позволит зафиксировать резец в нужном положении для комфортной обработки.
Наиболее приемлемым материалом для самодельных резцов является инструментальная сталь (У8, У10, У12 и пр.). При этом стоит учесть, что она окажется проблематичной для обработки в гаражных или домашних условиях. Это связано с высокой первоначальной твердостью материала.
Традиционной практикой является изготовление под токарный станок резцов из углеродистой марки стали с последующей ее закалкой. Самостоятельно инструмент изготавливают из следующего сырья:
- Арматура или пруты стали. Предпочтительней подбирать заготовки с максимально приближенными геометрическими параметрами к будущим режущим формам.
- Напильник либо рашпиль. Ножи для домашнего использования переделывают из б/у напильников, потерявших свой первоначальный вид и режущие способности. Важно проверить заготовку на отсутствие трещин и сильных сколов, чтобы получить качественный продукт.
- Куски рессор от автомобилей. Такая сталь проблематично обрабатывается без предварительного нагрева и придания максимально близкой формы. Для этой операции используют автоген или сварочный аппарат.
Хорошей альтернативой является изготовление базового токарного корпуса, в котором удастся менять резцы. Однако, подобная ситуация требует наличия монтажных элементов в конструкции готового изделия. В процессе работы они обязаны держать значительную нагрузку и не менять первоначального положения режущей части.
В качестве заготовок могут быть использованы рашпили или напильники, уже отслужившие свой срок
Когда заготовку согнули до требуемой формы, необходимо провести предварительную заточку кромки. На следующем этапе рабочая часть подвергается закаливанию. Это делается с помощью разогревания острия на отрытом огне, например газовой горелкой или в кузнечном горне. Далее обеспечиваем резкое охлаждение в большом объеме машинного масла.
Высоколегированные и высокоуглеродистые стали не стоит калить в воде, так как внутренние напряжения материала приведут к появлению трещин, хрупкости и выходу из строя заготовки.
Самостоятельно изготовленное вспомогательное режущее оборудование по дереву для токарного станка рекомендуется проверять на мягкой древесине. Это поможет избежать возможных негативных последствий с ним. После непродолжительного тестирования нужно проверить сохранность первоначальной заточки и формы инструмента.
ВИДЕО: Как сделать рейер своими руками (грубая очистка)
ВИДЕО: Мейсель своими руками (чистовая обработка)
Заточка рабочего инструмента
Каждая рабочая стамеска должна быть хорошо заточена. В противном случае она не даст нужной чистоты поверхности или станет создавать сколы в деревянных заготовках. Заточка токарных резцов по дереву требуется в нескольких случаях: после покупки (не все производители продают свои резцы в заточенном виде) и после затупления кромки (придается первоначальный вид инструменту). Вернуть кромке необходимую остроту удастся с помощью определенных операций.
Для заточки используется станок, шлифмашина или напильник
В первую очередь для правильной заточки необходимо запастись несколькими типами заточных камней. Более грубый с крупным зерном будет обдирочным, а абразивный инструмент с мелким зерном является доводочным.
Если имеется такой фиксатор для абразива как башмак, то оснастка крепится в нем под требуемым углом. Далее по поверхности водим резец из стороны в сторону.
Использовать для заточки исключительно крупное зерно – непрактично, так как оно не даст нужной остроты. Все время точить мелким зерном также неправильно, ведь камень будет забиваться стружкой, а металл станет подгорать и терять свою твердость от повышения температуры, что приведет к быстрому затуплению. Можно воспользоваться средним зерном из интервала 25-40 с твердостью СМ-1.
Читать также: Салат из авокадо с креветками и помидорами
Нередко профессионалы практикуют заточку своими руками в несколько этапов. Сначала обдирочные операции, потом доводочные также на станке. Финишная стадия осуществляется на заточном бруске – оселке. Их можно смазывать машинным маслом, чтобы минимизировать нагрев заготовки.
Хранение проводится в сухом месте, так как данный инструмент не переносит влаги. После каждого сеанса применения необходимо очистить каждый резец от остатков стружки, смол или иных типов загрязнения.
ВИДЕО: Как правильно затачивать инструмент
Работа на токарном станке по дереву, в принципе, несложная, но требует навыка и умения «чувствовать» обрабатываемую деталь. Именно тогда она становится настоящим искусством, в котором находят свое выражение воображение и творчество.
Токарный станок по дереву имеет одну ограниченную функцию: он только вращает деревянную заготовку. Столяр же из простого куска дерева постепенно вытачивает законченный предмет: ножки для мебели, корпус лампы, стойки перил, игрушки, коробочки, кубки, салатницы, вазы и т. д.
В отличие от прочих машин для обработки дерева, использующихся лишь на тех или иных промежуточных стадиях, токарный станок годится для всех операций – от черновой обработки до полирования. Требуемый инструмент – это желобчатые (цилиндрические или в форме буквы «V») и плоские стамески, резцы, скребки различных размеров и форм. Станок вращает заготовку, а рука контролирует движение резца. В зависимости от того, какой предмет надо изготовить, существует два способа крепления заготовки. В первом случае деревянная деталь зажимается горизонтально между центрами передней и задней бабок. Второй способ предусматривает установку заготовки исключительно в передней бабке с помощью патрона или планшайбы. Если вы новичок в работе на этом станке, будет логично начинать с первого способа.
Токарный станок с электронным регулированием
Принцип действия
Весь механизм станка укреплен на станине, сделанной из двух стальных брусьев или из профильных чугунных либо алюминиевых балок. С одной стороны станины располагается передняя бабка, внутри которой размещен электрический двигатель вращающий шпиндель. Последний имеет конус Морзе, в него может вставляться поводковый центр (с двумя, тремя либо четырьмя ножами и одним острием), патрон или планшайба. С другой стороны станка находится задняя бабка, центр которой поджимает заготовку, удерживая ее в горизонтальном положении.
Поворачивающийся во все стороны подручник, располагающийся как можно ближе к заготовке, поддерживает и направляет резец.
На станках с ручной регулировкой скорость (частота) вращения может переключаться (от 450 до 2000 об/мин) рычагом коробки передач, в которой расположены шкивы с подшипниками. В более сложных моделях станков коробка передач заменена электронным вариатором, позволяющим плавно регулировать скорость на ходу.
Обработка заготовки, зажатой между центрами
Этот способ применяется для обработки деталей цилиндрической формы различной длины, укрепленных между центрами передней и задней бабок. Таким образом вы можете изготовить всякие детали: от миниатюрных шахматных фигур до ножек стола или стоек перил. Особенно опытным мастерам удается даже вытачивать бильярдные кии.
Первый шаг работы заключается в нахождении положения оси деревянной заготовки, чтобы зажать ее между поводковым центром и центром задней бабки. Следующая операция состоит в том, чтобы сделать заготовку (из бруска дерева квадратного сечения или просто из обрезка полена) цилиндрической. Это осуществляется на скорости При этом стружка снимается справа налево с помощью широкой вогнутой желобчатой стамески для черновой обработки – рейера. Если заготовка длинная, черновая обработка производится в несколько этапов; подручник придвигается к детали по мере ее обтачивания, не изменяя своего положения по высоте.
Для вытачивания деталей существуют инструменты разной формы: желобчатая стамеска для обработки фасонной поверхности, плоская стамеска, крючок, полукруглый резец, скошенная стамеска (косяк) и др. В зависимости от типа используемого инструмента и стадии работы следует периодически приближать подручник к заготовке. После завершения процесса, когда деталь уже выточена, производится окончательная отделка (шлифование, полирование, вощение, тонирование и др.) при снятом подручнике.
С помощью углового центроискателя проведите карандашом с обоих торцов заготовки по две-три линии, пересечение которых и будет центром торца.
Сильно ударив молотком по разметочному керну, сделайте канавки и осевое углубление на торцах заготовки.
Наденьте заготовку на поводковый центр, подведите заднюю бабку к противоположному торцу и подожмите ею заготовку так, чтобы поводки хорошо врезались в канавки на торце, а затем отведите центр задней бабки – заготовка должна держаться сама.
Вновь подведите центр задней бабки к заготовке, чтобы зафиксировать ее по оси центров. Поверните маховик задней бабки на четверть оборота, если дерево мягкое, и на пол-оборота, если оно твердое. Заготовка должна быть закреплена так, чтобы ее можно было без сопротивления проворачивать рукой.
Черновая обработка
Для чернового точения цилиндра с помощью рейера установите частоту вращения 1000 или Чем точнее должна быть форма цилиндра, тем большую скорость надо устанавливать. Заготовки с малым припуском на обработку можно проточить с одного прохода по всей длине, с большим припуском – небольшими порциями, двигаясь от задней бабки к шпинделю.
Начинайте работу плавно, опираясь стержнем резца на подручник и держа лезвие так, чтобы пятка резца соприкасалась с деревом. Затем поднимайте ручку стамески до тех пор, пока кромка лезвия не начнет врезаться в дерево, снимая при этом ровную и хорошо скручивающуюся стружку.
Ведите резец в направлении снятия стружки таким образом: одна рука, держащая ручку, задает движение, а другая – лишь поддерживает лезвие (не нажимая на него).
При черновой обработке квадратной заготовки аккуратно срезайте стамеской углы, не слишком на нее налегая. Доведите заготовку до цилиндрической формы наибольшего диаметра, придвигая по мере стачивания припуска подручник по направлению к оси вращения.
В зависимости от того, какую форму вам нужно придать детали, проведите карандашом основные линии разметки выпуклых и вогнутых частей, поворачивая заготовку рукой. Размечайте заготовку так, чтобы наиболее широкие части детали всегда располагались со стороны передней бабки.
Проверка размера
Для того чтобы выточить полутор, воспользуйтесь желобчатой стамеской для обработки фасонной поверхности. Держа ее перпендикулярно оси, «спускайте» режущую кромку с внешней стороны внутрь заготовки, поднимая и слегка поворачивая ручку. Чтобы получить целый тор, произведите ту же операцию с обеих сторон.
Шейка (свод) вытачивается таким же резцом, что и тор. После черновой обработки донышка посередине шейки проточите правую полушейку, на этот раз ведя инструмент снизу вверх и вправо. Никогда не переводите резец сразу с одной стороны шейки на другую – их нужно вытачивать по очереди.
Читать также: Как посадить тую в открытый грунт весной
Листели (маленькие ободки, часто оставляемые с обеих сторон шейки) вытачиваются мейсель-резцом. У него нет задних углов на боковых гранях стержня, как у стамески, но зато есть тонкая канавка для выхода стружек.
Галтель представляет собой плавный переход от одной поверхности к другой – по сути, комбинацию тора и шейки. Поэтому вначале точите шейку, а затем тор, примыкающий к ней.
Деталь, зажатую с двух сторон, никогда не отрезают полностью. Выточите с двух краев канавки, оставляя перемычки маленького диаметра, и отпилите концы ножовкой, предварительно остановив станок.
Чтобы завершить отделку детали, снимите резцедержатель и обработайте деталь снизу мелкой шкуркой (зернистостью от 16 до М63). Во время работы поворачивайте шкурку крест-накрест, чтобы избежать кольцевых царапин.
Высверливаем основание лампы
Обработка заготовки, зажатой с одного конца
При изготовлении коробочки деревянная заготовка закрепляется только с одного конца. В зависимости от формы и размеров детали используются разные средства крепления: патрон с тремя или четырьмя кулачками (некоторые зажимают в восьми точках), патрон «свиной хвост» (с установочными винтами, вкручивающимися в деталь), цанговый патрон или планшайба.
Эта работа требует немалого мастерства. Здесь надо проявить большую аккуратность при вытачивании уступа, чтобы диаметр не сделать меньше, чем нужно.
Надежно зажмите квадратную заготовку в патроне так, чтобы вручную добиться малого биения. Придавая заготовке цилиндрическую форму, вы можете для большей безопасности пользоваться подручником. Когда заготовка приобретет нужную форму, обработайте свободный торец стамеской.
Вначале подрезается буртик крышки, а затем полукруглым резцом выбирается ее внутренность. Подручник располагается со стороны свободного торца заготовки, при этом центр задней бабки снимается.
Из оставшейся в патроне заготовки предстоит сделать коробочку. Как и в предыдущем случае, стачивается торец, и на нем точно прочерчивается диаметр вхождения буртика крышки.
Вырезав по разметке слегка коническое углубление, вбейте в него киянкой крышку. Ее буртик должен быть высотой не менее 5 мм.
Соединение крышки с коробочкой довольно прочное, так что их можно обрабатывать совместно желобчатой стамеской. Работать надо плавными, равномерными движениями, снимая стружку в направлении от более выпуклых частей к более тонким.
Когда вы придадите коробочке нужную форму, вырежьте тонкие бороздки и обожгите их (сделайте темными) с помощью натянутой железной проволоки. Последнюю операцию следует прекращать с появлением дыма.
На готовую вращающуюся коробочку нанесите, распыляя из баллончика, нитролак, а затем обработайте ее стружками.
После этого изделие покройте воском и отполируйте пробкой.
Ручная отделка древесных пород всегда будет актуальна, даже в эпоху абсолютной автоматизации всех производственных процессов, ведь уникальную вещь в подавляющем большинстве случаев можно выполнить только вручную.
Азы токарных работ по дереву на станке могут пригодиться не только профессиональному плотнику, но и начинающим дизайнерам, строителям, да и просто желающим изучить это древнее мастерство.
Работа на токарном станке по дереву, или, как иногда говорят, токарка, в общем-то, не составляет особого труда, но нужно научиться понимать, как бы ощущать обрабатываемое изделие. Именно тогда работа становится подлинным искусством, в котором человек обретает самовыражение, реализует творчество и развивает воображение.
Как вырезать наклейки на строгальном станке без станка
Наклейки-планировщики — это интересный способ сделать ваш ежедневник или пулевой журнал красивее, организованнее и функциональнее.
Если вы хотите наклеить свой ежедневник, дневник или буджо, не разбивая банк, то распечатайте стикеры-планировщики. (Не уверены? Просмотрите весь этот пост о преимуществах наклеек для печати.)
К сожалению, когда у вас нет электронной машины для резки, может казаться, что вы упускаете все удовольствие от создания собственных наклеек. .
К счастью, это неправда! Вы можете сделать свои собственные стикеры-планировщики без резки. Сегодня мы рассмотрим три способа вырезания стикеров-планировщиков дома с помощью таких машин, как Cricut или Silhouette.
Вам нужна электронная машина для резки, чтобы делать собственные наклейки?
Этот пост содержит партнерские ссылки, что означает, что я могу получать комиссию за покупки, сделанные по ссылкам, без каких-либо дополнительных затрат для вас.
Нет!
Да, электронная машина для резки может помочь сделать самодельные наклейки более профессиональными и сэкономить ваше время.
У меня есть две модели Silhouette, и я могу с уверенностью сказать, что:
- Они действительно крутые, когда работают правильно
- Иногда они также являются большой проблемой
- Существуют текущие расходы
- Программное обеспечение Silhouette Может быть неприятно работать с
Режущие станки — это круто , и я часто пользовался своим, когда у меня был магазин Etsy по продаже физических товаров. (И я использовал его еще больше, создавая нашу свадьбу своими руками для таких проектов, как эта гирлянда из бумажных цветов и шары для поцелуев из бумажных цветов.) Но у них свои огорчения и проблемы. Вы можете потратить столько же времени, пытаясь получить правильные настройки с новой наклейкой, сколько вам потребовалось бы, чтобы просто разрезать лист вручную.
Станок для резки необходим, если вы хотите изготовить большое количество наклеек (или наклеек высокопрофессионального вида) в домашних условиях для продажи. Но если вы просто хотите распечатать и использовать свои собственные наклейки, не потратив 200+ долларов на машину, вы можете вырезать свои собственные наклейки вручную.
Как вырезать наклейки вручную
Вот способы вырезать свои собственные наклейки для планировщика вручную. У каждого есть свои плюсы и минусы:
- Использование ножниц
- Маленькие ножницы хороши для точных надрезов и резки нестандартных форм. Большие ножницы подходят для более длинных стрижек.
- Использование резака для бумаги или триммера для бумаги
- Триммер для бумаги отлично подходит для длинных прямых линий, таких как вырезание наклеек на коробки
- Использование металлической прямой кромки и ножа для хобби (нож Xacto)
- Если Практикуясь, вы можете вырезать только верхний слой бумаги для наклеек, чтобы создать настоящий лист наклеек, а не просто стопку вырезанных наклеек
Для некоторых типов наклеек используйте резак для бумаги в сочетании с небольшими точными наклейками работает хорошо. Например, вы можете легко вырезать длинные ряды из этого набора бесплатных распечатываемых функциональных наклеек с вертикальным флажком с помощью резака для бумаги, а затем небольшими ножницами вырезать выемку в нижней части каждой наклейки.
Инструмент под названием Gyro-Cut может создавать точные разрезы кривых и различных форм, , но он требует некоторого обучения. Если вы собираетесь потратить время на практику, это может быть отличным выбором. Если вы предпочитаете использовать уже имеющиеся дома расходные материалы и сразу же приступить к резке, воспользуйтесь одним из методов, о которых я расскажу в этой статье.
Как вырезать стикеры вручную видеоурок
Как говорится, картинка стоит тысячи слов и все такое. Вот почему я создал видео , демонстрирующее эти три техники вырезания наклеек. Я рекомендую посмотреть видео, если у вас есть возможность, и прочитать оставшуюся часть сообщения, чтобы получить полное представление о том, как успешно вырезать свои собственные наклейки вручную.
Как вырезать наклейки ножницами
Я не рекомендую вырезать весь лист наклеек вручную ножницами, если только это не единственный вариант.
Для длинных и крупных разрезов используйте острые ножницы большего размера. Недавно я купил титановые ножницы Scotch с антипригарным покрытием, и они режут . Я часто пользовался ножницами (в моем магазине Etsy продавались как тканевые изделия, так и вывески с обрезанным винилом, после колледжа я работал в копировальном центре и был учителем в классе. Я использовал штук, много штук). ножницы.)
Для небольших и точных разрезов я предпочитаю эти маленькие антипригарные ножницы Fiskars. Это моя вторая пара этих маленьких ножниц — я использовал первую пару более 5 лет и заменил их только потому, что я их потерял.
Маленькие ножницы идеально подходят для более детального дизайна. Они идеально подходят для небольших и точных надрезов, таких как буква «v» в нижней части этих наклеек с флажками. Вы также можете использовать их для более точного вырезания любого рисунка, который вы распечатываете, чтобы создать более профессиональный стикер, чем просто коробка.
Продажа Fiskars 154110-1001 Ножницы для деталей с антипригарным покрытием Titanium Softgrip, 5 дюймов, …- Идеально подходят для резки узких узоров и быстрых надрезов на самых разных материалах, включая бумагу, картон, ленту и многое другое. покрытие лезвия позволяет легко прорезать материалы с помощью липкого клея.
- Лезвия из нержавеющей стали с усиленным титаном обеспечивают чистые разрезы и остаются острыми при интенсивном использовании. и создайте шаткие края, если вы не будете очень медленными и осторожными.
С другой стороны, у вас, вероятно, уже есть ножницы, и вы знаете, как ими пользоваться, так что можете сразу приступить к работе. Ножницы, особенно точные, позволяют вырезать более сложные конструкции, а не просто коробки.
Использование резака для бумаги для вырезания наклеек
Существует два различных типа резаков для бумаги в домашних условиях: с поворотным лезвием гильотинного типа и резаки для бумаги с маленьким горизонтально перемещающимся лезвием, которое движется по направляющей.
Часто модели с поворотным рычагом называются ножами для бумаги , а менее устрашающие на вид с небольшим лезвием, которое проходит вдоль направляющей, называются ножами для бумаги .
Резаки для бумаги более мощные и могут разрезать несколько листов за раз, если все выровнено правильно и вы надежно удерживаете страницы на месте. При этом я редко вытаскиваю свой огромный старый резак для бумаги из туалета.
Лично я считаю, что триммер для бумаги моего Fiskar довольно точен и намного безопаснее носить дома с маленьким ребенком. Лезвие может немного заклеиться из-за большого количества обрезков наклеек, но вы можете протирать его между использованием, а лезвия дешевы и легко заменяются.Триммер также меньше и легче, чем «резак». Это то, что я использую в течение многих лет:
Sale Fiskars SureCut Deluxe Craft Paper Trimmer 12 дюймов, 1,44×10,31×18,06- Идеально подходит для резки широкого спектра материалов для творчества, включая бумагу, фотографии, страницы альбома для вырезок или специальные материалы
- Самая широкая база на рынке (6 1/4 дюйма) делает резку карточек проще, чем когда-либо.
- Линия резки проволоки Sure Cut позволяет легко увидеть, где режется лезвие, обеспечивая непревзойденную точность
Обрезка наклеек с помощью триммера для бумаги довольно просто. Тщательно совместите то место, где вы хотите разрезать, с разработанной линией разреза. Триммеры для бумаги имеют направляющую проволоку, которая упрощает эту задачу. Плотно удерживайте страницу вдоль верхней части резака и нарежьте ее.
Мне нравится делать длинные надрезы резаком для бумаги и ножницами разрезать отдельные наклейки. Делать много маленьких, коротких надрезов с помощью триммера для бумаги утомительно.
Как вырезать наклейки вручную с помощью линейки и ножа
Наконец, есть (потенциально) наиболее точный, но и самый трудоемкий метод: вырезание наклеек не с помощью металлической линейки и ножа для хобби.
Важно использовать прямую кромку из металла, а не из пластика или дерева. Ваш нож легко режет пластиковую или деревянную линейку, оставляя зазубрины и получающиеся неточные края. У меня есть недорогая упаковка металлических линейок. Они также отлично подходят для ведения дневника пули!
Этот метод лучше всего подходит для резки прямых линий. Может использоваться для вырезания выемки на флажках. Вы также можете (аккуратно) вырезать коробки из наклеек, если хотите сделать рамку.
Я рекомендую подложить под лист коврик для резки перед тем, как начать резку. Если у вас нет коврика для резки, в крайнем случае можно использовать кухонную разделочную доску.
Осторожно расположите линейку вдоль края, который вы хотите отрезать. Возможно, вы захотите расположить его немного смещением от точной линии разреза. Немного выдавите его, чтобы получить небольшую белую рамку, или немного, если хотите убедиться, что на нем нет белых пятен.
Удерживая линейку на месте, осторожно разрежьте ее по краю. Со временем вы можете использовать острое лезвие, чтобы прорезать слой наклейки, но не , а не , чтобы прорезать подложку для наклеек. Это создает более профессионально выглядящие листы наклеек, которые легко хранить в файле или папке.
Наслаждайтесь своими наклейками-планировщиками!
Теперь вы знаете, как вырезать стикеры-планировщики вручную! Примените свои новые знания на практике, загрузив эти бесплатные наклейки для планировщика с сайта The Artisan Life:
Наклейки для планировщика для печати
Наклейки для печати — это интересный способ украсить свой планировщик и сделать его более функциональным без посещения хранить.
Преимущества наклеек для печати
Не уверены, о чем идет речь? Откройте для себя преимущества распечатываемых наклеек-планировщиков.
Продолжить чтение
Изучение того, как сделать сферу
В нашем обществе, где быстро выбрасываются вещи, пластик и резина, кажется, правят. Однако многие по-прежнему ценят стабильность, мастерство и непреходящую красоту. Предметы древних цивилизаций, выставленные в музеях, такие как чаши, украшения и предметы искусства, часто изготавливаются из камней.Их прочность не имеет себе равных, а сделанные из агата, яшмы или других разноцветных камней они завораживают. Сферы всегда привлекали внимание, будь то 15-тонные древние каменные сферы Коста-Рики или крошечные разноцветные шарики. Хотя каменные сферы являются одной из самых простых форм, их изготовление требует много времени.
Что нужно для изготовления шара? Начните с выбора подходящего камня. Монтана полна великолепных пород: агат, яшма, окаменелое дерево, кости динозавра, гранит, кальцит и т. Д.Изделие, подходящее для изготовления сфер, должно иметь красивый контраст, интересные узоры или удачные сочетания цветов. Изделие не должно иметь видимых трещин или линий излома. Избегайте камней, участки которых могут быть плохо отполированы. Чем мягче камень, тем легче будет придать ему форму. Однако, возможно, и его легче сломать. После того, как камень выбран, следует измерить его высоту, ширину и глубину. Наименьшее измерение определяет максимальный размер сферы, которую можно сделать. Используя каменную пилу с алмазными лезвиями, следует сделать надрезы, чтобы получился куб.Продолжая каменную пилу, отрежьте углы и края куба. На данный момент было сделано 22 разреза, и в результате у вас останется восьмиугольник или что-то похожее на граненый шар.
Теперь следует использовать шлифовальный станок с кругами из карбида кремния для шлифования любых оставшихся выступов. Каждый шаг огибает камень, но он все равно будет ухабистым. Окончательную шлифовку лучше всего производить на специализированном гранильном оборудовании, называемом сферическим станком. Существуют двух- и трехкомпонентные сферические машины. Эти противоположные чашки оказывают давление с противоположных сторон и поддерживают неровную сферу, при этом позволяя сфере произвольно вращаться.Это многоступенчатый процесс, в котором используются песок и вода. На каждом этапе используется различная жесткость зерна, начиная с грубого зерна и заканчивая очень мелким зерном, примерно так же, как при работе с деревом используется все более мелкая наждачная бумага.
Хотя скала теперь круглая, она также тусклая. Его необходимо вымыть водой с мылом, а чашки в машине для сфер заменить на полировальные. Очистку следует проводить тщательно и осторожно, так как даже один кусочек песка может поцарапать сферу и помешать ей полностью отполироваться.Для окончательной полировки будет использоваться суспензия из воды и полировальной пасты.
Щелкните здесь, чтобы увидеть полный PDF-файлВосхитительно круглая, красиво отполированная и надежно сделанная сфера теперь готова для восхищения и передачи ее будущим поколениям. Разглядывать различные минералы и преломления в каменных сферах одинаково успокаивающе и захватывающе. Посетите «Сокровища Земли» по адресу 25 N. Willson в историческом центре города Бозман и полюбуйтесь сферами, сделанными из камней, найденных в Монтане и по всему миру. Позвоните по телефону 406-586-3451 или посетите сайт www.EarthsTreasuresMT.com.
Как распылить эфирные масла без диффузора
Иногда кажется, что нам всегда нужно вытаскивать наши ультразвуковые диффузоры, чтобы ароматически насладиться преимуществами эфирных масел. Есть много способов использовать наши эфирные масла без диффузора. Я покажу и расскажу, как распространять ароматические соединения без диффузора. Это почти как если бы под рукой был диффузор, сделанный своими руками.
Посмотрите видео ниже, чтобы увидеть все крутые способы, или дочитайте до конца.Мой любимый способ распыления эфирных масел — №26, да, есть и бонус!
Начнем прямо сейчас!
Мои любимые 25 способов распыления эфирных масел без диффузора
1. Рулоны туалетной бумаги.
Использование старых добрых рулонов туалетной бумаги в качестве диффузора — это просто великолепно. У вас может быть свежая ванная комната, даже если кто-то забыл спрей. Прежде чем положить рулон туалетной бумаги на решетку, капните 2-3 капли ваших любимых эфирных масел в среднюю трубку.Каждый раз, когда кто-то приходит в туалет и снимает туалетную бумагу, она перемещается по воздуху и рассеивает частицы масла, чтобы вы могли наслаждаться. Выбирайте масла, которые вы здесь используете, исходя из личных предпочтений. Я люблю добавлять цитрусовые масла в наши рулоны туалетной бумаги, потому что вся наша семья любит запах каждого из них. Это идеальный дешевый самодельный диффузор.
2. Рулоны бумажных полотенец
Знаете ли вы, что с рулонами бумажных полотенец можно делать то же самое, что и с туалетной бумагой? Теперь ты знаешь! Есть так много отличных вариантов, которые вы можете добавить сюда, но в моей семье мы придерживаемся лимона, апельсина и лайма в этой части нашего дома.Нет ничего проще диффузора, сделанного своими руками, не так ли? Все, что вам нужно сделать, это просто капнуть пару масел на внутреннюю часть ролла!
3. Печные фильтры
Это один из моих самых любимых способов распыления эфирных масел без диффузора. Каждый раз при замене фильтра мы добавляем несколько капель наших любимых масел или их комбинаций. Обычно мы выбираем масла, которые не слишком сильны, а просто дадут приятный аромат. К сожалению, если вы когда-либо использовали этот метод, вы знаете, что запах длится недолго.Вам нужно будет добавлять больше капель каждые несколько дней, если вы хотите постоянно чувствовать запах масла в печи. PRO TIP — Компания приедет на ужин? Продам свой дом? Нанесите немного эфирных масел на фильтр печи прямо перед тем, как люди войдут в комнату, чтобы получить приятное, воодушевляющее впечатление. У нас есть много смесей для печенья и осенних диффузоров, которые обычно нравятся большинству людей и отлично подойдут, особенно если у вас есть день открытых дверей или вы пытаетесь продать свой дом.Для этого вам даже не нужно делать диффузор своими руками, просто вытащите фильтр, капните немного масла, и все готово.
4. Диффузор своими руками ватные шарики
Знаете ли вы, что можно положить ватный диск в бутылку с почти пустой (или даже если она кажется пустой) бутылкой с эфирным маслом? Вставьте ватный диск и закройте крышку. Затем оставьте это на 48 часов и позвольте ватному тампону впитать все эфирные масла до последней капли. Удалите ватный диск (может потребоваться пинцет или шпажка).В зависимости от используемого эфирного масла мне нравится прятать эти маленькие самодельные диффузоры в неприметных местах дома. Чтобы отпугнуть насекомых и пауков, я прячу их за вагонами, возле плинтусов и т. Д. Чтобы освежить машину, я использую цитрусовые и кладу их под сиденья, в карманы и т. Д.
5. Прямо из бутылки
Это настолько простое, что иногда я совершенно забываю, насколько легко это сделать. Вам буквально не нужно ничего, кроме бутылки эфирного масла. Просто снимите колпачок и сделайте большой вдох, задержите его на пару секунд, отпустите и повторите.Я проделывал это несколько раз, как в настоящей «чрезвычайной ситуации». Иногда, когда я летаю, я немного нервничаю, и я не хочу, чтобы весь самолет пахло моими маслами. Я просто открою пробную бутылку с бергамотом, мятой, имбирем и т. Д. И сделаю пару вдохов. Когда у вас нет под рукой диффузора, это самый быстрый и простой способ насладиться эфирными маслами. Что, если вы хотите наслаждаться смесью без диффузора? Нет проблем, просто откройте крышки 2-3 разных бутылочек с маслом и вдохните их все одновременно! (мы действительно делаем это, когда тестируем смеси)
6.Используя свои добрые руки
Еще один отличный способ насладиться ароматическими маслами — это положить одну каплю на ладонь одной из рук. Затем потрите обе руки вместе, положите ладони на нос, вдохните и наслаждайтесь. Мне также нравится делать это после того, как я нанесу эфирные масла на свое тело, точки пульса и ступни. Обычно у меня на руках остается немного остаточных масел, поэтому я пользуюсь этим и наслаждаюсь ими.
7. Сделайте спрей для комнаты
Изготовление спрея с эфирными маслами для комнаты — один из моих любимых способов наслаждаться эфирными маслами в моем доме.Это так быстро и удобно. Мне не нужно искать вилку, чтобы подключить диффузор. Мне не нужно наполнять резервуар водой. Как только мой спрей будет готов, я могу просто сунуть его в карман и пойти из комнаты в комнату, распыляя эфирное масло по всему дому. У нас есть много хороших рецептов по приготовлению спрея для помещений, но вот краткий обзор; Если вы хотите перепрофилировать некоторые из ваших бутылок и спасти свалку, возьмите любимую почти пустую бутылку из-под масла. Добавьте несколько капель нескольких разных масел, чтобы получилась смесь, или просто добавьте 15 капель своего любимого аромата.Затем я люблю добавить немного соли и чайную ложку водки или гамамелиса. Долейте воду в бутылку с эфирным маслом (оставив немного места для распылительной насадки) и добавьте распылительную насадку. Вы можете приобрести здесь аэрозольные насадки, которые подойдут к вашим флаконам с эфирными маслами объемом 5 и 15 мл. Как это круто?
8. На новогодней елке
У меня есть пара рождественских украшений, которые я купил специально для эфирных масел. Если у вас его нет, а у вас деревенское дерево, вы можете сделать симпатичный орнамент из войлока или дерева и добавить пару капель сибирской пихты.О, оно пахнет потрясающе, и если у вас есть искусственное дерево, оно будет пахнуть почти так же хорошо, как настоящее! Только не забывайте обновлять украшение каждые несколько дней. Раньше у меня был плагин с ароматом сосны, без которого я не мог ЖИТЬ. Теперь, когда я пытаюсь озеленить свой дом, они уже давно выброшены. Я действительно счастлив, что теперь могу легко наслаждаться свежим ароматом сосны всю зиму с небольшим украшением диффузора, сделанным своими руками, без каких-либо агрессивных химикатов!
9. Шишки душистые
В магазине можно купить шишки с ароматом и без.Поскольку я стараюсь быть немного более осторожным с нашей химической нагрузкой, я выбираю те, которые не содержат запаха (вы также можете использовать те, которые вы найдете у себя во дворе или в походах, просто обязательно сначала запеките их, чтобы убить любых насекомых и тварей) . Поскольку корица и сосна — это своего рода союз, заключенный для меня на небесах, я люблю использовать оба эфирных масла на своих шишках. Я просто добавляю по капле каждого (иногда легче смешать масла, прежде чем нанести их на шишки). Что мне так нравится в сосновых шишках, так это то, что я использую много сосновых шишек в своих зимних украшениях.Это позволяет легко установить диффузор из сосновой шишки во многих местах вашего дома. Просто обновляйте каждые несколько дней по мере необходимости или прямо перед приходом компании! Вы также можете смешать его с «спреем для комнаты» и опрыскивать украшения своим спреем так часто, как захотите.
10. Ожерелья с эфирным маслом
Ювелирные изделия с эфирным маслом прошли долгий путь даже за последний год. Вы можете носить множество симпатичных модных ожерелий, которые можно украсить своим любимым эфирным маслом.Некоторые используют терракоту, масляные подушечки или бусинки из лавы. Мои любимые ожерелья, вероятно, будут с бусинкой лавы. Это так красиво и больше похоже на модные украшения. Опять же, я ненавижу летать, поэтому я обычно ношу ожерелье и добавляю на него немного лаванды, бергамота или имбиря, прежде чем самолет взлетит. Это помогает мне расслабиться и почувствовать себя более заземленным. Я также могу просто поиграть со своим ожерельем, если мне нужно больше аромата масел, не привлекая к себе слишком много внимания.
11.Браслеты с эфирным маслом
Не думайте, что на вечеринку модных украшений идут только ожерелья. Теперь есть множество милых новых стилей браслетов. Сложите их с другими модными украшениями, чтобы получился забавный образ. Опять же, они обычно идут с масляными подушками и лавовыми камнями.
12. Прищепки деревянные
Освежите свой шкаф, нанеся 1-2 капли вашего любимого эфирного масла на прищепку. Затем просто повесьте юбки и штаны и дайте им раствориться в шкафу.Это также отлично работает, если вы используете прищепки для магнитов, на которые можно вешать бумаги.
13. Ароматические ингаляторы
Ингаляторы аромата становятся все более популярными. Мы даже продаем наборы для ингаляторов своими руками. Я сделал один из наборов ингаляторов своими руками и беру его с собой в путешествия. Есть что-то в способности успокаивать мои эмоции и поддерживать свое тело, когда я путешествую, это очень хорошо, успокаивает меня! Это ваш собственный маленький диффузор, сделанный своими руками. Посередине ингалятора есть небольшой фитиль.Вы просто капаете на него несколько масел или свою смесь, а затем снова соединяете. Рекомендуется не класть его полностью в нос, чтобы насладиться преимуществами. Просто закройте одну ноздрю и вдохните с помощью ингалятора чуть ниже носа. Повторите с другой стороны. Опять же, я благодарен за то, что нашел способы избавиться от некоторых токсичных предметов в моем доме, включая некоторые лекарственные ингаляторы, купленные в магазине.
14. Подушка и льняной спрей
Как и комнатные спреи, я люблю брать почти готовую бутылку лаванды или любого другого успокаивающего, заземляющего масла, чтобы приготовить их.Вам понадобится почти пустая бутылка масла (осталось около 15 капель), распылитель, немного гамамелиса и немного воды. Поместите ингредиенты в 15-миллилитровую бутылку, наденьте распылительный колпачок и наслаждайтесь. Распылите на подушку и простыни и дайте им высохнуть, прежде чем лечь в постель.
15. Диффузоры для домашних животных
Теперь есть маленькие диффузоры, которые можно прикрепить к ошейнику вашего питомца. Не знаю, как вы, но я думаю, что это чертовски круто. Если у вас когда-либо было домашнее животное, которое напугано или немного нуждается в дополнительном комфорте, вы знаете, насколько это может быть ценно.У вас есть собака, которая прячется при каждом раскате грома? Вы можете попробовать диффузор для домашних животных.
16. Фаворит Бланки
Большинство детей носят с собой любимое одеяло первые несколько лет своей жизни. Просто пришейте небольшую фетровую нашивку к одному углу одеяла. Добавьте пару капель эфирного масла лаванды, дайте ему высохнуть, а затем верните малышу. Это отличный способ вздремнуть, чтобы помочь им расслабиться и засыпать.
17. Чучела животных
Чучела животных могут иметь такую же войлочную нашивку, как одеяло.Просто пришейте его к любимой игрушке, добавьте пару капель любимого масла, дайте ему высохнуть и верните ребенку. У них может быть даже любимое масло, которым они захотят полить свою любимую игрушку. Это отличный способ познакомить детей с эфирными маслами.
18. Душевые бомбы / расплавы
Сезонные угрозы вас расстроили? Не беспокойтесь, просто бросьте бомбу для душа в душ, чтобы насладиться ее терапевтическим эффектом, пока вы принимаете душ. Когда я иду в душ, мне нравится откладывать эти плавки в сторону.Будьте осторожны, не кладите его куда-нибудь, чтобы за него споткнуться. Что касается меня, я просто не хочу, чтобы в него попала основная вода, потому что в этом случае она растворится довольно быстро.
19. Самодельные бомбы для ванны
Нет ничего прекраснее, чем принять горячую ванну в конце долгого дня с несколькими каплями ваших любимых эфирных масел. Здесь вы найдете отличные рецепты бомбочек для ванн. Вы можете настроить ароматы для нужной вам поддержки. Пока ваша бомба в ванне шипит и тает, вы также получите удовольствие от ароматерапии с помощью эфирных масел, которые вы добавляете в бомбы для ванны.
20. Соль для ванн своими руками
Еще один из моих любимых способов насладиться ароматическими соединениями — это соли для ванн. Это идеальный самодельный диффузор. Использование и приготовление солей для ванн таким способом полезно как с точки зрения аромата, так и с точки зрения местного действия. Что мне нравится в солях для ванн, так это то, что они используют соли Эпсома и содержащиеся в них магний расслабляют мышцы. Совместите это с эфирными маслами, и вы мгновенно расслабитесь.
21. Диффузор водяных шариков
Водные бусинки — еще один из этих ГОРЯЧИХ продуктов.Они отлично подходят для детей с сенсорными проблемами или просто для развлечения! Если ваши дети собираются играть руками с водяными бусинами, почему бы не добавить в них немного полезных эфирных масел? Когда вы делаете водяные бусины, добавьте несколько капель вашего любимого эфирного масла (например, гамамелиса) и перемешайте, чтобы масло равномерно распределилось в воде. Затем, пока вы играете с водными бусами, вы можете насладиться ароматерапией. Если вам нужно добавить больше воды в бусинки, освежитесь еще несколькими каплями эфирного масла!
22.Диффузор для макияжа
Вместе с диффузором из ватного тампона. Если у вас есть не ватные шарики, а салфетки для макияжа или даже салфетка, вы можете сделать то же самое. Просто нанесите пару ваших любимых эфирных масел на подушечку и положите их там, где хотите (у плинтуса, в машине и т. Д.).
23. Герконовый диффузор
Герконовые диффузоры технически уже являются диффузорами, но не вставными. Вы можете купить тростниковый диффузор в большинстве домашних магазинов или в Интернете. Вы просто кладете тростник в небольшую стеклянную емкость, в которой хранятся масло и вода.Камыши всасывают масло и воду и начинают распространять эфирные масла в воздух. Это действительно интересный способ насладиться преимуществами вашего эо.
24. Дезодоратор и диффузор для ковров
Просто смешайте немного пищевой соды и ваши любимые эфирные масла. Посыпьте ковер перед сном и пропылесосьте, когда проснетесь. Постарайтесь не ходить по нему, чтобы он не углубился глубоко в ваш ковер. Это отличный способ освежить свой дом и насладиться преимуществами эфирных масел.
25. Сумка для попурри
Многие часто забывают об этом, но я знаю, что мои мама и бабушка сделали их много лет назад. Просто соберите несколько сухих цветов и небольшой тканевый мешочек на шнурке. Добавьте к засушенным цветам несколько капель ваших любимых эфирных масел и наполните пакет. Положите в ящик для носков, в шкаф, под автокресло и в любое другое место, где нужно освежиться. Время от времени встряхивайте сумку, чтобы рассеять больше масел, а также вы можете обновлять ее каждую неделю или около того, добавляя в нее еще немного масел.
26. БОНУСНЫЙ ДИФФУЗОР DIY — Fake Snow
Это тот, о котором люди НИКОГДА не писали в блогах, и я очень рад поделиться с вами своим 26-м, последним и любимым способом распыления эфирных масел без диффузора. Вы можете купить поддельные снежные пакеты в магазинах примерно с октября или получить их в других интернет-магазинах круглый год. Просто сделайте искусственный снег в соответствии с указаниями производителя. Когда вы добавляете воду в искусственный снег, мне нравится добавлять свои эфирные масла.Начните с нескольких капель, вы всегда можете добавить еще. Вы любите украсить искусственным снегом на праздники или даже хотите потушить деревню искусственным снегом? Добавление эфирных масел в снег — отличный способ оживить комнату и зимнюю сцену. Выберите любимый рождественский аромат, такой как коричное, сосновое, пихтовое или еловое масло.
Мы очень надеемся, что вам понравился наш урок по использованию эфирных масел без традиционного диффузора. Какой из них вы еще не пробовали и собираетесь использовать сейчас?
Как изменить поверхность шара для боулинга вручную
Несмотря на то, что боулинг существовал в той или иной форме на протяжении тысячелетий, современная версия игры появилась лишь чуть более 100 лет назад.Именно тогда боулинг стал стандартизированным, были разработаны официальные правила и предписаны точные спецификации для шаров, кеглей и дорожек для боулинга.
Хотя боулинг существует уже много лет, он остается популярным среди американских энтузиастов отдыха во всех возрастных группах, включая детей и молодых людей. Боулинг настолько популярен среди детей в возрасте от шести лет и старше, что более 30 процентов из них играли в боулинг хотя бы раз в 2007 году . В том же году примерно — два процента населения страны () в возрасте 15 лет и старше могли играть в боулинг в любой день.
Хотя игра в боулинг не сильно изменилась за последнее столетие, шары для боулинга изменились. Самые ранние версии сегодняшних шаров для боулинга были сделаны из дерева и часто не имели отверстий для захвата, что означало, что игрокам приходилось складывать шары ладонью, чтобы играть. Начиная с начала 1990-х и в течение следующих пяти десятилетий или около того, шары для боулинга обычно делались из твердой резины. В конце 1950-х — начале 1960-х резиновые шары начали заменять шарами для боулинга, состоящими из полиэстера.
С 1980-х годов шары для боулинга претерпели значительные изменения как внутри, так и снаружи. На внешней стороне полиуретановые покрывающие материалы получили распространение в 80-х годах, за ними последовали покрывающие материалы из реактивных смол в начале 1990-х годов и покрывающие материалы из твердых частиц позже в том же десятилетии. Эти достижения в области покрытия позволили шарам для боулинга создавать значительно большее трение с поверхностью дорожки для боулинга. В результате новые шары для боулинга дали игрокам больше возможностей зацепиться за дорожку и улучшить угол входа в кегли по сравнению с их предшественниками.
Помимо изменения внешнего вида своих шаров, производители шаров для боулинга также внесли изменения во внутреннюю часть своих шаров в течение этого периода времени. Используя усовершенствованные ядра, также известные как блоки веса, производители производили шары для боулинга с динамически несбалансированными ядрами. Эти новые ядра способствовали увеличению количества крючков, которые боулеры могли производить на дорожке.
Компоненты шара для боулинга
В целом современные шары для боулинга часто классифицируются как состоящие из трех или двух частей.В прошлые десятилетия данная классификация мяча относилась к буквальному количеству частей, которые использовались для создания мяча, но сегодня это не обязательно так, когда речь идет о шарах, состоящих из двух частей. Шарики, состоящие из трех частей, по-прежнему обычно состоят из трех компонентов: тонкого покрывающего материала, наполнителя и весового блока для блинов.
Состоящие из двух частей шары, которые производятся сегодня, часто состоят из более чем двух компонентов из-за добавления грузовых блоков во внешнем сердечнике, который отделен от накладки шара.Это означает, что шар, состоящий из двух частей, обычно состоит из трех частей: крышки, сердечника и внешнего сердечника.
Независимо от того, состоит ли у вас шар для боулинга, состоящий из трех или двух частей, покрытие вашего шара будет влиять на его поведение на дорожке больше, чем любой другой компонент, используемый для создания шара. Фактически, от 60 до 80 процентов эффективности вашего мяча на дорожке будет зависеть от его накладки. Напротив, только 20-40% производительности вашего мяча будет зависеть от его сердечника, схемы сверления и других физических свойств.
Отшлифованные и отполированные накладкиПоскольку покрытие вашего мяча так сильно влияет на вашу игру, важно понимать, как состояние покрытия вашего мяча влияет на эффективность вашего мяча на дорожке. Как правило, шары для боулинга изготавливаются с шлифованной или полированной поверхностью. Проще говоря, ваш шар для боулинга будет создавать большее трение с дорожкой, если у него шероховатая или отшлифованная поверхность. Если вы хотите, чтобы ваш мяч зацепился раньше к концу масляного рисунка дорожки, вы, вероятно, предпочтете отшлифованную покрышку полированной.И наоборот, если вы хотите, чтобы ваш мяч прошел дальше по дорожке, прежде чем он начнет зацепляться, мяч с полированной поверхностью — правильный выбор.
Независимо от того, имеет ли ваш мяч шлифованную или полированную поверхность, вы можете обработать верхнюю часть мяча, чтобы она лучше соответствовала вашему личному стилю игры, а также состоянию дорожки, на которой вы будете играть. Покрытие вашего мяча имеет определенные характеристики, которые вы должны учитывать, когда готовитесь к модификации поверхности вашего мяча, потому что внесение изменений повлияет на величину трения, которое ваш мяч будет создавать на дорожке.
К этим характеристикам относятся следующие:
- Шероховатость : Шероховатость покрытия вашего шара определяется расстоянием между пиками и впадинами на его поверхности, высотой и глубиной этих максимумов и минимумов, а также химическим составом обложку и ее отделку. Как обсуждалось ранее, более шероховатая поверхность обычно вызывает повышенное трение на полосе движения.
- Скорость абсорбции : Современные покрытия из реактивной смолы проницаемы, что означает, что они абсорбируют жидкости, в том числе дорожное масло.Шары с более высокой степенью поглощения создают повышенное трение в игре.
- Твердость поверхности : Хотя твердость поверхности сегодня не так актуальна, как в предыдущие десятилетия, твердость накладки вашего мяча по-прежнему может влиять на общие характеристики мяча на дорожке. Как правило, чем мягче поверхность мяча, тем меньше трение мяч с дорожкой.
Если вы собираетесь участвовать в мероприятии, санкционированном Конгрессом по боулингу США, накладка вашего шара должна соответствовать следующим требованиям:
- Средняя шероховатость поверхности от пика до впадины : Средняя шероховатость поверхности от пика до впадины накидку шара часто называют «Ра.«Для участия в матче по боулингу USBC покрытие вашего шара должно иметь Ra менее 50 микродюймов при чистоте поверхности 500 Abralon.
- Коэффициент трения сухой дорожки : Также известный как «COF», коэффициент трения вашего мяча на сухой дорожке должен быть меньше 0,32 при проверке USBC в определенных условиях.
- Твердость : твердость вашего мяча должна составлять 72 или более при оценке с помощью твердометра по Шору типа D, чтобы вы могли участвовать в соревнованиях по боулингу USBC.
Хотя вы не можете изменить твердость шара для боулинга, вы можете поддерживать его в оптимальном состоянии. Базовое обслуживание включает вытирание мяча перед каждым ударом. Частое протирание мяча поможет ему равномерно катиться, а также предотвратит впитывание масла покрывающим слоем мяча. По окончании игровой сессии следует также протереть шар для боулинга подходящим чистящим средством.
После каждых 75 игр или около того, как правило, рекомендуется использовать жидкое моющее средство для тщательной очистки мяча. Конечно, также целесообразно очистить полотенце для боулинга. Спорный вопрос, как часто вам следует поднимать или перекрашивать шар для боулинга для максимальной производительности. Некоторые источники говорят, что вам следует вернуться на поверхность после шестидесяти игр, в то время как другие предполагают, что вы можете сыграть более чем в четыре раза больше матчей, прежде чем вам понадобится повторно всплыть на поверхность. На то, как часто и когда вам нужно будет восстанавливать поверхность мяча, влияют многие факторы, в том числе зона отслеживания мяча.Когда на беговой дорожке появляются признаки износа, обычно следует подумать о том, чтобы смазать мяч.
Инструменты для самостоятельной шлифовки шаров для боулингаВвиду того, что односкоростные и многоскоростные прядильщики для мячей становятся все более доступными, многие боулеры применяют методы самостоятельной шлифовки шаров для боулинга. Независимо от того, планируете ли вы восстановить шар для боулинга без вертушки или с ней, вам понадобятся некоторые базовые инструменты, чтобы выполнить работу правильно.
Для восстановления поверхности шара для боулинга вам понадобятся следующие предметы:
- Sanding Agent : у вас есть выбор, когда дело доходит до того, что вы собираетесь использовать для шлифования шара для боулинга.В то время как некоторые люди используют наждачную бумагу или подушечки 3M Scotchbrite для обработки своих шаров, также популярны шлифовальные подушечки и диски Mirka Abralon и SIA, которые мы продаем в National Abrasives, Inc.
В зависимости от ваших целей по шлифовке вам могут потребоваться разные уровни зернистости, то есть вам может потребоваться более одного шлифовального агента. Пневматические диски SIA имеют зернистость от 240G до 4000G. Подушечки Abralon доступны в следующих зернах:
- 180G; 360 г; 500 г; 1,000G; 2,000G; 4,000G
- Вода : вам понадобится емкость с водой, достаточно большая, чтобы вы могли ополоснуть шлифовальные диски.Вам также понадобится распылитель, наполненный водой, чтобы вы могли поливать шар для боулинга по мере необходимости. Использование воды в процессе шлифовки дает два преимущества. Во-первых, он сохраняет ваш мяч и руки смазанными и прохладными, несмотря на трение, связанное с шлифованием. Это также помогает предотвратить бесполезное распространение пыли, которую вы создаете при шлифовании мяча.
- Полотенца и полировальные подушечки : если вы собираетесь нанести состав или полироль на шар для боулинга после того, как закончите его шлифовку, вам также понадобится несколько полотенец или полировальных подушек.Вы должны использовать разные полотенца или подушечки для каждого продукта, которым вы наносите на мяч. Используйте одно полотенце, чтобы нанести состав, второе, чтобы нанести полироль, а третье, например, очистить мяч.
- Состав, полироль и чистящее средство : Убедитесь, что требуемый состав, полироль и чистящие средства доступны для использования после того, как вы закончите шлифовать мяч.
- Прядильщик для боулинга : Если у вас нет доступа к вертушке для боулинга, вы можете вручную восстановить поверхность шара с помощью домашнего набора для шлифовки.
Поверхность шара для боулинга обычно можно восстанавливать любое количество раз до тех пор, пока имя его производителя не исчезнет с его поверхности. Пытаетесь ли вы придумать, как заново покрыть шар для боулинга дома в первый раз, или вы уже освоили этот процесс после многократной шлифовки шара, процесс в основном один и тот же.
Первый шаг к шлифовке шара для боулинга — решить, какие результаты вы хотите получить от процесса шлифовки.Ваши конечные цели будут определять, какую зернистость вы будете использовать, а также какую технику шлифования вы будете использовать. В целом, более мелкая зернистость поможет вашему мячу лучше справляться с сильно смазанными дорожками и подходит для игроков, у которых высокая скорость мяча в сочетании с низким числом оборотов, потому что они оставят ваш мяч с большей поверхностью.
Более высокая зернистость оставляет меньше поверхности на вашем мяче и подходит для игроков, которые хотят большего контроля, потому что более крупная крупа продлит фазу захвата мяча во время игры.
В зависимости от используемой техники шлифования вы можете создать более ранний или более поздний крючок, увеличенный или уменьшенный крючок и изменение длины. Самый распространенный метод шлифования — это пересечение песка под углом 90 градусов от первоначального рисунка шлифования мяча. Если вместо этого вы шлифуете исходную дорожку вашего мяча, ваш мяч будет иметь большую длину в сочетании с большей агрессией в задней части дорожки. Чтобы получить ранний бросок в паре с менее агрессивным бэкендом, вам нужно будет отшлифовать начальную траекторию мяча.
Если вы не надеетесь достичь определенной цели с помощью определенной техники шлифования, обычно рекомендуется поместить шар для боулинга в спиннер так, чтобы центр его ручки находился вверху, когда вы будете готовы начать шлифование. Когда вы закончите шлифовать открытую поверхность, вы повернете мяч на 180 градусов. Когда вы закончите работу с этой поверхностью, вы повернете мяч на 90 градусов.
Наконец, вы поверните шар еще на 180 градусов и продолжите шлифование, чтобы убедиться, что вы отшлифовали всю поверхность покрытия шара.Другой способ взглянуть на шаблон поворота, которому вы должны следовать, заключается в следующем: метка, противоположная метка, верхняя и нижняя стороны этикетки, а также правая и затем левая стороны этикетки.
Вот описание того, как использовать подушечки Abralon на шаре для боулинга, когда мяч уже находится в спиннере:
- Влажные подушечки и мяч : Чтобы защитить руки от тепла, трение между шлифовальной подушкой и мячом создаст и сведет к минимуму распространение пыли, сбрызните свой шар водой и окуните подушечку Abralon в воду.Использование воды на протяжении всего времени шлифования также смывает отслоившиеся частицы, образующиеся при шлифовании, что в целом сделает шлифование более равномерным.
- Установите скорость вертушки : если у вашего вертушечника две скорости, установите самую низкую скорость во время шлифования. Если вы наносите состав или полироль, вертушку следует установить на максимальную скорость. Если у вашего спиннера только одна скорость, вы все равно можете нанести им состав или полироль.
- Подушечка Palm Abralon : Очень важно, чтобы вы правильно держали подушечку Abralon, с которой работаете.Держите подушечку на шаре для боулинга только ладонью. Перемещая подушечку пальцами вверх и вниз по шару для боулинга во время шлифования, вы рискуете получить серьезную травму, если один из ваших пальцев застрянет в одном из отверстий для шара.
- Приложите давление : Вам нужно будет надавить на подушечку Abralon, чтобы добиться желаемых результатов шлифовки. Как правило, вы должны прикладывать большее давление в течение более коротких периодов времени, когда используете подушечки с меньшим зерном.Когда вы шлифуете дисками с более высоким уровнем абразивности, вы должны прикладывать меньшее давление в течение более длительного времени.
- Шлифование по времени : Хотя обычно вы хотите продолжать шлифование до тех пор, пока вы не перестанете видеть линии, идущие в противоположном направлении от того, в котором вы работаете, очень важно отшлифовать каждую область вашего шар для боулинга равномерно. Вы можете убедиться, что делаете это, мысленно подсчитывая время, которое вы тратите на работу с мячом в каждой из упомянутых выше позиций.
- Изменить зернистость : В зависимости от ваших целей шлифовки вам может потребоваться сменить подушечки для работы с другим уровнем зернистости. Убедитесь, что вы отшлифовали всю поверхность шара для боулинга имеющейся зернистостью, прежде чем переходить на более высокий или более низкий уровень зернистости.
Хотя есть споры о том, следует ли вам последовательно использовать более высокую зернистость или можно пропустить один или два уровня, прежде чем использовать наивысший уровень зернистости, с которым вы намеревались закончить, настоятельно рекомендуется избегать использования зернистости, которая более 1.В 5 раз более гладкий, чем тот, который вы только что закончили использовать. Например, вы должны использовать пэд Abralon с зернистостью 2000 после использования пэда 1,000G и до использования пэда 4,000G вместо того, чтобы перемещаться непосредственно с пэда 1000G на пэд 4000G.
Если вы шлифуете до более низкой зернистости, вы можете начать с самой низкой зернистости, которую планируете использовать, но убедитесь, что вы используете новую площадку. Использовать использованные подушечки уместно только тогда, когда вы шлифуете до более низкой зернистости в последовательности шагов, и использованная подушечка будет использоваться на промежуточном этапе, а не на последнем.
- Нанесите компаунд : После того, как вы закончили шлифование, самое время нанести компаунд, если вы хотите это сделать. Применение компаунда обеспечит полный контакт шара для боулинга с дорожкой во время игры. Установите вертушку на высокую скорость и с помощью ткани нанесите равное количество продукта на мяч, продолжая вращать его в соответствии с ранее предписанным способом.
- Нанесите полироль : После того, как вы нанесли состав, используйте отдельную ткань для нанесения полироли. Смесь придаст вашему шару для боулинга блеск, а полироль — липкую поверхность.Полировка также обычно помогает вашему мячу иметь резкую реакцию на бэкэнде, когда вы играете в боулинг.
- Очистите свой мяч : Заключительная часть восстановления поверхности шара для боулинга — его очистка. Для чистки шара для боулинга необязательно использовать спиннер. Просто нанесите на него немного чистящего средства и протрите мяч неиспользованной тканью. Не забудьте очистить отверстия для пальцев вашего мяча, а также его внешнюю поверхность.
Бренды, которым мы доверяем
SIA Воздушные диски и шлифовальные диски Abralon в National Abrasives, Inc.Если вы собираетесь обработать шар для боулинга вручную, свяжитесь с National Abrasives, Inc. сегодня. Наши дружелюбные и услужливые представители службы поддержки клиентов помогут обеспечить вас необходимыми шлифовальными принадлежностями, чтобы ваш мяч работал так, как вы хотите.
Семейная компания National Abrasives, Inc. предлагает конкурентоспособные цены, бесплатные образцы продукции и даже бесплатную доставку при минимальных покупках. Наши воздушные диски SIA идеально подходят для мокрого или сухого шлифования, в том числе для шлифовки вашего шара для боулинга.Известные своим исключительно долгим сроком службы, малой глубиной царапин и проницаемостью, вы можете снова и снова использовать наши 6-дюймовые водонепроницаемые воздушные диски SIA, чтобы обновлять поверхность своего шара для боулинга.
В наш широкий выбор шлифовальных тарелок и дисков Mirka Abralon входят диски для захвата из пеноматериала Mirka Abralon следующих размеров: 3, 6, 9 и 12 дюймов. Собираетесь ли вы использовать эти продукты для восстановления поверхности шара для боулинга без вертушки или собираетесь использовать вертушку для восстановления поверхности, эти продукты будут обеспечивать равномерный внешний вид каждый раз, когда вы их используете.Если вы купите определенное количество подушечек Mirka Abralon, вы получите право на оптовую скидку и бесплатную доставку. Свяжитесь с нашей командой отличных представителей службы поддержки клиентов, чтобы узнать больше сегодня.
В National Abrasives, Inc. удовлетворение потребностей клиентов всегда является нашим главным приоритетом. Лэнс Томас из IPG из Йорка, штат Пенсильвания, недавно сказал следующее о нашей компании:
«Мы закупаем расходные материалы у National Abrasives в течение последних 12 лет. Их способность хранить необычные товары позволяет нам быстро реагировать на требовательные потребности и сроки наших клиентов.Мы также во многом полагаемся на National — будь то 5 ремней или 500, они всегда проходят ».
Так же, как мы поставляем для IPG в течение многих лет, мы готовы доставить и для вас. У нас есть все необходимое для шлифовки, чтобы ваш шар для боулинга работал с максимальной эффективностью. Если до следующего турнира всего несколько дней или вы не планируете играть в течение нескольких недель, мы позаботимся о том, чтобы у вас были все необходимые продукты, когда они вам понадобятся. Свяжитесь с нами сегодня.
Сортировать по типу
Узнать больше об абразивных материалах для шаров для боулинга ДОЛЯ:Рекомендации по контролю за инфекциями в салоне
Обратите внимание, что вы можете преобразовать эту страницу на другой язык, нажав кнопку «Язык + Настройки» в правом верхнем углу выше.
Руководство по плану профилактики и контроля инфекций для ногтей техников, ресниц, косметологов, парикмахеров, косметологов, и парикмахеры
ОбязанностиЭто ваша ответственность как лицензиата и / или салона красоты. собственнику поддерживать санитарные условия там, где предоставляются услуги для защита ваших клиентов и вас.
Ручная стиркаВымойте руки водой с мылом, затем вытрите одноразовое бумажное или тканевое полотенце или сушилка для воздуха, прежде чем предоставлять какие-либо услуга.Можно использовать средство для рук на спиртовой основе (не менее 60%). спиртом) вместо мытья рук только тогда, когда ваши руки свободны от лосьонов, мази, средства или видимые загрязнения. Перчатки и салфетки для рук не заменяют мытье рук.
Очистка
Перед дезинфекцией необходимо очистить любой предмет или поверхность. Это значит, что ты должен:Удалите видимый мусор и одноразовые детали. Вымойте предмет или поверхность. водой с мылом или чистящим средством.После стирки ополосните изделие тщательно и полностью высушите перед дезинфекцией. Поверхности могут быть протирать чистящим средством перед дезинфекцией. Если чистящее средство или продукт не в оригинале контейнер, вы должны промаркировать его с названием продукта и использования инструкции. В противном случае, если исходный контейнер все еще доступен, вы делаете не нужно повторно маркировать новый контейнер инструкциями по применению.
Дезинфекция
Перед дезинфекцией все предметы необходимо очистить.
- Вы должны использовать дезинфицирующее средство, зарегистрирован EPA для использования в больницах и имеет маркировку бактерицидный, вирулицидный и фунгицидный. Сам по себе алкоголь неприемлем дезинфицирующее средство.
- Вы должны использовать дезинфицирующее средство в соответствии с инструкции производителя, которые включают время контакта, меры безопасности, требования к разбавлению (если таковые имеются) и надлежащая утилизация.
- Все дезинфицирующие растворы должны быть разборчивыми. помечены названием дезинфицирующего средства и любыми требованиями к разбавлению.В дезинфицирующие растворы необходимо готовить ежедневно и утилизировать в конце дня или немедленно, если присутствуют видимые загрязнения. Если концентрированные дезинфицирующие средства необходимо быть разбавленным водой, измерительные приборы должны быть легкодоступны и использоваться для обеспечить эффективное решение.
- Чтобы вылечить инструмент или приспособление, необходимо: полностью погрузите все поверхности инструмента или приспособления, включая рукоятки, в дезинфицирующее средство в закрытом контейнере на все время контакта, указанное в указания производителя.После дезинфекции предметы необходимо промыть и сушеные.
- В каждом салоне должно быть дезинфицирующее средство. контейнеры с крышками. Контейнеры должны быть достаточно большими, чтобы полностью погрузиться в воду. инструменты и инструменты в дезинфицирующем средстве. Количество крытых контейнеров и размер контейнеров должен быть достаточным, чтобы вместить все приспособления и инструменты, которые нужно продезинфицировать.
- Вы должны носить перчатки или использовать щипцы, чтобы избежать прямого контакта кожи с дезинфицирующим средством, и соблюдать все меры безопасности, указанные в инструкциях производителя .
Воздействие крови и биологических жидкостей
.
Вы должны прекратить обслуживание, если произойдет неожиданный порез, ссадина или другая травма во время службы и приводит к контакту с кровью или другими биологическими жидкостями или когда другие жидкости в организме появляются в результате оказания услуги. Затем выполните шаги с A по G:A. Наденьте перчатки.
B. Если возможно, промойте рану проточной водой.
C. Очистите рану антисептическим раствором и накрыть стерильной повязкой.
D. Если рана на руке, наденьте перчатку или палец. прикрыть рану. Если рана находится на клиенте, наденьте перчатки на обе руки
, чтобы завершить обслуживание.
E. Поместите окровавленную ткань, вату или другую Материал, загрязненный кровью или биологическими жидкостями, поместить в пластиковый пакет, затем запечатать и выбросить сумку.
F. Перед возобновлением обслуживания снимите все оборудование, инструменты и приспособления, контактировавшие с кровью или другими биологическими жидкостями.
G. Очистите и продезинфицируйте все загрязненные поверхности, затем Мойте ваши руки с мылом и водой.Загрязненные инструменты, приспособления и оборудование должны быть очищенным и продезинфицированным, как описано выше
Хранение предметов (подраздел 6)
- Вся чистая и продезинфицированная посуда / инструменты. и материал, когда он не используется, должны храниться в чистом, сухом, свободном от мусора среда, которая включает, помимо прочего, ящики, ящики, пояс для инструментов, роликовые лотки. Их необходимо хранить отдельно от загрязненных. посуда / инструменты. Ультрафиолетовые (УФ) электрические дезинфицирующие средства допустимы для использовать как контейнер для сухого хранения, а не как форму дезинфекции.
- Обеззараженные предметы не должны попадать в контакт с зараженными или недезинфицированными предметами. Сюда входят предметы, которые вы подготовить к использованию прямо перед службой; они не должны контактировать с поверхности, не прошедшие дезинфекцию
Практика безопасности и инфекционного контроля
Относительно инструментов:
Вы должны использовать только очищенные, продезинфицированные и правильно хранимые инструменты и инвентарь на клиентах.
Ваш салон должен иметь запас доступны продезинфицированные инструменты, продезинфицированные инструменты и одноразовые расходные материалы для использования практикующими врачами.Предложение должно быть достаточным в зависимости от обслуживания. объем, чтобы гарантировать обслуживание каждого клиента с должным образом очищенными и продезинфицированными инструменты и инвентарь каждый день
Инструменты или приспособления упали на пол или в противном случае загрязненные во время обслуживания должны быть удалены с рабочей станции, очищены и продезинфицированы или помещены в закрытый контейнер с этикеткой «использовались» до очистки и дезинфекции
Касательно продукции:
- Все жидкости, полужидкости, кремы, воски и порошки должны храниться в чистых закрытых контейнерах с твердой крышкой и должны раздавать таким образом, чтобы предотвратить загрязнение неиспользованного запаса.
- Нельзя использовать пальцы для вынуть продукт из контейнеров. Вместо этого вы должны использовать одноразовые или продезинфицированные шпатели или аппликаторы. Шпатели, аппликаторы или совки нельзя хранить в контейнер
- Если товар удален из контейнера, его нельзя класть обратно в контейнер. Вместо этого, если это неиспользованный, его необходимо выбросить или утилизировать.
- Поверхности контейнеров необходимо очистить и продезинфицировать дезинфицирующим средством. протирать в конце дня.
- Все продукты должны иметь четкую маркировку, включая те, которые не были в оригинальной упаковке.
- Косметический карандаш необходимо заточить перед каждое использование дезинфицированной точилкой для карандашей. Когда косметика карандашного типа находится в механический аппликатор или диаметр слишком мал для заточки, Открытый кончик продукта необходимо удалить дезинфицированными ножницами или нож, а кончик аппликатора протереть спиртом перед использованием на другом клиент.
- Вы должны соблюдать все инструкции производителя. инструкции по использованию продукта. Когда в инструкции к продукту требуется тест на исправление, вы должен (1) предложить патч-тест и (2) предоставить информацию клиенту относительно риска возможных побочных реакций на продукт
По клиентам, животным, продуктам питания и напиткам:
- Не следует оказывать услуги клиентам с открытыми ранами или язвочками в обслуживаемой области тела.
- Животные не допускаются в салоны.Этот запрет не распространяется на служебных животных, как это определено Общие статуты Коннектикута, Закон об американцах с ограниченными возможностями (ADA) и соответствующие правила.
- Рыба живая, пиявки, улитки и др. живые существа не должны использоваться в косметических услугах.
- Открытые продукты питания и напитки не допускаются. в присутствии непокрытых дезинфицирующих растворов или при дезинфекции растворы производятся или утилизируются, или когда используются дезинфицирующие спреи.
- Запрещается есть и курить, в том числе электронные сигареты, при выполнении любых услуг. Ты можешь пить безалкогольные напитки при оказании услуг, но ваш напиток должен быть накрывается крышкой.
Постиранные предметы (подраздел 8)
- Стирка с моющим средством и горячая вода в стиральной машине
- Высушено в сушилке для белья при максимальной температуре
- Незамедлительно хранить в чистом закрытом контейнере
- Пластиковые или нейлоновые накидки и фартуки можно стирать. в машине и сушить на любой установке в сушилке или можно продезинфицировать спрей дезинфицирующий.
- Вы должны хранить использованные или грязные полотенца, белье и накидки в закрытых контейнерах с пометкой «использовалось».
- Полотенца и другие предметы стирки должны быть правильно очищены и хранятся. Коммерческая услуга постельного белья используется, если: не сделано в помещении.
Ножницы и бритвы
Ножницы и бритвы мыть не нужно, протереть, чтобы удалить волосы, остатки продукта и остатки кожи, а затем продезинфицировать с зарегистрированным EPA дезинфицирующим спреем для больниц или протирать после каждого использовать.Поверхности должны оставаться влажными от спрея или дезинфицирующего средства для протирки. Время контакта указано на этикетке дезинфицирующего средства.
Электрические и электронные инструменты (подраздел 11)
Машинки для стрижки ногтей, сверла для ногтей, утюги, фены, стеклянные или металлические электроды, высокочастотные палочки, эстетические машины, пароварки, диффузоры или другие электрические или электронные инструменты должны быть очищены и дезинфицировать после каждого использования, включая корпус, ручку и прикрепленный шнур.
Для очистки и дезинфекции электрических и электронных инструментов, после каждого использования:
- Удалить все съемные детали (пластиковые ограждения, съемные неметаллические детали, металлические ограждения, лезвия машинки для стрижки, сверла и др.).
- Вытрите или почистите все изделие щеткой. остатки, волосы, остатки кожи, пыль от ногтей и другой видимый мусор от поверхность инструмента.
- Продезинфицировать предмет поверхности (включая корпус, ручку и шнур) и съемные части с Зарегистрированный EPA дезинфицирующий спрей или салфетка для больниц. Лезвия для стрижки, которые не снимаются, волосы необходимо удалить дезинфицированной щеткой или мытье лезвия, а лезвие машинки необходимо продезинфицировать в больничном дезинфицирующий спрей.Поверхности должны оставаться влажными от спрея или протирать. дезинфицирующее средство на время контакта, указанное на этикетке дезинфицирующего средства. Как всегда, вы должны следовать указаниям производителя.
Дезинфицированные электрические и электронные инструменты должны быть хранится, когда не используется. Приемлемое хранение включает чистую и продезинфицированную поверхность, подставка или крючок, или закрытый контейнер, шкаф или ящик.
Ванночки для педикюра (ванны для ног, ванны для ног и спа лайнеры) необходимо очищать и дезинфицировать после каждого клиента, используя эту последовательность независимо от используемых лайнеров:
- Слить всю воду и весь мусор. должны быть удалены из бассейна.
- Затем ванночку для педикюра необходимо очистить мыло или моющее средство и вода, все съемные части необходимо снять для дальнейшего использования. уборка. (сюда входят: крышки форсунок и экраны).
- Бассейн спа необходимо продезинфицировать Зарегистрированное EPA дезинфицирующее средство с бактерицидным, фунгицидным и вирулицидным действием. активность, используемая в соответствии с инструкциями производителя. Обычно 10 требуется время контакта в минутах, гидромассажные форсунки с рециркуляционной водой должны быть заполнены и включены для надлежащей дезинфекции.Пожалуйста, выберите эту ссылку для фото.
- Раковину необходимо насухо протереть чистое полотенце или дать достаточно высохнуть на воздухе.
Предметы одноразового использования
Следующие предметы считаются предметами одноразового использования, их можно использовать один раз только и должны быть немедленно выброшены в мусорное ведро после каждого обслуживания:- Сепараторы из пеноматериала
- Буферные блоки из пеноматериала
- Вкладыши для педикюра
- Пемза или куски пемзы
- Вьетнамки из замши, бумаги или поролона или тапочки
- Пилки для ногтей, если они не металлические, класса или кристалл
- Керамические пилки для ногтей, если они не запломбированы полностью глазурью
- Шлифовальные ленты или втулки
- Сверла для бумаги по наждачной бумаге
- Аппликаторы деревянные
- Ватные диски, ватные диски или тампоны
- Подушечки марлевые
- Губки
- Нашейные ленты
- Восковые полоски
- Прочие изделия из бумаги, дерева, пенопласта или другие пористые материалы
Требования к одноразовым изделиям:
- Вы должны хранить все новые одноразовые предметы в чистые закрытые емкости с твердыми стенками и крышками, содержащие только новые или продезинфицированные предметы.Вы можете хранить новинки в оригинальной закрытой упаковке. на открытом воздухе, например, в приемной.
- Для надрезания кромок острые одноразовые файлы, вы можете использовать один файл несколько раз, чтобы подпилить край запаса новых файлов при условии использования перчаток при подготовке новые файлы и файл партитуры хранится в амбулатории в продезинфицированный контейнер с надписью «файл с очками». В каждом салоне может быть только один файл партитуры.
Воск и парафин
Во время восковой службы:
- Необходимо использовать шпатели одноразовые, деревянные. палочки и аппликаторы только один раз, затем выбросьте инструмент, не используя другой конец.Никакого двойного окунания! Единственное исключение — если вы используете одноразовый воск и выбросьте воск сразу после службы.
- Вы должны дозировать парафин который предотвращает загрязнение неиспользованного расходного материала, например, в сумке или другом контейнер для использования клиентом в качестве единой службы.
После восковой службы:
- Любая поверхность, к которой прикасается использованная восковая палочка. необходимо очистить и продезинфицировать сразу после службы.
- Восковые горшки и подогреватели парафина должны быть сохранены. покрытые и внешняя чистка, по крайней мере, ежедневно.
- Если воск или парафин содержит мусор или был загрязнен в результате контакта с кожей, нечистыми аппликаторами или двойное погружение, восковую емкость или подогреватель парафина необходимо опорожнить и продезинфицировать и воск необходимо выбросить.
Приспособления, требующие ежедневной очистки и дезинфекции, использовать зарегистрированные EPA дезинфицирующие салфетки или спреи для больниц с поверхность мокрая на время контакта по указаниям производителя:
- Кресла стилиста в парикмахерских
- Стулья на шампунных станциях
- Кресло маникюрное
- Трон для педикюра
- Раковины и чаши для шампуня, включая смеситель: ручки, распылители, внутренняя часть чаш, внешние поверхности.Волосы необходимо удалить из мисок шампуня сразу после каждого использования шампуня.
- Тележки роликовые
- Подносы рабочие
- Другие контейнеры, используемые для хранения инструментов и инструменты во время ухода за волосами, кожей, воском, ногтей, педикюра или других услуг
- Полотенцесушители. Дополнительно:
- Полотенца необходимо стирать с моющим средством и отбеливателем, затем высушите в горячей сушилке;
- Практикующие готовят полотенца для утеплителей необходимо мыть руки или надевать перчатки; и
- Влажные полотенца, используемые в услуги должны быть приготовлены свежими каждый день.В конце дня неиспользованные приготовленные на пару полотенца необходимо снять и постирать.
Крепления должны быть защищены от контакта с кожей чистой тканью, бумажным полотенцем или простыней И , подлежащей очистке и дезинфицировать ежедневно с использованием дезинфицирующих салфеток, зарегистрированных в EPA, или распыляет с влажной поверхностью на время контакта в заводской направления:
Рабочие поверхности, на которых выполняются услуги
- Чаши для шампуня
- Столики для ногтей
- Кресла или кровати для лица
- Кресла или кровати для депиляции
ВАЖНО : При контакте с кожей клиента с поверхностью необходимо очистить и продезинфицировать поверхность сразу после услуга.
Сразу после обслуживания волосы и мусор необходимо удалить. снят с пола.
Запрещенное оборудование:
- Оборудование для снятия шкур, в т.ч. бритвенные бритвы для мозолей, лезвия для кредо, рашпили или терки и другие инструменты которые используются для удаления натоптышей или мозолей путем разрезания ниже поверхности кожи
- Шариковый воск
- Шариковый воск одноразового использования Картриджи приемлемы, но должны быть утилизированы сразу после обслуживания.При нагревании в восковом нагревателе шариковые восковые картриджи должны иметь неповрежденную пломбу. В Нагревательный элемент необходимо очищать и дезинфицировать после каждого использования.
- УФ-стерилизаторы или световые короба
- Это неприемлемо устройства для инфекционного контроля и не должны присутствовать в салоне (на странице 2 мы говорим что УФ-стерилизаторы допустимы в качестве контейнера для сухого хранения)
- Это не относится к УФ-излучению. сушилки или ультрафиолетовые лампы, используемые для сушки или отверждения ногтей.
- Напильники или дрели электрические или на батарейках не производятся специально для использования на людях
Как превратить свой кулак в машину для разбивания блоков
Немногие вещи в жизни могут предложить более интуитивное доказательство силы физики, чем удар карате. Пробейте кирпич голой рукой, и если вы неопытны в боевых искусствах, вы можете сломать палец. Ударьте по нему с соответствующей силой, импульсом и положением, и вместо этого вы сломаете кирпич. «Удивительно, но здесь нет никаких уловок, — говорит Майкл Фельд, физик из Массачусетского технологического института.«Перед вами одно из самых эффективных человеческих движений, когда-либо задуманных».
В конце 1970-х, когда Фельд зарабатывал коричневый пояс по карате, его инструктор Рональд Макнейр тоже был его студентом-физиком. (Макнейр умер в 1986 году, работая ученым-астронавтом на борту космического корабля «Челленджер».) Оба мужчины согласились, что секрет карате заключается в скорости и сосредоточенности удара. Но насколько быстро движется удар карате? Чтобы выяснить это, они присоединились к студенту Стивену Уилку и установили стробоскоп, который мигал 60 или 120 раз в секунду.Затем они сфотографировали Макнейра и других, наносящих удары руками и ногами, и подсчитали, сколько раз мигал стробоскоп, пока ступня или кулак не попали в цель.
Фельд и Макнейр обнаружили, что начинающие ученики могут бросать отбивную каратэ со скоростью около 20 футов в секунду, что достаточно, чтобы сломать доску толщиной в один дюйм. Но такой черный пояс, как Макнейр, мог рубить со скоростью 46 футов в секунду. Ударяя по дереву с такой скоростью, рука весом в 11/2 фунта может нанести удар силой до 2800 ньютонов (один ньютон примерно равен силе, прилагаемой к весу яблока).На раскол типичной бетонной плиты толщиной 11/2 дюйма на самом деле требуется меньше, примерно 1900 ньютонов. Конечно, грубая прочность — не единственное требование для разрушения бетонных блоков — важен также характер скола. Ученики каратэ должны усвоить, что для того, чтобы удар имел максимальную силу, он должен иметь завершение; по той же причине игроки в гольф и теннис продолжают свои качели.
Чтобы понять, как работает последующая работа, Джерл Уокер, бывшая студентка таэквондо, которая сейчас преподает физику в Государственном университете Кливленда, организовала исследование, во многом похожее на исследование Фельда и Макнейра.Он обнаружил, что хорошо брошенный кулак достигает максимальной скорости, когда рука вытянута примерно на 80 процентов. «Это именно то, чему меня научил мой мастер таэквондо», — говорит Уокер. «Вы сосредотачиваете свой удар в своем воображении так, чтобы он оканчивался внутри тела вашего противника, а не на поверхности. Чтобы обеспечить максимальную мощность, вам нужно установить контакт до того, как начнется замедление ».
То, что происходит после контакта, также очень важно. Все материалы хоть немного эластичны: ударьте их в нужном месте, и они начнут колебаться.«Если вы поворачиваете резиновую ленту, она движется вверх и вниз, и то же самое верно, если вы настраиваете доску или кирпич с гораздо большей силой», — говорит Фельд. «Когда они достигают предела эластичности, они начинают податливаться. Другими словами, они ломаются ».
К счастью для нас, достичь эквивалентного предела в костях тела нелегко. Фельд говорит, что кость может выдержать в 40 раз большую силу, чем бетон, а костяной цилиндр диаметром менее дюйма и длиной 21/3 дюйма может выдержать силу в 25000 ньютонов.Руки и ноги могут подвергнуться еще большему насилию, потому что кожа, мышцы, связки, сухожилия и хрящи поглощают большую часть ударов. Нога с хорошим ударом может поглотить примерно в 2000 раз больше силы, чем бетон, прежде чем она сломается. Фельд ни разу не сломал палец в карате, хотя однажды он сломал восемь досок толщиной в один дюйм за раз.
Если учащиеся хотят разбивать доски, они должны не только увеличить скорость и улучшить прицеливание, но и укрепить свои руки и ноги, ударив их о столб, обернутый пеной и брезентом.«Вначале ваша кожа такая мягкая, что вы можете ее порезать. А потом идет кровь », — говорит гроссмейстер тхэквондо Сихак Генри Чо. «Это не рекомендуется». Со временем на шуто, или острие руки, образуется мозоль, которая действует точно так же, как автомобильный бампер, поглощая и рассеивая силу столкновения.
Важный урок для потенциальных черных поясов заключается в том, что физика нуждается в небольшой помощи с упорством. «Тайгер Вудс не просто проснулся однажды утром и начал отбивать мяч на расстоянии 320 ярдов, и мы не просто зашли и разбили шлакоблок», — говорит Чо.«Каждый должен над этим работать».
Изготовление собственной ручки без токарного станка
Инструкции Алисы Венигер из Alice’s Workshop Изготовить ручки очень просто, недорого и не требует много времени. Отличный подарок в любое время года. Ручка может быть изготовлена менее чем за час без токарного станка , используя описанную ниже технику. В идеале вы должны использовать токарный станок и токарный набор для поворота ручек, но не у всех есть место для большой инструмент, или они просто не могут себе этого позволить.Необходимые инструменты и материалы: